Keba is Down to the last micron Automation for probably the most precise printing cylinders in the world
They want precision. They want extreme precision. “Micron” must be the most frequently used word at Daetwyler Graphics AG at their plant in Oftringen in Switzerland.
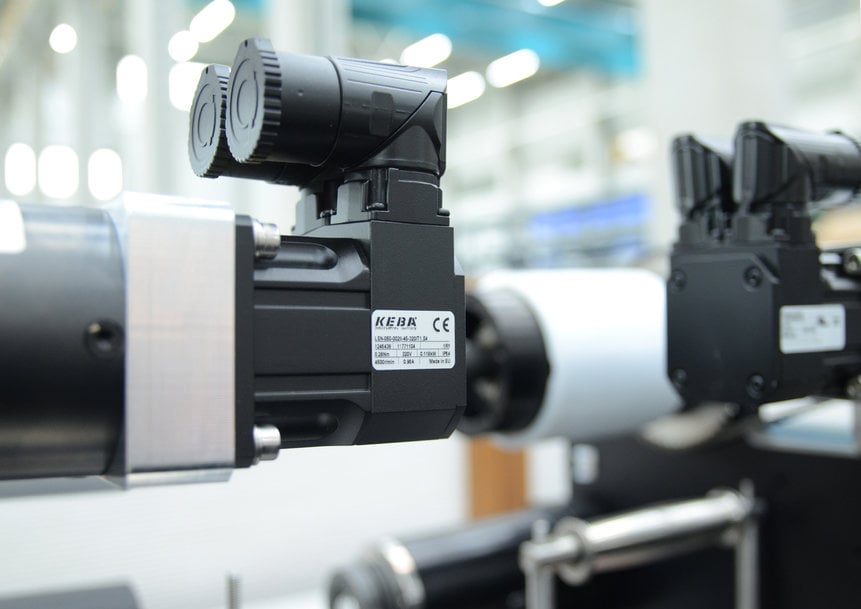
KEBA servo motor with great dynamic and power in a very compact design.
Here, a 60-strong workforce painstakingly develops and builds about 60 turning and grinding systems annually that are used for the manufacturing and processing of rotogravure cylinders (printing cylinders with engraved images) used in printing presses for intaglio printing. The company is part of Heliograph Holding and generates an annual revenue of about 15 million euros.
Rotogravure is used mainly for printing jobs in which visuals and/or security play an important role. This is true for example in the case of flexible packaging, such as in the cigarette industry, or in the case of printing banknotes and securities. The technique is also used in high-volume catalog printing. The export rate is very high. Daetwyler Graphics’ most important market is Asia.
Companies that operate the systems made by Daetwyler make the most precise printing cylinders in the world. Such systems must ensure that end customers will be able to treat and process their cylinders with a precision in the micrometer range. The tolerance range is 10 µm cylindrically and 5–10 µm for the diameter, depending on the cylinder size. In order to achieve this, the guides of the machine are straightened with a precision of about 3 µm. If the cylinder does not rotate with the highest precision in the printing press, colors will deviate or be missing altogether. In other words, the bar is very high when it comes to quality, and this also counts for components such as drives and controllers.
Hansjörg Michel, Head of Technology, Daetwyler Graphics AG: “KEBA’s employees are closely involved with the product. This enables them to provide quick, professional consultation. They don't forward your call to an endless string of people. Instead, as a customer you get to talk to an expert at eye level.”
Info box: How does gravure printing work?
Gravure printing involves three steps:
- The printing plate or printing cylinder with the desired images is fully covered with ink.
- A squeege
- E is then used to scrape the ink off the surface. The ink remains only in the recessed sections, i.e. the actual printing elements.
- Ink transfer: With a strong press-on force and through the absorbency of the paper, the ink is transferred to the print medium.
Daetwyler and KEBA
Head of Technology at Daetwyler Graphics, explains: “Heliograph Holding has been using controllers made by LTI Motion GmbH (note: part of KEBA since 2019) for years. At an SPS trade fair, our developer team discovered the KEBA controllers and was fascinated by their compact design.” The business relationship became even closer in 2017 when Daetwyler Graphics’ main supplier of motion controllers discontinued a product and could not readily provide a substitute that satisfied Daetwyler’s requirements.
Michel: “The proposed solution would have meant going back to the drawing board: starting development over from scratch. For this reason, we called for bids from our existing suppliers and asked them to develop a concept and submit an offer.” In total, six automation specialists were contacted and participated in the bidding process. Michel: “KEBA won the bid – not because theirs was the lowest price, incidentally they came in second on that count, but because the overall package was right and they provided other persuasive benefits.”
Belt grinding drive with excellent synchronism through KEBA servo system.
Automation does not happen in isolation Flexibility & openness in a compact design
KEBA’s Kemro X hardware and software platform comes with open interfaces as standard. This makes these solutions open to other applications, both proprietary and third-party. Customers can thus make their own decisions about which technologies to use where, which technologies they wish to protect and in what areas they are willing to accept dependencies. This approach ensures sustainable automation solutions while at the same time safeguarding the company’s flexibility. Michel: “Other automation providers offer single-source solutions, but they act like isolationists at the product level: They make it impossible to integrate third-party or proprietary applications, which is a massive drawback.”
Another boon when comparing the bids was the principle of built-in safety in the KEBA – in other words, the required SLS safe stop protocols etc. are already included in the basic control system and all controllers come with the necessary safe inputs.
Because KEBA puts as much intelligence as possible into each component, they can save a lot of space in construction. This compact design was a crucial benefit. Michel: Support for Codesys, for example, was very important. My condition, however, was that Codesys needed to be integrated into the control system rather than use a separate PC.
If we keep rigorously to this compact design approach, about 30 % of space can be saved in the control cabinet.” Shrinking the control cabinet to this much more compact size allows Daetwyler Graphics greater freedom in the design of new systems – a critical factor in particular for smaller system types. Size is not the only benefit – the uniform design of the KEBA components also helps machine manufacturers. Michel: “Regardless of which KEBA controller we install, whether servo controllers or frequency controllers, they all have the same dimensions and the same shape. This is a massive help in our design process. Daetwyler Graphics is already planning their new product series on this basis.
The optimized size of the KEBA drives and the multi-axis system on a single power supply have massively reduced the size of the control cabinet and the required wiring effort. This saves Daetwyler Graphics time and money.
Unique: Team and culture
“What we particularly enjoy about working with KEBA is the easy communication,” says Mr. Michel. “Our point of contact in Switzerland takes care of all our concerns and gets back quickly to us with feedback. This works great and goes very smoothly because he in turn has direct points of contact within the company and a very short communication chain.” What else does Daetwyler like about their partner KEBA? The fact that KEBA has great vertical integration and extremely knowledgeable staff.
Michel: “During the consultation talks in the preparation phase, we can really feel that KEBA is itself a manufacturing company and produces for example circuit boards.” The experts work where the products are built. And this massive benefit is also tangible later when working with the support team. “KEBA’s employees are closely involved with the product. This enables them to provide quick, professional consultation. They don't forward your call to an endless string of people. Instead, as a customer you get to talk to an expert at eye level.” How would he describe the cooperation with KEBA in just a few words? “Open, honest, cooperative and customer-friendly,” is the lightning-quick answer. Mr. Michels emphasizes that this is true for the KEBA office in Switzerland as much as for the teams in Germany and Austria.
www.keba.com