www.ptreview.co.uk
24
'21
Written on Modified on
ExOne and SSI Partner to Drive Volume Production with Metal Binder Jetting
International supplier of high-performance metal products for automotive and industrial markets, SSI Sintered Specialties purchases X1 160Pro and InnoventPro® 3L metal 3D printers for production and is now partnering with ExOne to advance the technology.
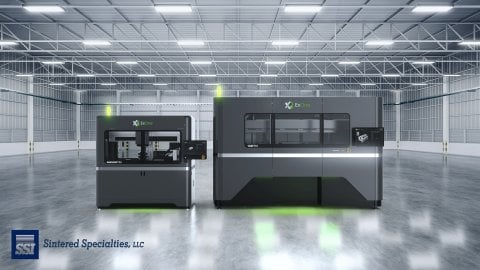
The ExOne Company (Nasdaq: XONE), the global leader in industrial sand and metal 3D printers using binder jetting technology, today announced that SSI Sintered Specialties, a leading metallurgical solutions partner, has purchased an X1 160Pro and InnoventPro 3L metal binder jetting system featuring ExOne's patented Triple Advanced Compaction Technology (ACT).
The two ExOne printers are slated for delivery in the first half of 2022 and will be located at the company’s Headquarters in Janesville, WI. SSI’s 250,000-square-foot facility also houses the world’s largest installed capacity of high temperature sintering furnaces — a process step core to metal binder jetting – and post-processing technology to support volume production in metal binder jetting.
“The addition of metal binder jetting to SSI’s technology portfolio was the natural next step in providing our customers with the most advanced technology on the market to produce complex geometries in volume production,” said Paul Hauck, SSI Sintered Specialties COO. “Our expertise and lengthy heritage in high temperature metallurgy processing is a perfect fit for binder jetting technology, and we are thrilled to be working with ExOne to offer our customers the future of metal 3D printing.”
SSI has over 40 years of powder metallurgy experience and metal 3D printing adds to the company’s existing capabilities in Press and Sinter powder metallurgy and nontraditional Metal Injection Molding. With ExOne’s 3D printers and SSI’s furnace and sintering capabilities, the parts manufacturer will offer components with increased complexity and size for volume production with no tooling in a variety of metals.
The investment in ExOne’s binder jet technology is just one of the steps in SSI’s business strategy to embrace additive manufacturing and bring new manufacturing solutions for volume production.
“ExOne is delighted to have our cutting-edge binder jet technology adopted by such an experienced powder metallurgy partner and high-quality parts supplier such as SSI,” said John Hartner, ExOne CEO. “We look forward to driving binder jetting to full production for a wide range of customers who will now be able to unlock new value with innovative new designs that were once impossible or too expensive to produce with traditional manufacturing.”
In addition to serving customers, SSI and ExOne will now be collaborating in a variety of binder jet material, automation, and process areas. SSI will use the InnoventPro for material and application development, with the 160Pro dedicated to volume production through a fully automated cell with continuous sintering and state-of-the-art furnace equipment.
To date, ExOne has qualified more than 20 materials for its binder jetting process, including 12 metals, 5 composites, and 4 ceramics. Aside from stainless and tool steels such as 17-4PH, 316L, M2 and H13, ExOne has qualified Inconel 625, aluminum 6061, copper and more.
Binder jet additive manufacturing is a method of 3D printing in which a digital file is used to quickly inkjet a binder into a bed of powder particles — such as metal, sand, or ceramic — to create a solid part, one thin layer at a time. When printing metals, the final bound metal part must be sintered in a furnace to fuse the particles together into a solid object. Binder jetting is highly similar to MIM and PM manufacturing techniques, with the exception that the pre-sintered part is 3D printed rather than being formed by a press or molding. ExOne’s Triple ACT ensures high consistency, repeatability, and quality in the printed part.
The InnoventPro 3L, which features a build area of 220 x 125 x 100 mm (8.7 x 4.9 x 3.9 in), is slated for delivery in the first half of 2022 and will be the world’s most advanced metal binder jetting system with the capability to print ExOne’s groundbreaking NanoFuse™ particulate binders. The X1 160Pro is the world’s largest metal binder jetting system with a build area of 800 x 500 x 400 mm (31.5 x 19.7 x 15.8 in) and offers the most qualified materials. The two systems use the same printheads, so customers can easily scale their R&D on the InnoventPro to production with the 160Pro.
ExOne has now sold multiple X1 160Pro printers to customers in the food and beverage, automotive, consumer goods, and energy industries, with factory acceptance tests now underway.
www.exone.com