www.ptreview.co.uk
02
'21
Written on Modified on
Smart Measurement for Smart Manufacturing: The New Mantra
A Quick Dive Into Multi Sensor Measurement of Multi-pole Connectors. By Goh Kah Khoon, Vice President of Sales & Manufacturing Business Unit, Hexagon Manufacturing Intelligence, Korea, ASEAN, Pacific & India.
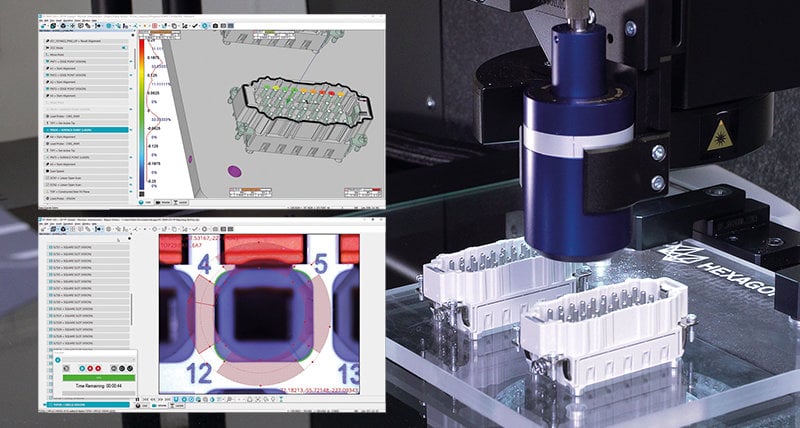
The current global chip shortage has brought on new pressure. Manufacturers involved in consumer electronics, 5G telecommunications, IoT Smart devices, Cloud Servers and automotive industries - to name a few - have had to deal with the challenges arising from the disruption of the global supply chain which left many high, dry and some, stranded.
In 2000, when the tech bubble burst, it left a ripple effect in the manufacturing sector. Equipment manufacturers had shifted to a leaner business model, holding very slim chip inventories while embracing a “just in time” approach to their materials.
However, the current crunch has renewed the pressure. Components, manufacturing equipment, computing support and materials had to be sought and spot bought, including electrical and electronic systems, to cater to speed, volumes and design variety required as demand for smart devices, electric mobility, cloud servers, phones and gadgets spiked. Work schedules had to be adapted to suit Covid restrictions placed by governments. Production had to be adjusted to suit new workplace safety regulations and requirements. Pivots needed to happen across the value chain. Fast.
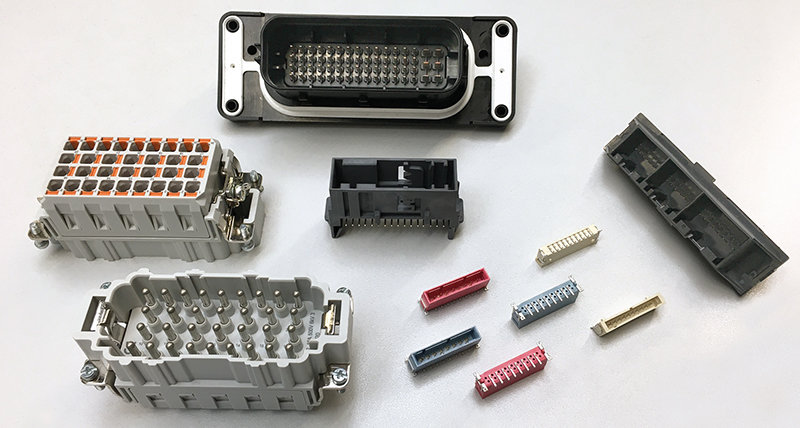
Here, complex technologies are often needed to ensure all design goals are met - efficiently and accurately, from start to finish, in order for products to be delivered with high quality and at optimum productivity.
And, as any good engineer will attest, enhancing application flexibility and reducing the number of iterations lead to improved productivity and accurate results with reduced cycle times.
Precise metrology and production data is, therefore, increasingly essential. More importantly, it needs to be shared in real time across the entire manufacturing workflow, from design and engineering, through to production, logistics and supply chains.
Flexible inspection capabilities and high measurement throughput
The challenges faced by many manufacturers today is how to enable metrology systems to collaborate and provide the rest of the business the quality information they need in real-time, without compromising security, accuracy, precision or performance.
While technologies for modularisation, miniaturisation and function extension open up opportunities for growth for connectors - a core component in all things electronics - in all areas of application, they also increase requirements for the measurement and inspection technology.
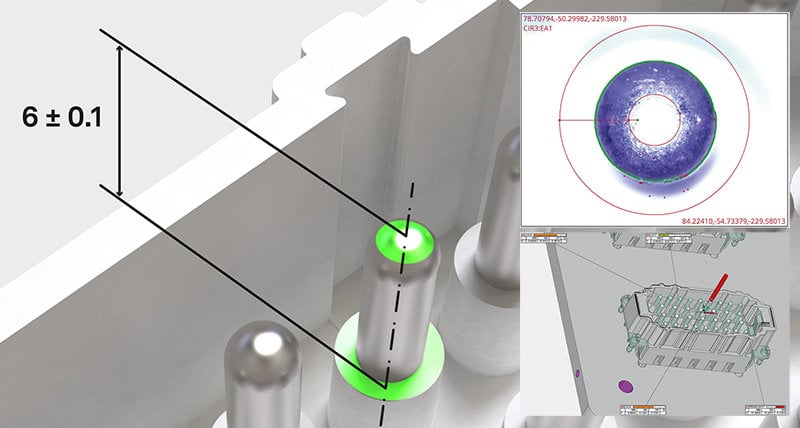
Multisensor measurement of the pin height: typical length tolerances are in the range of ± 0.1 mm.
Not only that, diverse connector types and housing variants need to be subject to variable dimensional inspection tasks at high measurement speeds.
Not performed correctly, these measurement processes may cause false rejections and unnecessary rework. Even worse, poor inspection or an acceptance of a bad part could lead to painful bottlenecks or defects which affect product safety and recalls, as mistakes, scraps and wastages chalk up already ballooning costs.
In short, “maximum technical performance at smallest size” best describes the requirements for the design, development and production of connectors. For quality control of the miniaturised assemblies, the measurement technology used therefore must offer both high resolution and accuracy.
Case Study - Hexagon OPTIV M: Dimensional accuracy of the contact elements
By incorporating multiple sensor technologies and advanced lighting systems into a single, high-precision measurement platform, multi-sensor coordinate measuring machines (CMMs) provide a universal solution for the capture and analysis of the entire spectrum of possible geometric errors of connectors.
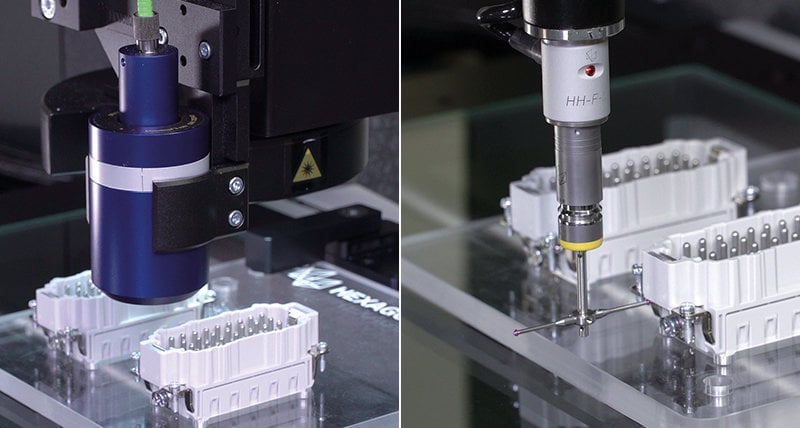
They are particularly suited for initial sample inspection of complex connector assemblies in fully automated measuring cycles.
Such CMMs reduce the need for using multiple devices in the inspection area, and eschew multiple setups and consolidate multiple measurement results, thus increasing the productivity by up to 30%, depending on the complexity of the components measured.
Dimensional accuracy of a connectors’ electrical contact elements, or its pins, is the crux of connector accuracy. In order to ensure this, a CMM measures the height of the pins (seating depth) related to a defined datum plane; in this case, the typical length tolerance is in the range of ± 0.1 mm.
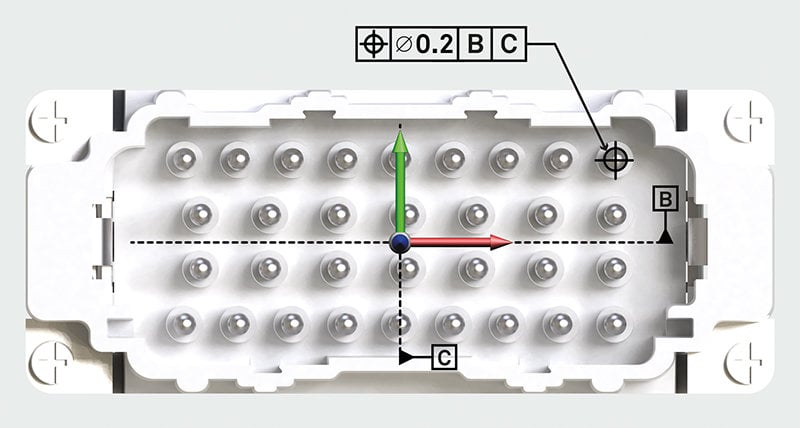
Measurement of the permissible positional deviation of the pin tips.
In the same measurement cycle, the vertical position of the pins is measured regardless of their shiny surface with the chromatic-confocal white light sensor. Due to the axial beam path of this non-contact distance sensor, there are no shading effects, so that even narrow and deep in the connector housing lying pin grids are reliably detected.
In addition, the permissible positional deviation of each pin tip from its ideal zero position in the X and Y directions is measured. The corresponding datum is made using a constructed intersection that is derived from measured reference edges on the connector housing.
The camera sensor’s variable lighting options also ensure highly accurate edge detection. All LED light sources - coaxial top light, telecentric backlight and multi-segment ring light - can be flexibly adapted to suit the texture and colour of various connectors.
Additionally, at measurement routine execution, the PC-DMIS function SensiLight checks whether an adjustment of the lighting is necessary and supports the user in selecting the correct lighting setting.
Functional inspection of the connector housing
For some connectors - especially in the automotive industry and the eMobility sector - resistance to environmental influences, dirt and humidity are important mechanical requirements. The flatness of contact and sealing surfaces must therefore be measured, and measured accurately.
In scanning mode, the chromatic white light sensor and multisensors enable the ambient light-independent capture of line profiles to be measured with a high measuring point density.
The metrology software PC-DMIS, for example, provides a range of CAD-based methods for contact and non-contact scanning. With the Perimeter Scan, the scanning path for the non-contact white light sensor is created directly on the imported CAD model of the connector.
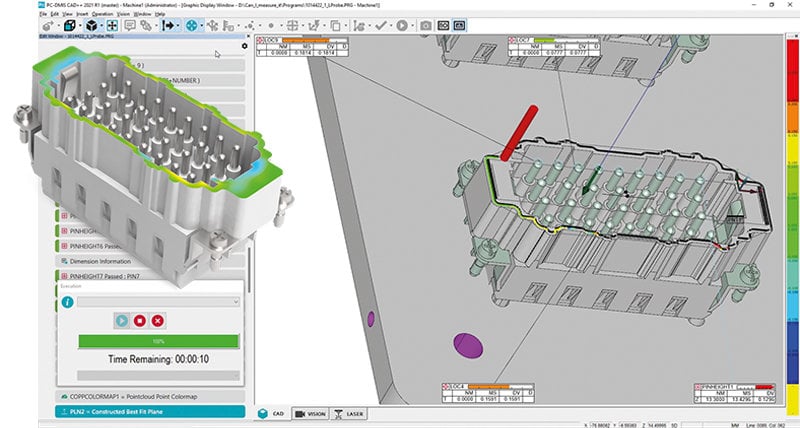
Measurement of the flatness of contact and sealing surfaces on the connector housing.
The scan then follows automatically along a defined offset of the nominal contour of the selected sealing surface. For a quick conformity assessment of the dimensional accuracy of critical contact and sealing surfaces, the measurement data can be analysed against the CAD model during the measurement routine execution and visualised as a colour-coded presentation of deviations.
The socket side of connectors also poses metrological challenges. In injection moulding or over-moulding processes, smallest cavities can be produced in very dense clusters.
Their inclination related to a defined reference plane is one of the important functional dimensions of connectors and must be measured. To solve this task, the multisensory coordinate measuring machine OPTIV M combines camera sensor and touch-trigger probe in one measuring cycle, and all measurements are carried out according to the drawing and without re-clamping the workpiece.
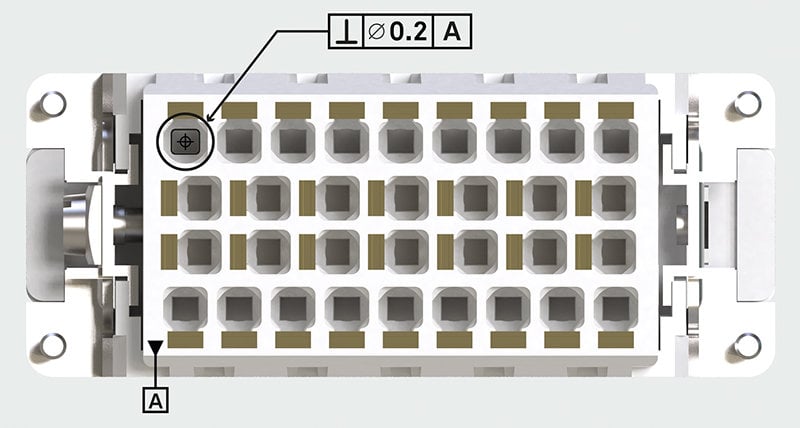
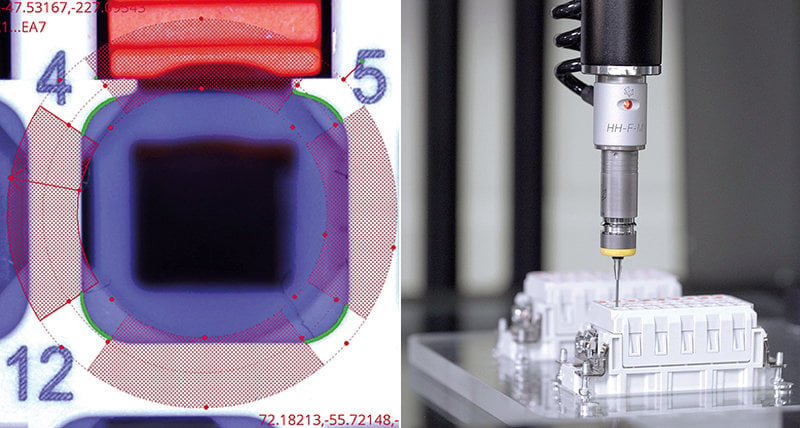
Multisensor measurement of the spatial orientation of the connector sockets.
With two independent axes for the optical and tactile sensors, OPTIV’s Dual Z technology provides the best accessibility to the inspection features with a minimised risk of collision. In addition, programming and measurement times are reduced to a minimum.
Real-time Data For Agility
The benefits to smart factory initiatives are clear to see. In fact, a Deloitte study found that smart factory initiatives have given companies 12% labour productivity gains in the past three years, and these gains could grow at a compound annual rate of 2.3% between 2025 to 2030.
To continue this trajectory of growth, consistent adoption of solutions that cut down manual work and offer users deeper insights is key.
Take for example manufacturers Soldar Ltd. Having secured a new business deal to produce components for a high-value OEM, it was clear over time that turnaround was too slow. The company saw a dip in on-time delivery. After investigating, they discover a significant bottleneck in the quality lab. The complexity of the new customer’s parts and the difficulty of alignment proved to be the stumbling block, which was time-consuming and prone to error.
Smart automation like Hexagon’s EYE-D, which uses a camera to automatically identify and align the part to launch the correct measurement routine, would help make alignment faster, eliminate error, and drive quicker product output.
What’s more, the ability to integrate this data into other software systems like Hexagon’s SFx Assets Management and Q-DAS software, could contribute to real-time equipment OEE, machine monitoring, availability, run-time alert, quality and data analysis. These smart functions could certainly support production teams in deriving subsequent improvements across their production and quality control processes, thus enabling manufacturers to drive smart manufacturing in areas that they might not have anticipated with thier initial investment.
A relatively simple technology upgrade like this can have a massive impact on KPIs, and the opportunities are there throughout the quality process
As well as supporting business objectives and a range of KPIs, these incremental technology upgrades also prime your quality processes for greater autonomy, another important step in the smarter manufacturing journey.
www.hexagonmi.com