Hexagon Solves Complex Issues for Specialist Packaging Solution Provider, With Productivity-Boosting CAD to CNC workflow
A company that specialises in producing bespoke complex, high-end mould tools for injection and stretch-blown plastic bottles is moving forward through 2021 with a highly automated workflow that integrates three design and CAM solutions from Hexagon’s Manufacturing Intelligence division with its preferred design software to increase efficiency by up to 40% and meet demanding lead times for customers.
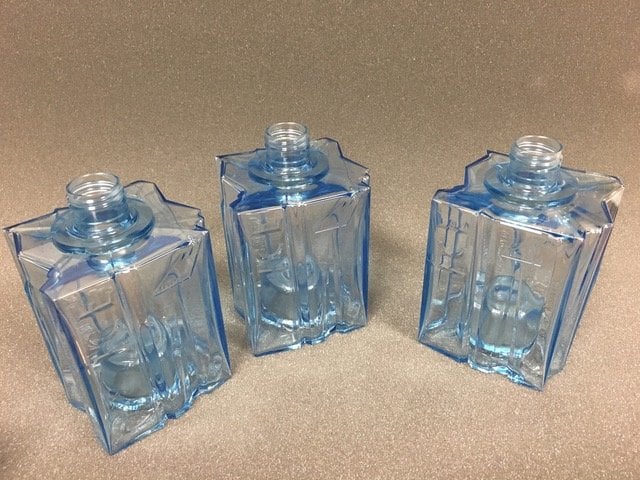
“While the COVID-19 pandemic made 2020 the worst year for the world, continuing to automate as much of our manufacturing process as we could allowed us to generate the manufacturing capacity to support record revenues,” says Andy Phillips, Manufacturing Manager for R&D Leverage.
R&D Leverage is the world’s largest independent solution provider to the single-stage Injection Stretch Blow Moulding (ISBM) packaging market sector, offering the global plastic convertors and consumer product brand owners what Andy Phillips calls a “complete solution” for a range of ISBM machines. Its tools are designed and manufactured using the highest quality materials. All tools are made in-house, on a vast array of the highest quality CNC machines: “The tools then go into our dedicated Product Solutions Laboratory (PSL) for testing, before we release them to customers.”
With the consumer market evolving, R&D Leverage’s high-end customers were requesting more complex geometries for end-users, incorporating significant undercuts, honeycombs and freeform surfaces. Those evolving requirements and the need to produce more complex 5-axis tooling in addition to their long-standing 2D milling and turning, meant they needed to invest in the latest technology to provide the necessary capability and cost reduction with confidence that its high quality standards would be maintained.
After a lengthy trawl through the marketplace to ensure they were investing in the best possible solution for their specific requirements, they now have a highly integrated workflow comprising DESIGNER, EDGECAM and WORKNC from Hexagon, and an automated pallet system feeding the machines so operators can be more productive.
That investment needed to address four critical challenges:
- Improving turning cycle times
- The need to produce rapid-prototype 3D moulds and execute 5-axis programs with a high level of automation to respond quickly to customers
- Automating the repeated 2D milling of back plate variations
- Editing models to prepare them for manufacture.
They had already been using EDGECAM to program their machine tools for 2D milling and turning for eight years, and Andy Phillips says when they were looking to upgrade their software to program complex 3D geometries, they quickly saw WORKNC’s potential.
As Hexagon’s CAM solution for complex models in the mould, die and tooling industries for 2- to 5-axis CNC programming, the software was ideal for these specific needs. “Many of the bottles for which we produce moulds are extremely complicated. Some have engravings all the way down the sides, and the honey bottles have a lot of honeycombs in the form.
“With our old software, all angles and anything complex, had to be programmed manually, and there was no 5-axis capability. This meant we had to carry out a number of twists on the machine, which gave scope for error.” This was not acceptable for R&D Leverage.
R&D Leverage’s CNC Milling Programmer, Robert Dods, takes up the story: “When we create our toolpaths now, we can do the whole program in one action with WORKNC. Then I check everything out to ensure there are no collisions, or any holder collisions, and that the machine is capable of performing all of the manoeuvres that we’re asking of it.” “This means that when we send the program to the shop floor, the operators can run it with full confidence, knowing it’s going to be 100% accurate.”
The Hexagon team also gave the company additional peace of mind by building a virtual replica of the machine and its internal kinematics inside WORKNC, so the outputted programme can be fully visualised in a digital environment. “We didn’t have anything like that with our previous software,” says Andy Phillips. “We were simply relying on the programmer’s knowledge and experience. But now, with this extra failsafe in WORKNC, we can check there are no collisions in the program before we start machining.”
To enable greater automation, he says their digital workflow begins with importing PTC Creo design files that conform to the templates from their American owners, and R&D Leverage standards, so that the digital workflow can progress seamlessly through the entire manufacturing workflow to cutting metal on the machines.
This includes the automation tools to utilise 2D information and vastly reduce programming time in EDGECAM and WORKNC. Occasionally, there is the requirement with their 3D work to modify a model for manufacture, such as capping holes and removing faces.
This is carried out in Hexagon’s specialist CAD-for-CAM product, Designer, which provides one agnostic platform to exchange files with both EDGECAM and WORKNC without any translation or data loss, ensuring the data is accurate and the program is right the first time.
In a nutshell, the workflow begins with designing the preform around the original 2D drawing. This has to be completely accurate as this is later “blown” to create the bottle. The tooling is designed around that in PTC Creo, and the data is exported to the CNC programming team. The .prt files are then run through EDGECAM for plateline work utilising a complex and customised algorithmic ruleset in EDGECAM Strategy Manager, defined by R & D Leverage, to ensure the right tooling and cutting strategies are utilised depending on the 2D featuring, improving standardisation, reducing programming time and improving quality.
For any complex 3D moulds, the .prt is pulled into Designer for model preparation before one-click integration into WORKNC, where the expert programming team undertake complex 5-axis work, utilising their pre-determined templates. These templates sit within WORKNC and use previously approved and proven strategies and tooling, that are dynamically adapted to the new subject model. Finished programmes are then output in either Heidenhain or Fanuc NC code through proven post processors, depending on which machine will be carrying out the subtractive manufacturing.
The team have also built an accurate tool library inside both WORKNC and EDGECAM, detailing a variety of information including feeds, speeds and depth of cut. And everything is fully collision-checked with the cutter holder, shank, machine table, column, and the fixture. This complements the approved templates (or strategies) which govern part of their automation process. Robert Dods explains: “When we need to make a specific plate we bring in the strategy for it, and it fully automates feeds, speeds and tooling.”
As well as the technical capabilities of the products, the key factor in R&D Leverage’s successful deployment has been the human factor, as Andy Phillips explains: “With our changing requirements in recent years, we once again surveyed our options to understand the best provider. The real differentiator for Hexagon has been the expertise and commitment of the people.
“Given the complexity of the project and the internal pressure to make it succeed, ensuring it was managed correctly was a huge factor for us. Phil Smith, Hexagon’s Enterprise Application Engineer, set out a clear project plan with sensible but challenging milestones, and has worked tirelessly to deliver on those objectives. The software makes our lives easier now, but this was only because of Phil’s hard work in understanding our exact needs and providing a true turn-key solution.”
Matt Martin, Hexagon’s Enterprise Sales Manager, suggested the human factor was a two-way deal: “The project was only successful because Andy and his team were so open with us. They were open about their challenges and where they wanted to get to and we plotted a course together.”
The inter-operability between all components of their integrated Hexagon workflow gives R&D Leverage the ability to guarantee a quick turnaround of mould tools that are 100 per cent accurate for their packaging customers. One component in particular that was commonly used within all of their mould tool assemblies really challenged the turning capabilities of their previous software, but bringing EDGECAM’s innovative Waveform Turning capabilities into the equation now offers game-changing efficiency gains.
Andy Phillips concludes: “This complex component has seen a 40% reduction in run time per unit. We machine around 2,500 of those per year – so it’s a massive time saving. In order to continue providing a better solution than our competitors, we needed to continue our investment in new state-of-the art technology. Our overall fully integrated, automated solution from Hexagon is absolutely vital in ensuring R&D Leverage is always one step ahead in offering our customers the highest quality solution with 100% reliability on lead times.”
www.hexagon.com