www.ptreview.co.uk
17
'21
Written on Modified on
Akasol News
AUTOMATED BATTERY RECYCLING PROCESS
AKASOL PARTNERS WITH FRAUNHOFER RESEARCH INSTITUTION is partnering with the Fraunhofer Research Institution for Materials Recycling and Resource Strategies IWKS on a new funding project: As part of their joint project, “Bætter Recycle – Battery recycling and disassembly for eMobility and optimization through recycling-friendly design,” the two partners are working to develop automated recycling processes for the eMobility industry.
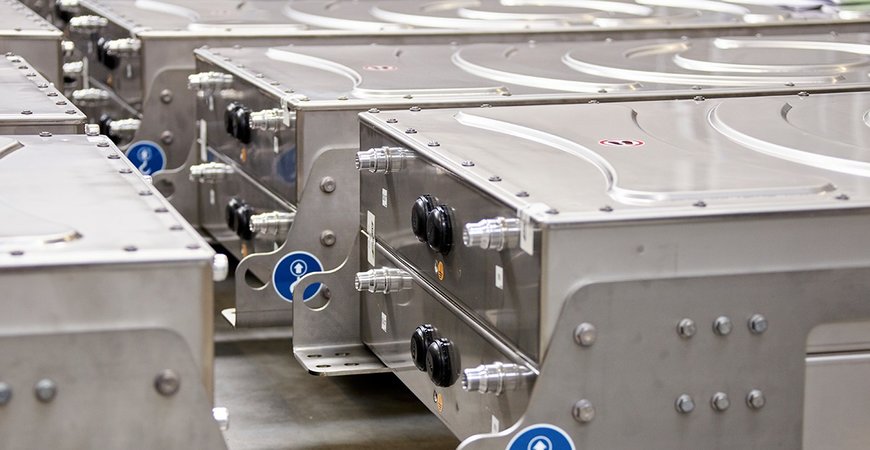
According to plans by the German federal government, around ten million electric vehicles and 500,000 electric commercial vehicles are to be sold in Germany by 2030. A third of the buses used in public transportation will also be fitted with electric drives during the same period. “The rising demand for high-performance battery systems for electrification the various areas of mobility automatically means that more raw materials, such as lithium, cobalt or nickel, are needed to manufacture these energy-storage technologies,” explains Dr. Björn Eberleh, who, as head of Product Management at AKASOL, is in charge of the project.
In order to cover the increased demand for raw materials, it is necessary to promote their recovery from used batteries and to gradually increase the recovery rates. An important step is to align product design around considerations of recyclability at the end of the service life. “I am pleased that we have found a strong and competent partner in the Fraunhofer IWKS research institution, with whom we can work together to develop solutions for the efficient recovery of valuable materials from the product life cycle.”
As part of the “Bætter Recycle” funding project, the research partners want to develop an automated recycling process for the efficient disassembly of traction batteries and the recovery of raw materials. “The goal is to implement a process that checks a battery system to determine its condition and then uses relevant parameters to decide whether it can be used in a “second-life” application, or whether it needs to be fed directly to recycling,” Eberleh explains. In this context, the entire product life cycle of lithium-ion batteries, from design to recyclability, is to be analyzed and evaluated in two stages.
The first stage considers recyclability at the initial design of the product. This stage identifies any problematic steps in disassembly that might be optimized in the design of future battery systems. In the further course of the project, the materials used will also be tested for their recyclability in order to avoid materials that are difficult to recycle in future developments.
Another aspect considered within the funding project is the actual reusability of the various modules for practical applications in a “second life.” “In concrete terms, we are studying the extent to which modules recovered from battery systems can be repurposed with the aid of a modular system – to create stationary battery storage, for example.”, explains Eberleh. This not only extends service life but also increases the cost-effectiveness of the AKASOL modules. Parallel to developing the disassembly and recycling process, the new processes are assessed under a range of parameters – such as environmental impact, material criticality or cost – in an effort to evaluate overall process sustainability and identify the factors that leverage this. “We want to improve the ecological balance of the lithium-ion batteries and contribute to the reduction of CO2 in production.” New development guidelines are being drawn up for this purpose and in the future will permit mapping and planning of sustainable materials and processes, even at the design stage. The Darmstadt, Germany based manufacturer is thus playing a real pioneering role in the market for the recycling and reuse of lithium-ion batteries in the commercial vehicle sector.
The topic of climate protection has top priority in the individual production steps: “The eMobility industry is obliged to think about sustainability in holistic ways. At AKASOL, this means keeping our own ecological footprint as small as possible while prioritizing environmentally conscious handling – from the development through to the disposal of battery systems. Our promise is to develop products in a climate-friendly manner, to avoid waste and to ensure professional disposal and recycling.” The findings from the funding project will be applied as transferable benchmark concepts for product lifecycles of all types – regardless of a battery system’s size, type or application.
The initiative for the promotion of innovations at Hessen Agentur GmbH is providing around EUR 775,000 in funding for the project; in this regard, AKASOL acts as an industry partner to the Fraunhofer Research Institution for Materials Recycling and Resource Strategies IWKS. With headquarters in Alzenau in Bavaria and Hanau in Hesse, one area of research focus at Fraunhofer IWKS is the extent to which recyclable materials can be efficiently recovered from a product life cycle.
www.akasol.com