www.ptreview.co.uk
19
'21
Written on Modified on
CONNECTED FACTORY : HOW IS ACTIA ENGAGING IN THE DYNAMIC OF THE 4TH INDUSTRIAL REVOLUTION
“The challenge of connected factory is creating this hyper connectivity and handling the data that comes with it, by connecting all the links of the production chain, as well as the customers and all stakeholders who will encounter the product. From the RFQ phases up to the product’s life-cycle in its application with the final customer, connectivity has now been a reality for some years.” Éric Le Bozec, ACTIA Group Industrial Director, describes the performance drivers for ACTIA’s factory 4.0.

Industry 4.0 refers to the digital transformation of factories. Just like other electronics manufacturers, ACTIA is leading its fourth industrial revolution. In recent years, the group has been rapidly accelerating in this field. Incorporating the digital ecosystem within a production factory entails numerous major changes within the organisation, both in terms of jobs, and product and service offerings. This is a real revolution within the group’s eight production units worldwide.
WHAT ARE THE CHALLENGES OF THE CONNECTED FACTORY FOR ACTIA?
Industrial excellence to enhance competitiveness
“Within a hugely competitive environment such as ours, the main issue is time! Saving time: production time, manufacturing time, time to market, feedback loops for taking action more quickly, more efficiently and to reduce, or even eliminate waste.” Explains Éric Le Bozec
Industrial business has become a “connected factory”, providing obvious gains, among which we can mention:
– greater flexibility for responding to variations in customer requests;
– continuous adaptability to the diversity of markets and products;
– more extensive traceability, in order to respond more quickly in the event of malfunction;
– increased responsiveness;
– production cycle optimisation;
– providing information to our customers in real time.
Digitalisation is in place at every level of the industrialisation chain, creating a truly connected factory.
The second major concern of this digitalisation is securing data. The challenge is to secure the management of customer data while reducing the costs of managing this data.
Positively building support
“Digitising our means of production affects more employees than any other process within the company. This is why it is essential to build progressive support for the initiative by sequencing the stages and selecting technological building blocks.
I am in favour of a deployment strategy where each small step achieved falls within an ROI initiative that is short and has quick success, in order to positively build this necessary support. I am not a fan of the Big Bang approach.” Explains Éric Le Bozec
At ACTIA, people are really a key factor in the connected factory. A large number of technological building blocks are produced in house. The ACTIA teams are made up of experts who are highly experienced in the methods and tools. They have an excellent knowledge of the environment, the needs and future requests of customers, despite the disparate nature of our markets. The teams are driven by a constant desire for improvement and learning, which is a real source of added value towards the efficiency of our connected factories.
This applies to the production teams. ACTIA is set on developing the skills of personnel who work with robots as well as with a high degree of automation. This degree of automation also varies according to customer requirements. With the arrival of increased automation within the factories, operators are assigned to tasks with high added value. The connected factory transforms roles and behaviours. ACTIA assists its employees in this change.
The synergy of 8 global industrial sites
The ACTIA group has eight factories or electronics or electrification units across three continents:
– ACTIA Colomiers, France;
– ACTIA Chartres, France;
– ACTIA Tunisia, Tunis;
– CIPI ACTIA Tunis;
– ACTIA Electronics in Romulus, Michigan, USA;
– ACTIA Nordic in Linkoping, Sweden;
– ACTIA I+ME in Salzgitter, Germany;
– ACTIA Corp in Elkhart, Indiana, USA.
The initiative for digitalising factories therefore brings together the skills and energies of these eight different backgrounds. We rely on a team of ACTIA experts to model the production means on an international scale. This group synergy enables us to pool tools and developments, as well as decentralise the industrial steering of units. It also allows support requirements to be continuously met according to production events.
Therefore, each unit makes a contribution.
For example, the new generation of generic test platform developed in France will be deployed in the group’s factories. The POC (Proof of Concept), connected glasses, developed in Tunisia and the USA, along with digitalising of production routines will also soon be deployed on the production sites.
Cybersecurity as part of a global approach
One of the major challenges of this industry of the future is to improve industrial performance through digitalising production means and better use of data and interfaces, while ensuring optimal security for the whole chain.
Increased data exchange and interfaces, both in terms of our ecosystem and external environments (customers, suppliers), have resulted in a significant increase in exposure to threats.
In addition to the “technical” security aspects of our production environment, responding to these challenges requires addressing cybersecurity more broadly, with respect to our business processes and all human and supply chain resources.
In order to address this, ACTIA has implemented a global cybersecurity management initiative, which is not limited to the factory environment, but extends to the whole perimeter and all interfaces.
“Since 2018, ACTIA has held certification for its Information Security Management System (ISMS) in accordance with the ISO 27001 standard.
Additionally, this global approach integrates that application of benchmarks that are more specific to the industrial context, such as the Industrial CyberSecurity Guide by ANSSI [French National Cyber Security Agency] for example, or Automotive cybersecurity engineering standards such as ISO/SAE 21434, and is gradually being rolled out to all factories.” Eric Le Bozec
Advancement of collaborative platforms
Digitalising collaboration between departments and connected factories
“Over the last few years, our efforts have been focused simultaneously on infrastructure, production means, machines of course, as well as developing our collaborative platforms.
The first benefit of collaborative platforms is breaking down the barriers to interactions between departments and stakeholders, and developing cooperation and joint construction within the company. This approach gives rise to ideas and initiatives regarding the Industrialisation Department. Within the ACTIA group, each factory develops initiatives or even creates POCs (Proofs of Concept) to benefit the group’s other factories.” Emphasises Éric Le Bozec
The other concern is the risk of KPI proliferation. Digitalising processes and procedures generates more data and increases its availability. The more data that is produced, the more indicators there are. Each department has its KPIs according to its priorities. It is crucial to know how to process, classify and index this data.
For example, ERP becomes the database that guides everything in terms of the logistics chain. It is connected to the PLM which holds all of its product data and configuration, the MES hosts all the real-time production data.
The MES (Manufacturing Execution System) software is the driving force of the connected factory
To address the challenges of the connected factory, the MES must create a link between:
– humans,
– production machines,
– company’s information system,
– various monitoring and data management tools
– and customers, of course.
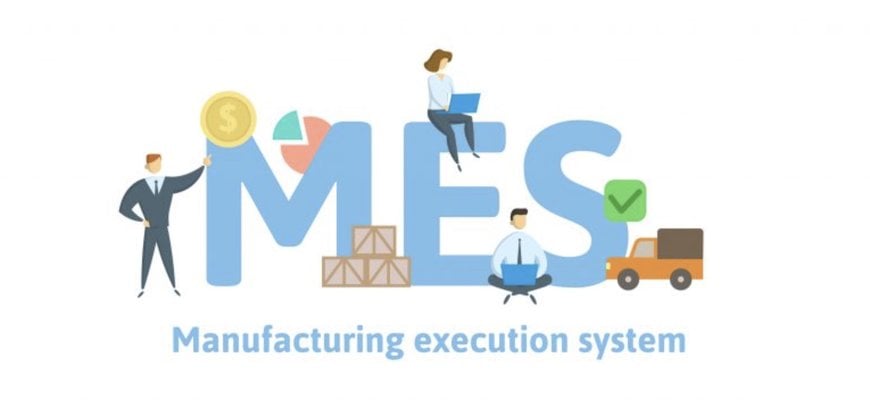
This link is provided by various IT solutions that process production data, documentation, quality, etc. This is the MES. The key issue is managing industrial processes by collecting real-time production data from a workshop or factory.
This data is then used for multiple purposes:
– traceability,
– quality control,
– production monitoring,
– scheduling,
– maintenance, etc.
Supporting an ERP, a workshop MES solution makes it possible to:
– increase the reliability of customer delivery times and meet deadlines;
– manage the production tool accurately;
– improve human and machine productivity;
– reduce stocks (in-process, supplied materials and finished products) and production cycle times;
– enhance visibility and accuracy across the whole supply chain: logistics, production, purchasing, procurements, sales.
The new NPI
“Following PLM deployment and six months ahead of our ERP migration connected to the PLM, we are deploying an NPI tool which is a major brick of the MES (Manufacturing Execution System). This deployment is taking place gradually over the group’s eight production sites. We have taken advantage of the Covid-19 crisis to develop our NPI deployment plan, which was selected in January 2020, and train our specialists.” Says Éric Le Bozec.
This tool will help us to digitalise entry into production for new products and to anticipate automatic preparation for some production machine programmes.
Digitalising factories, like factory 4.0 or cobotics, are not new issues. Accelerating the initiative within the ACTIA group gives structure to both the architecture and the method in order to better position it at the core of the key objectives: customer satisfaction and industrial competitiveness. This significantly shortens the production cycle. All the technologies deployed help to optimise production as close as possible to needs and to anticipate constraints. The same applies for digitalising customer relations.
“Digitalising the production chain is at the heart of the interface between ACTIA and its customers. This is an excellent way of improving operational efficiency. These technologies provide new commercial opportunities in the near future, just as it creates work spaces and freedom to take initiative, which are of interest and important for industrial teams.” Concludes Éric Le Bozec
www.actia.com