NANOLIKE DIGITIZES SILO FILL LEVEL MONITORING WITH OPTIMUM EFFICIENCY
Nanolike is pleased to introduce a new digitized fill level monitoring solution for food and beverage silos.
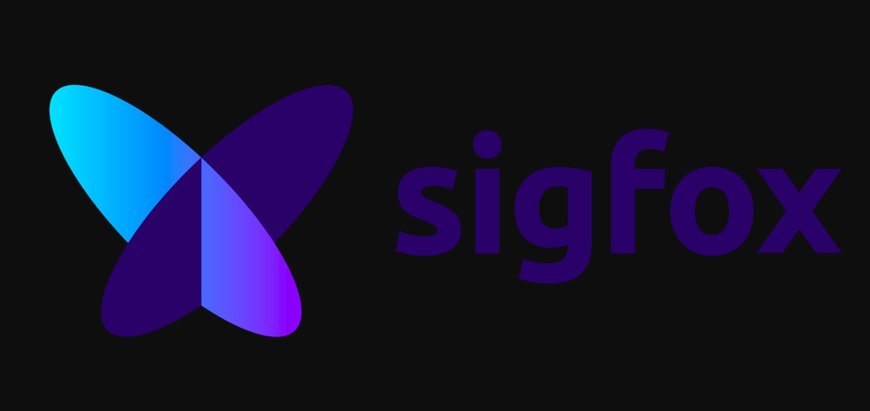
- Nanolike uses the 0G network to connect silo fill level monitoring to the cloud
- Real-time transparency facilitates silo fill level management
- Helps food and beverage manufacturers to optimize their supply chains
The goal is to simplify inventory and order management processes in the food and beverage industry. Another aim is to help the manufacturers and suppliers of raw materials and additives optimize their silo replenishment processes. This not only saves costs but also reduces the environmental impact by enabling route optimization.
The new digitized silo fill level monitoring solution stands out through highly efficient sensor and cloud connectivity technology using the Sigfox 0G wireless network. It requires zero maintenance for years and needs neither an external power supply nor a data line, which saves costs and ensures that the digitization investment is amortized very quickly. This makes Nanolike technology highly disruptive, as it can replace any alternative sensor technology used exclusively to manage replenishment management.
Users of Nanolike‘s digitized silo fill level monitoring solution are found in almost all sub-sectors of the food industry, from soft drink and fruit juice producers, dairy product manufacturers, breweries and coffee roasters, to legume processors and industrial bakeries as well as jam, instant and convenience food manufacturers – and that‘s by no means an exhaustive list. Nanolike’s digitized silo fill level monitoring solution isn’t just for large silo operators; it also targets silo manufacturers who aspire to include this technology in their portfolios and, above all, raw materials and additives manufacturers aiming to offer their customers automatic replenishment, vendor-managed inventory (VMI) or similar solutions as part of their digitization strategies.
Quickly and easily mounted on the exterior base of the silo, the Nanolike sensors give users 24/7 access to information on fill levels and demand forecasts in real-time. This digital solution makes it much easier to monitor the silo fill levels and greatly reduces users’ workload, as they no longer have to climb to the top of silos at different locations to check the fill levels. Instead, all required inventory management tasks can be done in less time from the safety of the office. An integrated early warning system alerts the silo operator to potential bottlenecks, helping to prevent any shortages of raw materials and additives.
Based on real-time data, the mobile application also facilitates the automation of purchase processes as silo operators can chose to place orders directly from their smartphones. Such an integrated solution, which can be implemented with just a few clicks, greatly simplifies communication between food manufacturers and their suppliers. What is more, it makes it possible to optimize the supply to distributed silos at a higher level, leading to overall savings in transport logistics, which ultimately also improves the long term CO2 balance. The data from the Nanolike sensors are consolidated in a central cloud from where they can be imported into existing software systems and customer clouds, or retrieved via smartphone app at any time.
The digitized fill level monitoring solution from Nanolike is extremely simple to implement, as it is self-calibrating, does not require active calibration, and also filters out undesirable environmental influences. Before filling a silo, the user sets the sensor to zero via the mobile phone app and manually enters the fill load once in the software. From thereon, the changing fill level is calculated in the cloud, based on a comparison of sensor data recorded before and after filling. The measurement corridor can include just the one load, which doesn’t have to be a full load, or it can map the state between a completely empty and completely full silo.
Upon special request, it is also possible to manipulate the Nanololike measurement corridor manually in the cloud, for example, to be able to extrapolate fill levels of a half-full silo, which is 2/3 full after replenishment, over the entire fill level scale from 0 to 100%. The solution is also extremely scalable and can be extended from a simple cloud app for a batch size of 1 to fleets with thousands of silos. For the latter, Nanolike also offers a convenient data interface for the connection of external IT solutions.
The digitized fill level monitoring solution from Nanolike is available for order now from batch size 1. Larger-scale silo operators and their suppliers may request a free demo installation. Suppliers of silo technology are also invited to get in touch to evaluate the potential for developing collaborative solutions to digitize their fill level sensor technology.
www.sigfox.com