www.ptreview.co.uk
07
'20
Written on Modified on
What will the SME manufacturing landscape look like post COVID-19?
Chris Evans – Marketing and Operations Group Manager at Mitsubishi Electric UK looks at the effect the pandemic could have on the future adoption of automation in manufacturing within SMEs.
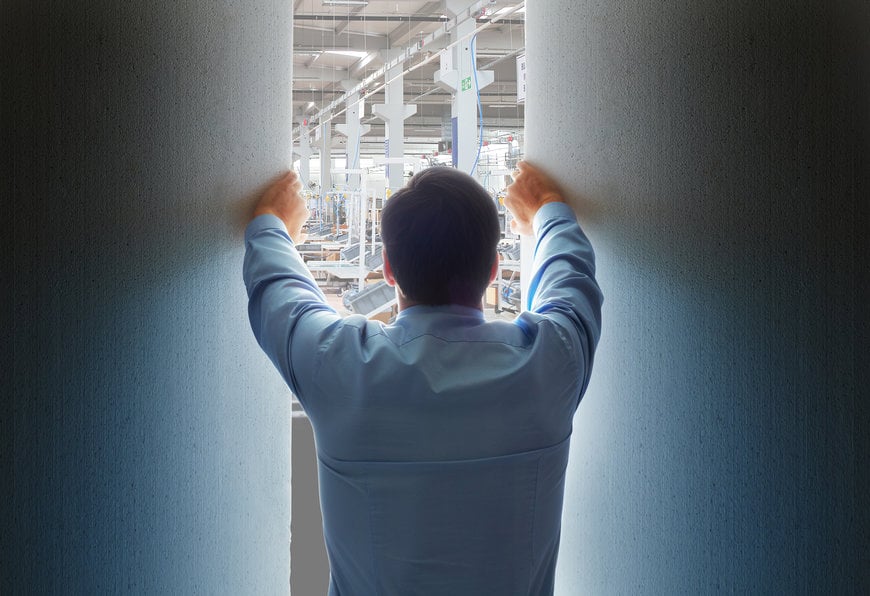
A catalyst for digital transformation
It is poignant to recall that at the time the world went into meltdown, industry in general was still riding the Industry 4.0 wave and looking forward to following a collective journey towards digitalisation and smart manufacturing. The global pandemic certainly put the brakes on that but what will happen when we emerge on the other side of this crisis?
What this experience has shown us and is continuing to show us, is that businesses who had already adopted automation, or by their very nature are digital operations, such as the online retailers, have adapted more quickly and in some cases have enjoyed a boom time. In contrast, many traditional manufacturing companies are struggling to return to anything like pre COVID-19 production levels because of many factors, not least of which is the requirement to observe social distancing requirements for staff on their production lines and associated processes.
Could it be then, that rather than be its nemesis, COVID-19 may well prove the catalyst that stimulates and drives manufacturing to forge ahead with digital transformation post pandemic?
Digitalisation for all
Perhaps in the past, talk of smart manufacturing and the digitalisation of the manufacturing process could have been interpreted by some as only applying to the larger manufacturers and enterprises. To accept that argument would be to deny SMEs the chance to enjoy the benefits of adopting automation and a level of ‘smart’ that is appropriate for their business.
It is important to consider the manufacturing process as a whole and analyse areas where the adoption of automation would have the greatest impact. Labour intensive areas have always been a target for automation and with the availability of today’s technologies, the options are wide and scalable. As an example, the adoption of robotic solutions in assembly, product sorting or machine tending processes offer many advantages over the manual alternative.
Robot solutions now include the option of collaborative operation should the robot have to interact directly with the operator. Depending on the application, a co-operative solution where the operator is allowed to enter into the robot’s working area safely, which either slows down or halts the robot operation until safe to resume, could well be the best solution
A wise investment
For an SME to invest in automation, there needs to be a relatively short ROI, which is even more relevant in these times of living with a pandemic when every investment comes under the greatest scrutiny. This can only be realised by considering what the SME is trying to achieve. Once that clear vision is established a scheduled plan can be developed, focussing initially on quick wins.
Every manufacturing operation has pinch points or bottle necks and often these offer those quick win opportunities, where a reasonable level of investment can return significant benefits.
This approach has two major benefits; an immediate effect on the efficiency of the manufacturing process and additionally, it helps to convince the people holding budgets that investing in automation is the right thing to do.
Applying automation solutions can be achieved with a staged approach as long as the end goal is understood by all parties. The scale of the implementation can also be matched to the size of the enterprise and available budget.
Changing data into information
Of course, to really make the operation ‘smart’ you must collect, collate, aggregate and analyse the information about the process from what is actually going on in the manufacturing plant.
This feels like another giant leap for many SMEs but again with the right approach this can be targeted and scaled to suit varying business requirements. Automation technology today has a host of built in diagnostic and predictive maintenance functions, all waiting to be collected and analysed.
What is done with that data can be as simple as visualising it on a local operator panel with associated alarms, to passing it through a data collection layer and linking it to business systems at the top of the enterprise and all points in between.
With the advent of intelligent process controllers and edge computing technology, it is possible to perform detailed analysis and even apply Artificial Intelligence (AI) at the Operational Technology (OT) layer to minimise the data traffic that is sent to the Information Technology (IT) end of the business. Edge technology also provides the ability to react in real time to process anomalies and changes at plant level.
The benefits of following this path are clear, facilitated by the evolving asset care regimes of preventative, predictive through to prescriptive maintenance, operational efficiencies can be improved, production throughput can be increased and downtime reduced.
Facing the challenges ahead
Now more than ever, manufacturers need to embrace the digitalisation process, which is challenging when many organisations have operated in ‘survival mode’ through this crisis with a subsequent lack of money for investment. Therefore the scale of any short term investment in the manufacturing process may be reduced, which makes it even more important to discuss and plan an achievable result, balancing what is available to invest against the best return on that investment. A well thought through implementation plan will illustrate that following a staged approach provides an entry level that can be achieved with the minimum of investment and provide tangible results.
It has been proven that an automated plant that relies less on manual labour in the manufacturing process is more resilient to this type of crisis than a labour intensive one. An automated plant also allows the manual labour to be deployed elsewhere in the organisation on less mundane tasks and provides opportunities to upskill the workforce.
Future proofing the operation
Moving forward, all businesses, whether SMEs or larger organisations will benefit from adopting or further adopting automation and smart manufacturing. This journey can start with small steps and evolve over time against an agreed plan but it is extremely likely that manufacturers who run smart operations and who make themselves more resilient will prosper as we work our way out of this pandemic.
At Mitsubishi Electric UK we have found that early engagement with the manufacturer is vital to fully understand their goals, business requirements and potential obstacles and then to develop a staged plan to map out the road to what smart manufacturing looks like for them.
It is also important to consider all the elements necessary to deliver a complete solution, including cyber security. We are fortunate at Mitsubishi Electric that in addition to our own automation solutions we have complimentary technologies from our e-F@ctory Alliance Partners which collectively can meet all of these requirements.
It would be easy just to relate everything to surviving the pandemic but it should also be viewed as a catalyst to implement change. Manufacturers who follow the journey towards digitalisation and smart manufacturing, scaled to suit their enterprise, will create a more agile and flexible manufacturing environment which will be ready to react to changing customer wishes and demands and will fundamentally enable them to stay ahead of their competitors.
www.gb3a.mitsubishielectric.com