www.ptreview.co.uk
07
'20
Written on Modified on
CANNY ROBOT DECISION BRINGS COST SAVINGS
A new Kawasaki robot has been installed to assist Ball Beverage Packaging improve its efficiency and save money. The machine replaced a near 20-year-old Kawasaki ZD130S robot at the Wakefield plant, bringing greater speed, precision and durability to the customer.
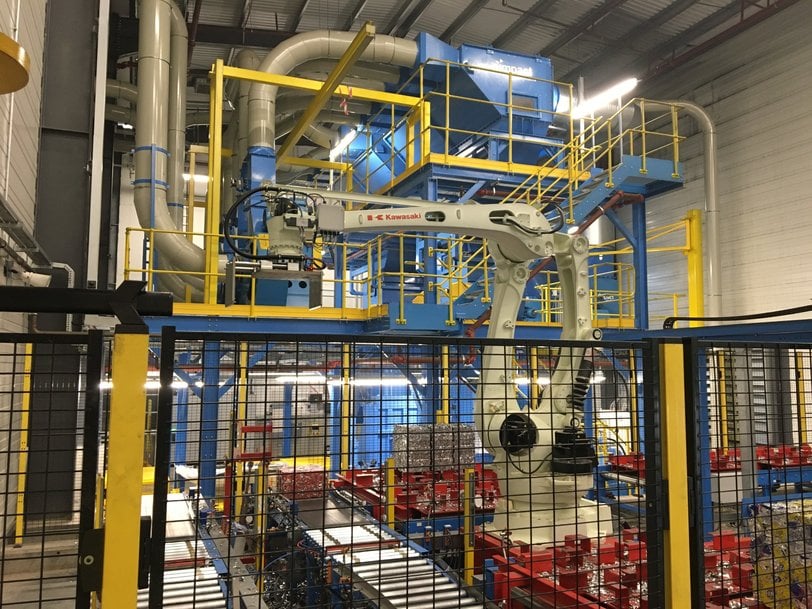
When Ball Packaging needed a new, fully automated waste material conveying and bale handling solution due to increased production capacity, they turned to air technology and waste separation experts Impact Air Systems for a solution. Impact Air Systems, established in 1989, specialises in providing bespoke solutions for the handling and processing of all manner of industrial waste products including metals, allowing manufacturers to maximise recycling opportunities, reduce costs and help look after the environment.
Impact Air System’s scrap handling system collects waste material from the beverage can production machinery and conveys it through a pneumatic ductwork circuit to a hydraulic bale press. Once pressed, the bales of waste material are loaded onto transportation and taken to an appointed recycling location.
Ball Packaging is a global leader in beverage packaging with extensive experience using Kawasaki robots already, and their brief to Impact was to design a new system that would allow them to increase production capacity, replace older equipment, reduce costs and maximise recycling capability.
Kawasaki Robotics recommended its automation systems integrator LAC Conveyors to work with the Impact Air Systems engineering team, and together they designed a new system that offered significant savings over the methods that were currently in use at Wakefield. They started by understanding Ball Packaging’s key operational requirements, designing flexibility and reliability into the system.
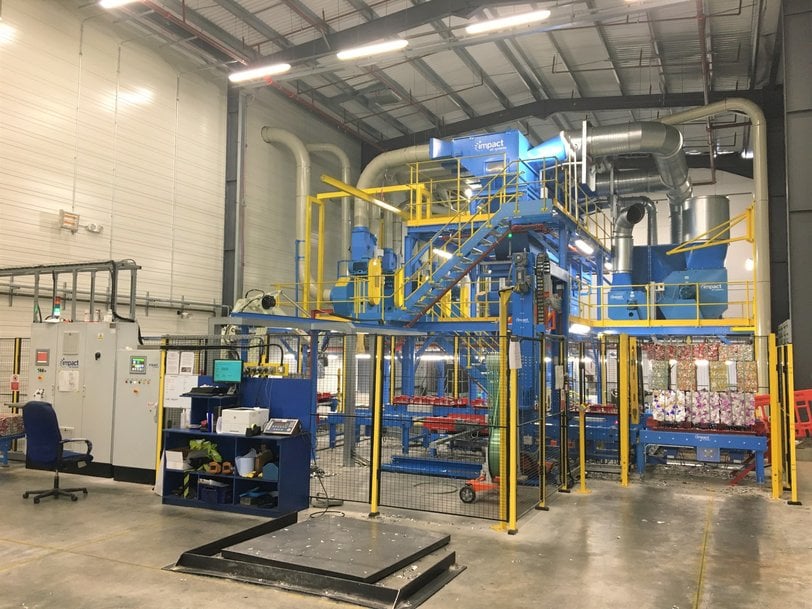
New system was installed at Wakefield to improve efficiency and save money
One aspect of the new design focused on the logistics aspects that take place with the finished aluminium bales after they leave the Wakefield site for recycling. Part of this process involved consideration about the bale stacking process, maximising the road vehicle payloads and also the offloading exercise that needed to take place once the bales reached the recycling centre.
Previously, the bales of scrap material had been stacked by the robot on to wooden pallets, strapped to the pallet by hand, transported from site like most other waste material, then removed from the wooden pallet prior to recycling. Detailed investigation revealed that this process did not provide the best payload economics for transportation and neither did it take any account of how the recycling plant could most efficiently handle the bales on arrival. As a result of reviewing this part of the process, Impact Air Systems created a new bale stacking pattern that maximised the robot capability enabling bales to be stacked in a pattern that eliminated the use of wooden pallets.
They achieved this by developing a new custom-made transport pallet, mindful of the fact that the stack needed to be within the tolerances described for baling and also the need to try and prevent the shedding of any debris from the bales during both handling and transit.
By employing a robot to stack the bales in a pre-approved pattern that contained voids allowing them to be handled by a fork truck, they could be moved, stacked and then loaded directly onto a road vehicle in a manner that facilitated swift and easy removal once the recycling centre had been reached, eliminating the use of wooden pallets. Extensive trialling proved the idea and as a result, the customer is now saving time and expense on a scale not previously achievable.
Kawasaki Robotics’ Ian Hensman, who sold the original robot to Ball Packaging almost 20 years ago, observed: “It was clear from the start of our discussion with Impact Air Systems and LAC that a combination of robot payload, speed and durability was being taken as a given, based on Ball Packaging’s previous 20 years of fault-free service from our ZD130S robot. What they needed to be certain of was that the new robot we recommended could cope with new demands brought by rapid growth, lifting anything up to 320 bales on each shift, with each bale weighing around 30kg. For the new system, the scrap brightwork bales, typically sized 440x440x280mm, had to be rotated to the required position for stacking whilst in the transit arc, and needed to be placed into the appropriate stacking position with a precision guaranteed to be within 1mm first time, every time. Further, to cope with increased production levels (and also make provision for further future growth), an extremely fast full-cycle time was specified for each individual movement. This also provided an assurance that the new system could absorb peaks in the event of potential spikes occurring in can making production, such as those seen as a result of lockdown”. Kawasaki’s engineers recommended the company’s CP180L robot for the application. It is approved and certified to carry a payload of up to 180kg at its maximum reach of 3255mm, and at this reach the unit operates with a guaranteed positional accuracy of +/- 0.5mm.
Impact Air Systems’ Dave Lansdell oversaw the project “We identified early on that greater speed and precision were clear requirements as far as the robot element was concerned. Our chosen bale handling integrator, LAC, has a long history of successful problem solving in partnership with Kawasaki Robotics, and the solution they provided with their CP180L robot for this application was perfect. From our viewpoint, we were impressed with the approach demonstrated by the entire robot and integration team, who provided us with excellent support and delivered first class teaching and training on installation”.
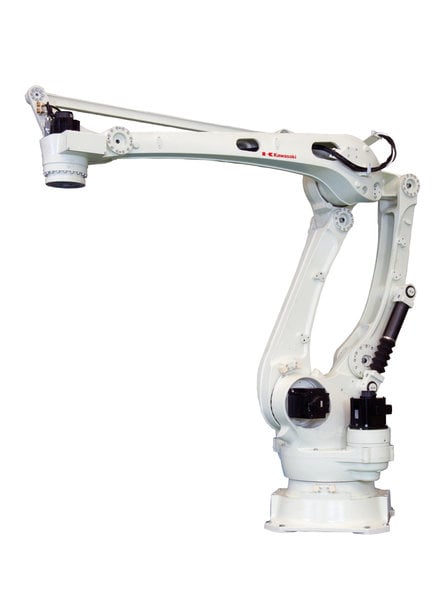
The Kawasaki CP180L robot can carry 180kg at a reach of 3255mm
Chris Unwin, CEO at LAC Conveyor Systems added “Fundamentally, our brief was to reduce labour costs, maximise the recycling opportunities and help minimise transportation costs. In this case, we needed to look beyond the normal points of reference and make our engineering match each clearly defined stage of a waste recycling process. The engineers from Impact Air Systems, Kawasaki Robotics and LAC made a great team and between us we met every objective that was agreed at the start of this interesting project”.
In conclusion, Kawasaki’s Ian Hensman says “Sound application skills coupled with our ability to provide both Impact and LAC with the latest simulation package was pivotal to all concerned. Our robot simulation software allows customers to add 3D models of Kawasaki robots, peripheral equipment, robot tools, and workpieces into a virtual environment and build multi-robot automation work cells. It allows us to design the perfect installation for a customer and to prove that it works long before any metal is cut”.
www.robotics.kawasaki.com