www.ptreview.co.uk
09
'20
Written on Modified on
Stopping sparks flying
The design considerations of hot-disconnect connectors.
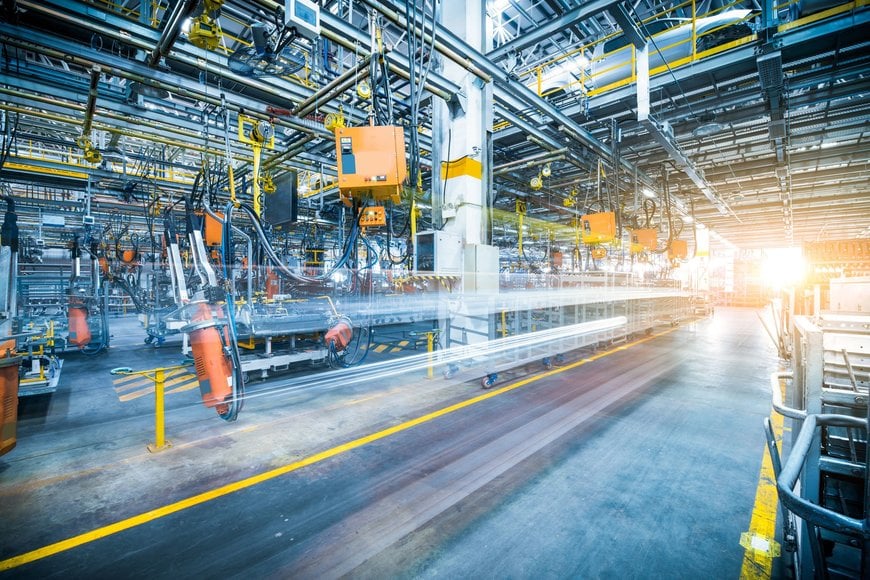
Imagine needing to go to the breaker box to turn off your entire home’s electricity supply every time you want to plug or unplug something. Now take that inconvenience and scale it up a thousand times. Imagine a factory needing to disconnect equipment thousands of times a day, possibly in explosive or hazardous atmospheres, and the problem becomes clear. Here Nick Lewis, product manager at cable and connector specialist PEI-Genesis, discusses hot disconnecting in industry.
The UK has the best plugs in the world, at least as far as YouTuber Tom Scott is concerned. Once you go through the arguments it’s difficult to disagree. British plugs include fuses, a built-in ground terminal and yank protection, which are found almost nowhere else in the world.
One particularly innovative part of the design is that the ground terminal is five millimetres longer than the live and neutral terminals. The ground makes contact first, which provides an escape route for any excess charge as the live and neutral contacts mate a moment later. The practical upshot of this is that British plugs are far less likely to arc when connected or disconnected.
Connecting and disconnecting powered connections like this is known as hot disconnecting in industry and, while avoiding arcing is beneficial for safety in the home, in industry the risks are far higher.
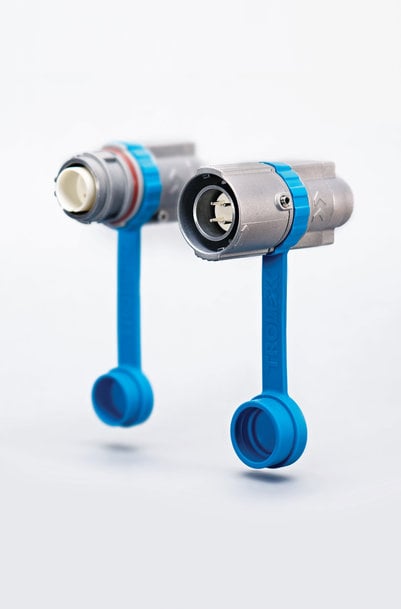
Only disconnect
The first question is — why hot disconnect at all? If equipment is powered down before disconnecting, all the associated problems can be avoided. For small industrial applications this is acceptable, but as factories expand this solution becomes impractical. Powering down equipment can lead to major losses in production and can be a very time consuming and labour-intensive process to plan and implement.
Many industries work this way, and the only real consequence is a reduction in the connector’s cycle lifetimes as the arcs slam into the contacts over and over. This arcing can lower cycle ratings by over 500 times, so it’s certainly a factor to keep in mind, but the increased cost of replacing connectors 500 times more frequently are massively outweighed by the increased production generated by keeping equipment powered up.
Another contributing factor is that industrial voltages are often many times larger than the 230 volts of home circuits. The possibility of arcing is a direct function of the voltage and the distance between the contacts, so a larger voltage makes for stronger and longer arcs.
Because the contacts start off touching, some arcing is unavoidable at the point they un-mate. This is limited in connectors which include a longer grounding terminal, just like the standard British plug, but arcing will always occur to some degree.
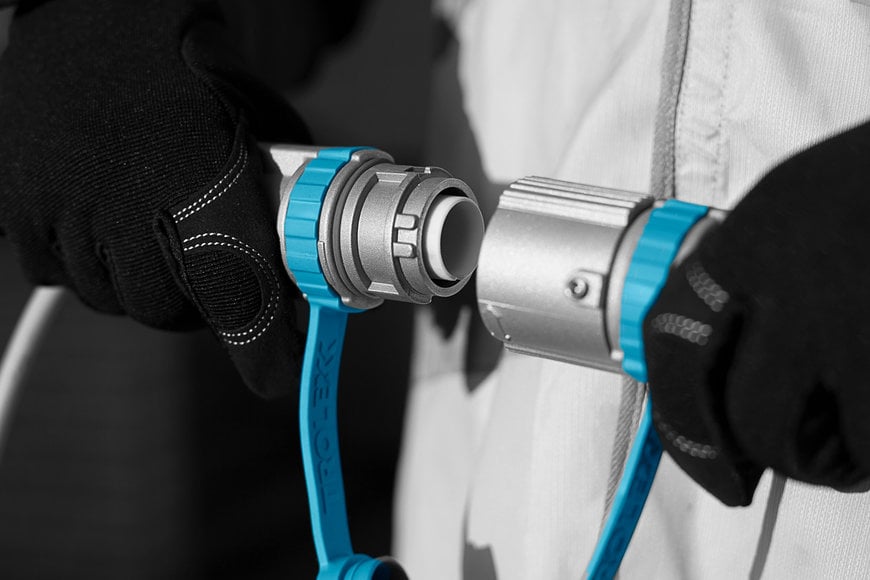
Only connect
However, there are some industrial situations where even minor arcing poses danger, most notably explosive environments.
The threat of catastrophic explosive consequences for arcing in these environments means that ATEX certified hot-disconnect connectors require an additional design consideration. These connectors, like the Trolex Falcon25, use a two-stage connecting process.
First the enclosure mates, and then the live contacts. This creates an explosion-containing capsule, meaning that if there is an explosive atmosphere present to be ignited by the arc, any explosion is safely contained within the capsule and therefore doesn’t have the opportunity to spread.
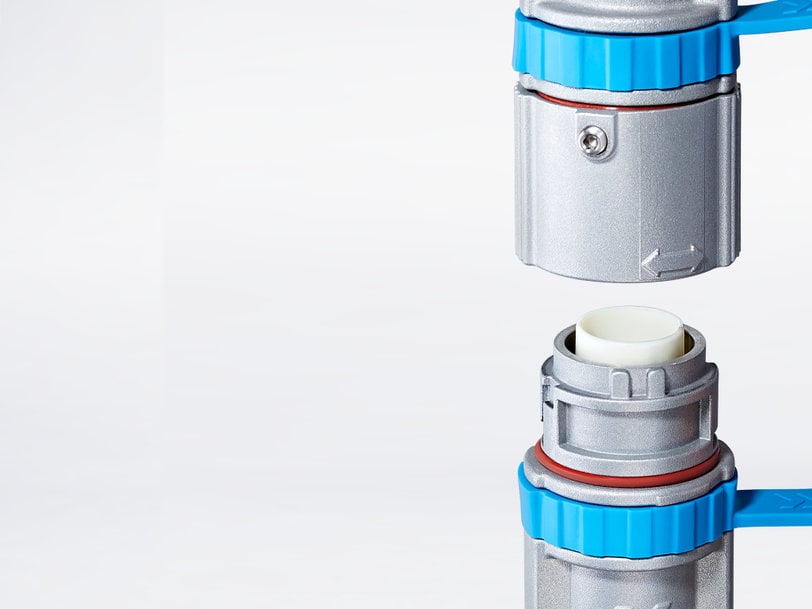
Hot disconnecting equipment is something that almost every industry does, but how many plant managers keep the connectors in mind when they do so? A hot disconnect in your home probably feels natural and doesn’t have any negative consequences if you are using an ultra-safe British plug. But, in a factory, it will reduce connector lifespan. However, sacrificing connectors for productivity is a sensible trade off, just one you should understand before you make.
www.peigenesis.com