www.ptreview.co.uk
06
'20
Written on Modified on
VDM Metals adopts Henkel’s nitric acid-free pickling process
More sustainable and cleaner nickel alloy production.
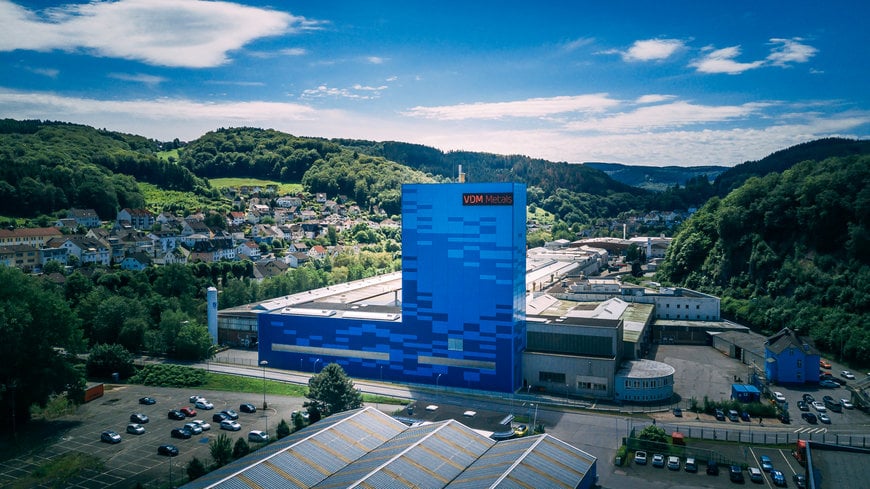
VDM Metals Group, a German manufacturer of nickel alloys and special stainless steels, has adopted Henkel’s next generation nitric acid (HNO3) free Bonderite C-CP (“Cleanox”) pickling process for dedicated wire products. The Bonderite C-CP product range answers market requirements within the metals industry to significantly increase the sustainability value of their production processes.
The Cleanox technology has already been in use for decades in multiple industries globally, including wires, tubes, coils, bars, and components. It is suitable for all stainless steel grades, and can be used in multiple applications, including immersion, spray, continuous line, or batch solution processes. VDM Metals, based in Werdohl, is using Henkel’s Cleanox technology to pickle rolled wire of high-alloyed materials in order to ensure the compliance with NOx limits.
Bjoern Lorenz, Sales Manager Metal Coil at Henkel for Western Europe, says: “Henkel is determined to play a decisive role in environmental protection, aligned with our company strategy, by offering our customers a reliable, flexible and sustainable pickling process for stainless steel in the metal coil industry. Customers such as VDM Metals have been benefiting from competitive production costs, whilst realizing a significant contribution to both ecological improvement and production safety. Together with our chemical and electric pickling, paired with our equipment to automatically control and dose chemicals, we are able to offer a systematic package to customers who are focused on increasing their sustainability.”
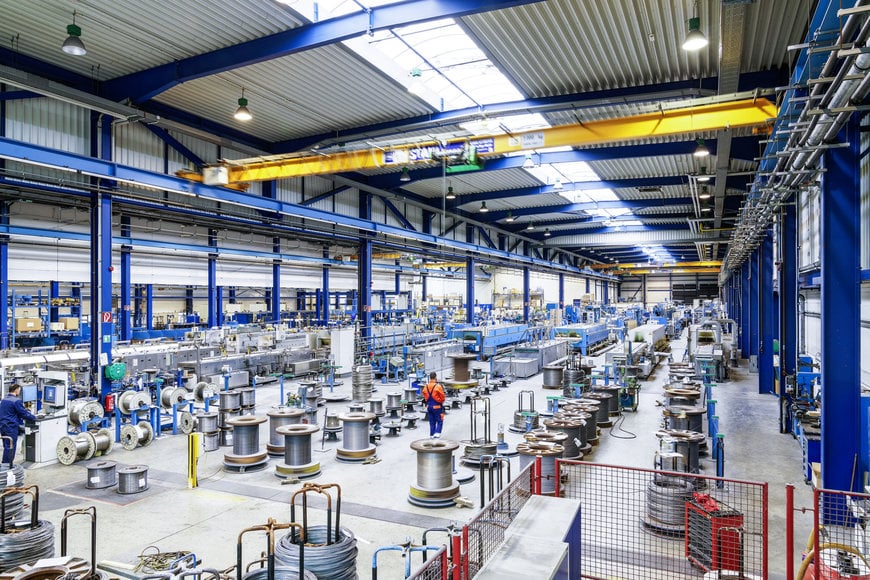
High-alloyed nickel chromium alloys are commonly used in multiple industries, including the automotive, petrochemical, aviation, power generation & electrical, chemical and appliances sectors. But there are challenges around common mixed acid pickling systems, due to the use of nitric acid. These cleaning techniques typically result in vast volumes of nitrate ions being discharged, during the intermediate and final rinsing stages. Nitrate and nitrite pollution is subject to legislative regulation and needs to be complied with via waste water treatment.
A further drawback for common mixed acid pickling processes is the need to treat nitrogen oxide (NOx) fumes, in order to avoid air pollution. It is technically possible to clean nitrogen oxides by different procedures, but it requires investments in equipment, process control and maintenance.
Both factors also determine the productivity of the pickling process, the waste water treatment and waste disposal.
Henkel’s Bonderite C-CP overcomes these environmental and cost hurdles with the latest in its line of nitric acid-free cleaning technologies. The lower amount of sludge created by the new technology, when compared to the traditional process, is a further sustainability advantage. Furthermore, global process costs are equal or lower than traditional processes, when this fully automatic technology is used. The Bonderite C-CP process can be used in spraying or immersion lines. It is suitable for any stainless steel or special grades based on austenite, ferrite, martensite, duplex or superduplex, including high-chromium AISI/SAE 4XX qualities.
Olaf Kazmierski, SVP of Production at VDM Metals in Werdohl, is very positive about both the sustainability potential of the new technology, as well as the collaboration with Henkel. “Our adoption of Bonderite C-CP has allowed us to optimize the pickling process. Henkel’s advices on how to manage the process and optimize the consumption were the base of the flawless change from mixed acids to the Bonderite technology. The problem of nitrate loads has been clearly mitigated. Meanwhile the process works without any problem, the new pickling procedure is well established.”
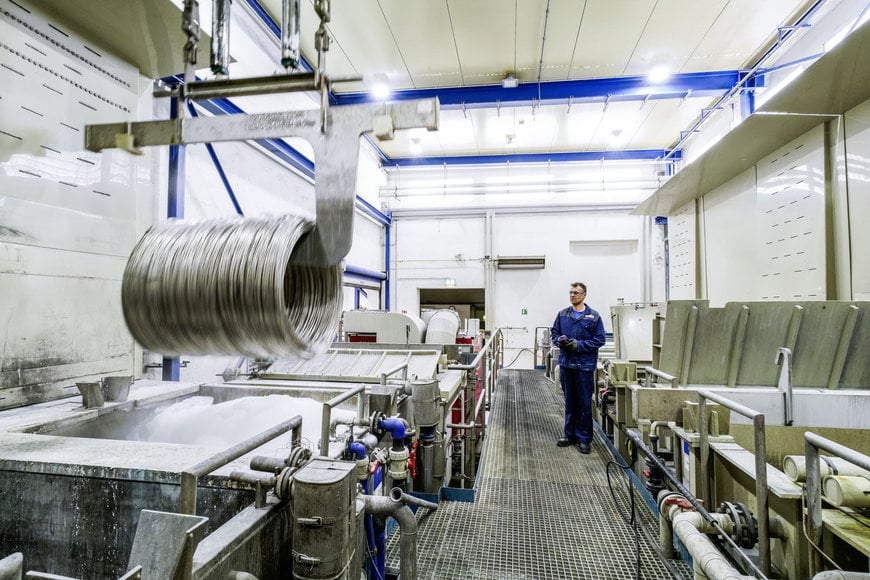
The latest innovation in the Cleanox range is the deployment of acid recovery acid machines that make the technology even more cost effective and sustainable. This equipment is offered by Henkel to fulfill multiple purposes, but primarily to further reduce any sludge remaining in the production system, as well as for the recycling of used Bonderite C-CP products. Through employing these machines, customers can significantly save costs for product consumption and further reduce their ecological footprint.
Henkel began offering its range of Bonderite C-CP technologies in the 1990s, to address the growing market demand for nitric acid free pickling technologies for stainless steel. Since the initial introduction, legislation governing this space has tightened in the EU, in accordance with the European Community Directive (96/82/EC) (known as “Seveso”), which further restricts the usage and storage of hydrofluoric acid. Henkel’s latest generation of Bonderite C-CP is fully in line with these regulatory requirements. VDM Metals is one of the first manufacturers of high-alloyed non-iron metals to adopt the process in their production.
Aziz Mabrouki, Head of Metal Coil Europe at Henkel, concludes: “Cleanox technology has not only been rolled out across Europe, but all across the world. We are able to offer integrated solutions ranging from chemistry to expertise and equipment to support stainless steel makers and users to be compliant with new directives, such as the Chinese central government’s regulations around nitrite emissions.”
www.henkel.com