The InnoventPro Metal 3D Printer
The world's most advanced entry-level metal 3D printer using binder jetting.
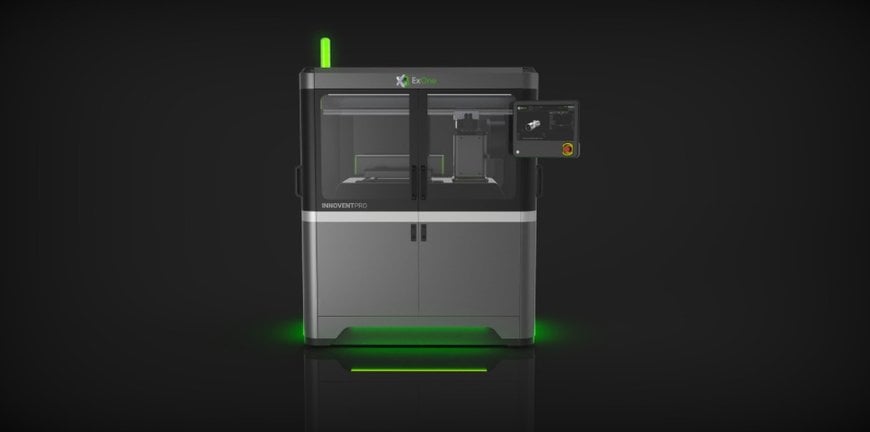
Production Metal 3D Printing Starts Here
ExOne Reveals Advanced InnoventPro Metal 3D Printer Concept
- InnoventPro to be the world’s most advanced entry-level model for metal binder jetting
- New 3D printer to supersize the build area of the world’s best-selling metal binder jetting system, the Innovent+, offering two new size options
- Upgraded printhead will more than triple print speeds, slashing the cost per part
- Offering all-new functionality in binder jetting: Option to 3D print a new class of patented NanoFuse binders embedded with nanoparticles to improve part quality and simplify sintering
- InnoventPro rounds out ExOne’s full family of production metal binder jetting systems and accessories, which now includes the X1D1 automated guided vehicle for Industry 4.0 operations
The ExOne Company (Nasdaq: XONE), the global leader in industrial sand and metal 3D printers using binder jetting technology, today debuted a concept rendering of the InnoventPro, a preview of the world’s most advanced entry-level binder jetting system for printing metals, ceramics and composites.
The InnoventPro will be a major upgrade of the Innovent+, the world’s best-selling metal binder jetting system since 2016. The InnoventPro will offer two new build sizes, a 3-liter and a 5-liter, with print speeds topping 700 cc/hour. The updated system is aimed at academics, researchers, and a full spectrum of manufacturers, from machine and MIM shops to high-volume producers, who want to produce metal parts quickly, affordably and sustainably.
“Customers around the world already love the Innovent+, and based on their feedback, we’re going to give them an updated entry-level system that’s bigger, faster and smarter than ever,” said John Hartner, ExOne CEO.
Siemens Digital Industries will serve as an Industry 4.0 collaboration partner on the production version of the machine, to be unveiled in the second half of 2021. An incentive program for the InnoventPro will be offered to customers who buy an Innovent+ prior to commercial availability of the new system.
Raising the bar in binder jetting
Binder jetting is a groundbreaking 3D printing process that uses a digital file to quickly inkjet a binder into a bed of powder particles — metal, sand or ceramic — creating a solid part one layer at a time. When printing metals, the final part must be sintered in order to fuse the particles together into a solid object.
Binder jetting is a sustainable method of manufacturing that reduces material waste to less than 5%, saves energy by consolidating many assembled parts and processes into one, and can deliver end-use products that are 30-40% lighter — for more efficient cars, planes and military equipment.
Importantly, the new InnoventPro will feature the same recirculating printhead modules used on the X1 25Pro® and X1 160Pro metal 3D printers, allowing users to easily scale up from R&D to high-volume production.
The recirculating printhead also enables ExOne’s pioneering move to offer particulate binders as an option on a commercial binder jetting system. The ExOne research team has been 3D printing a variety of nanoparticles suspended in its binders for years.
All-New Class of NanoFuse Binders
First patented in 2018, with related patents pending worldwide, ExOne’s “inkjet-printable nanoparticle suspensions” are slated for commercial deployment in the InnoventPro. This all-new class of ExOne NanoFuse binders advances the field of binder jet 3D printing in critical ways.
Because nanoparticles fill in the interstices between powder bed particles and can bond at lower temperatures, they enable stronger green parts. In turn, this enables 3D printing of larger parts and finer features, delivering sharper corners and edges. These new binders can also improve the resolution and sinterability of high-demand metals, such as copper and aluminum.
Rick Lucas, ExOne CTO and VP, New Markets, said the InnoventPro and new NanoFuse binders show how ExOne continues to lead the way in commercial development of binder jetting.
“Just as the current Innovent+ served as the proving ground for our patented Triple ACT system, which now delivers industry-leading quality in metal binder jetting, the InnoventPro will offer groundbreaking new features in a commercial system,” Lucas said. “Our patented approach to 3D printing particulate inks in a print bed is opening new doors in binder jetting.”
ExOne’s patented Triple ACT is a critical advanced compaction technology that, depending on material, delivers industry-leading final part density of 97+%, dimensional tolerances in the range of <1%-2.5%, and high consistency, with part variation of just 0.3% across the print bed.
Triple ACT has been so effective that it has also sped up ExOne’s qualification of new materials. ExOne binder jet systems now process more than 20 metal, ceramic and composite materials, with single-alloy metals making up more than half of those offerings. NanoFuse binders are expected to expand that material range and improve sintering dynamics.
A webinar about NanoFuse will be held at 9 a.m. on Wednesday, Nov. 4. Details are available at https://tinyurl.com/NanoFuseWebinar.
www.exone.com