www.ptreview.co.uk
28
'20
Written on Modified on
SMC Customer case – Expertise in: Meeting your challenges
SMC’s position sensor transforms 360-degree window sanding machine from MB Maschinenbau into a true all-rounder.
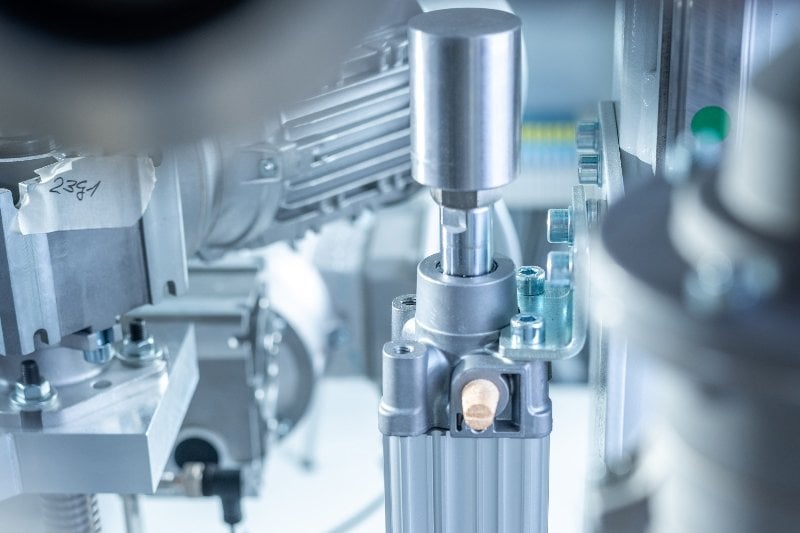
Turned into all-rounder: Sanding machine for window parts now also sands door frames By Nils Boy, Sales Engineer at SMC Deutschland GmbH.
Is there a draught? If the answer is “yes”, then the window frame or door frame doesn’t fit properly. To ensure your home stays warm and the doors and windows to look attractive, all parts for these products need to be produced with great precision and sanded to perfection. Conventional all-around sanders can only be used either for window or door components. With just a minor design change, MB Maschinenbau has now made its ROBA Fentech profile sanding machine for wooden window profiles also suitable for door frames. When combined with an optical sensor, the D-MP position sensor from SMC ensures that the machine optimally recognizes all workpieces.
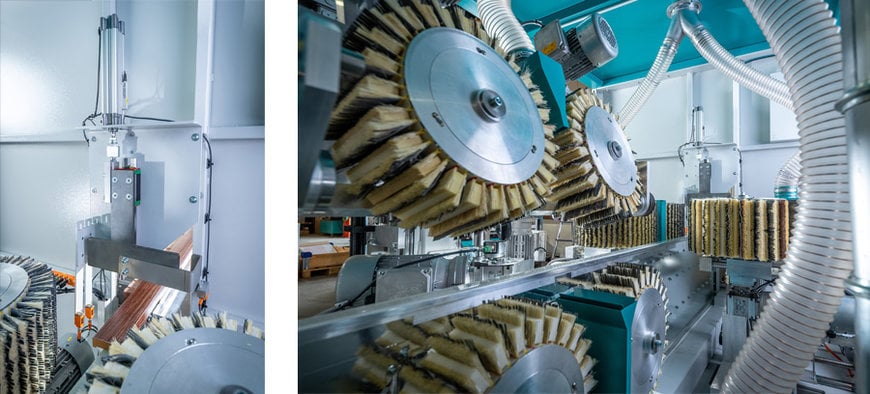
When a workpiece is inserted into the front of the ROBA Fentech profile sanding machine, an optical sensor detects its dimensions and automatically adjusts the sanding tools optimally – thanks to the innovative solutions from SMC, the machine can now even process door frames easily.
Wood doesn’t just need sanding as a finishing touch – before a workpiece is ready for delivery it goes through several sanding stages, from sanding the raw wood, to sanding between varnishes, through to the fine sanding. The variety of parts is immense and sanding by hand is very time consuming and labour intensive. Production efficiency can only be raised using highly automated solutions. MB Maschinenbau has developed a plant suitable for such requirements; the ROBA Fentech profile sanding machine. It recognizes the contours of each individual workpiece automatically and adjusts its sanding aggregates accordingly.
Until now, the Fentech has not been considered suitable for door frames, because such profiles are normally L-shaped, and the short leg of this combination was not detectable by the optical sensors used so far. By adding another cylinder and optical sensor, MB Maschinenbau was able to modify the configuration in a way, that also such complicated door frames can be processed. Thanks to SMC’s position sensor, the machine recognizes such door components when they are inserted into the machine.
Founded in 1992 in Herford, MB Maschinenbau GmbH develops, produces and sells sanding and special machines for the wood and metal industry – from one-off solutions through to series production. In recent years, the company has focused on wood machining, with a key focus on sanding. In addition to its headquarters in Herford, the company also has a subsidiary in North Carolina in the US, which sells its specially-produced machines internationally.
Automated sanding for a wide variety of parts
When designing window frames, there are almost no limits to the imagination. The range of wooden parts that have to be processed is accordingly large. “This makes sanding window profiles an especially demanding task, because the machine has to cope with a high level of variance without any major setup efforts,” says Ronald Busch, managing director and owner of MB Maschinenbau. “Ultimately, all parts should not only fit together perfectly, but must also offer the desired aesthetic and haptic qualities.” For a perfect surface finish, you either need to use time-consuming manual sanding, or a flexible automated solution.
That is why MB Maschinenbau developed the ROBA Fentech. This sanding machine is fully automatic. When a workpiece is inserted into the front of the machine, an optical sensor above the inlet detects its shape and dimensions, and positions the sanding aggregates inside the machine using an algorithm stored in the PLC (Programmable Logic Controller). Measuring 400 mm in diameter, the sanding tools ensure optimal contact with the surface of the wood. The inbuilt sanding tool jump control prevents the short edges from being sanded too aggressive. A new type of vacuum transport system conveys even small workpieces through the machine, which would not be able to be processed by conventional sanding machines.
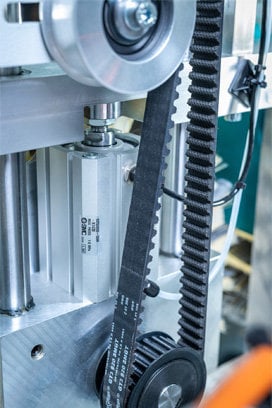
Door frames have milled “noses”, which cannot be recognized by a single optical sensor. Pneumatic cylinders from SMC therefore clamp the workpieces at the inlet of MB Maschinenbau’s ROBA Fentech machine – this enables to detect the height of the profile noses.
Making the sanding machines fit for use on doors
Many of MB Maschinenbau’s customers don’t just need to process window frames, but also door frames. “This poses a special challenge for our sanding machines,” says Petra Darnauer-Busch, Design Manager at MB Maschinenbau. “Door frames generally have an L-shaped profile. The short profile leg, which always hangs to down on the left side of the vacuum transport system, can vary in length.
Until now, the optical sensor on our ROBA Fentech could not recognize neither measure the underside of the planed nose.” The short leg of the L-shaped door frame profile lies against the wall of a doorway once mounted to cover the joint. As it is often integrated into the design of the door – its dimensions and milling contour can vary widely. In order to embed this level of variance into the machine control system, we would have been forced to build a completely new machine.
MB Maschinenbau chose a particularly efficient solution instead: The special purpose machine experts adapted the tried and tested ROBA Fentech profile sander to process door frames. “The main task of this redesign was to reliably detect the length of the noses on the door frames,” says Ronald Busch. “That is the only way that the sanding machine can position its tools precisely and machine the workpiece reliably and optimally.”
For this reason, MB Maschinenbau GmbH uses a D-MP position sensor in combination with a pneumatic cylinder from SMC in its ROBA Fentech. “The analogue position sensor works alongside the optical sensor,” explains Petra Darnauer-Busch. As soon the workpiece is inserted into the machine, the sensors start to work in tandem. While the optical sensor detects the end of the profile nose, the D-MP equipped cylinder engages and clamps the wooden piece. From the measured end position of the piston rod and the optically measured position of the nose end the sanding machine’s control unit calculates the length of the profile nose and adjusts the lower sanding tools accordingly.
With the help of a fixing slot the D-MP position sensor can be easily mounted on virtually all SMC cylinders. With a repeat accuracy of ±0.1 mm it is incredibly precise and furthermore compatible with the IO-Link communication standard. Not only it can quickly incorporate its measurements into the control system’s calculations, but also can be parameterized and monitored remotely. “Thanks to its IP67 protection class, the sensor is also protected from dust and water, which ensures reliable operation in the long term,” reports Petra Darnauer-Busch.
Precise all-rounder for windows and doors
The ROBA Fentech profile sanding machine has become a true all-rounder. “With minor design changes, we can now provide our customers a sanding machine that is perfectly tailored to their needs,” says a delighted Ronald Busch. “Whether it’s for door frame profiles or wooden window frames. So far, this is unique in our industry. SMC’s position sensor is the key component in this development; it fits our requirements perfectly.”
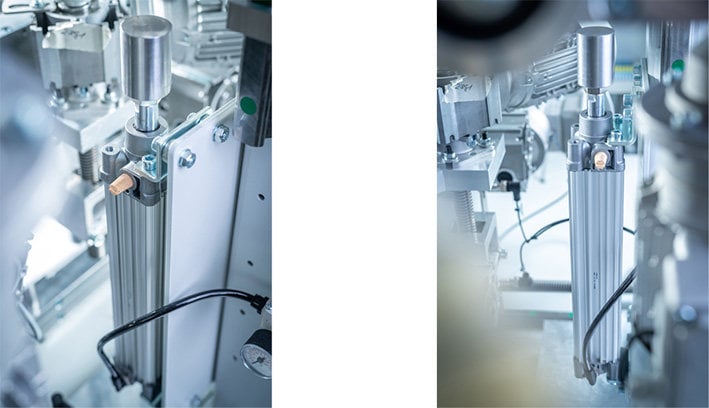
In combination with an additional optical sensor and pneumatic cylinder, the D-MP position sensor from SMC measures the height of the milled noses of the door frame and enables MB Maschinenbau’s ROBA Fentech profile sander to adjust itself perfectly.
www.smc.eu