www.ptreview.co.uk
28
'20
Written on Modified on
Automation in Automotive Engineering: Sensitive Robot Increases Efficiency in Final Assembly
Car manufacturers are looking for solutions to increase the efficiency of assembly on the assembly line. Innovative automation solutions should increase the degree of automation. Human and robot share the workplace along the assembly line.
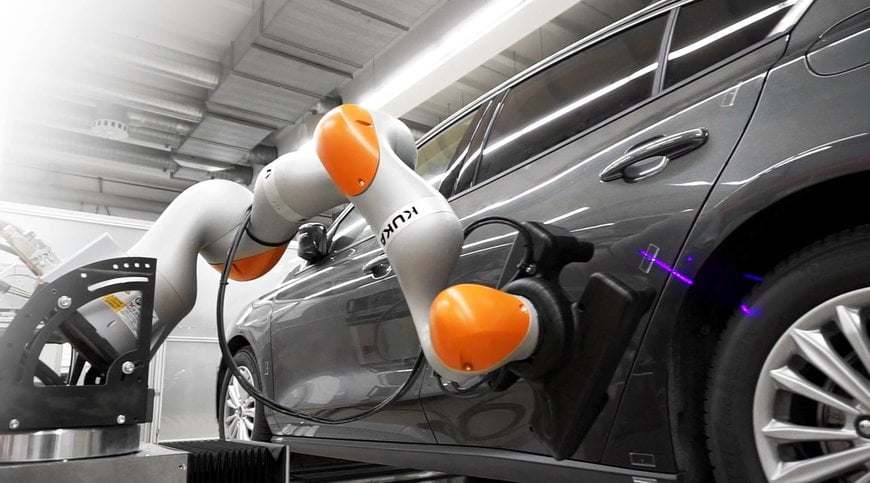
With its sensitive capabilities, the LBR iiwa from KUKA measures gap dimensions and flushness of body components such as between the tailgate and side wall or between the headlights and hood. At the same time, the worker carries out further quality tests on the car body. Automation in final assembly is a fairly new field. The fact that humans and robots share the workplace along the flow assembly line has been a rarity up to now.
" The measurements are relative to the component. This enables the robot to carry out its measuring task completely autonomously in flow operation. In contrast to conventional robot-supported measurement, this is a real added value. "
Otmar Honsberg, Head of Application Engineering at KUKA
In combination with optical detection and its haptic sensor technology, the sensitive KUKA LBR iiwa automatically adapts to new situations in the event of belt vibrations or stops, and continues to carry out its work seamlessly. "The "Assembly in Motion" solution makes the robot an intelligent positioning unit for the measuring device", adds Honsberg.
Increase efficiency
The assembly lines in the assembly halls of car manufacturers move partially assembled car bodies along the processing lines, while fitters assemble additional parts or test quality features in cycle time operation. The speed of the assembly line is adapted to the human cycle so that assembly work or reworking of components can be carried out on the running line. To increase efficiency on the assembly line, man and robot must work together.
www.kuka.com