www.ptreview.co.uk
29
'20
Written on Modified on
High dynamic machining of small engine blades: go-Mill 350
The Liechti go-Mill 350 is considered the benchmark for machining airfoils up to 350 mm in length
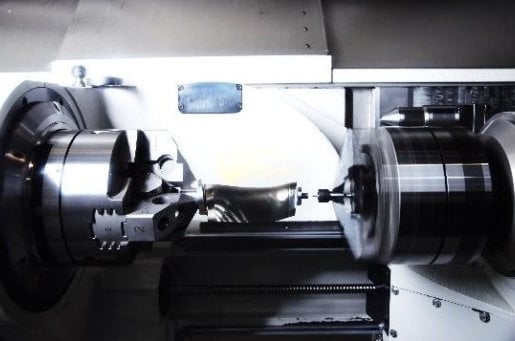
This Liechti five-axis machining center was introduced to the market in 2008 and thanks to continuous updates and improvements, almost 100 of these machining centers have already been put into operation. In this market niche, this is an impressive number—and it is not surprising that customers include renowned manufacturers from the aerospace and power generation (OEM) sectors.
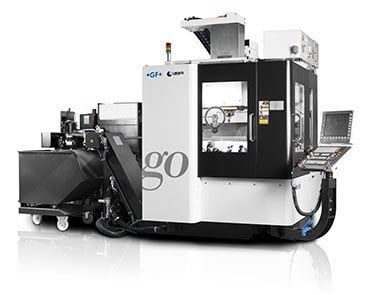
The compact design of the Liechti go-Mill 350 allows good accessibility and optimal visibility of the workpiece.
The go-Mill 350 was able to establish itself with these OEMs as a complete solution from Liechti thanks to its numerous advantages, but above all due to the reduced machining time, a higher surface quality and immaculately machined leading and trailing edges. The Step-Tec high-performance Spindle is equipped with an HSK-A63 tool interface and achieves 20,000 rpm with a torque of 120 Nm. Together with the five highly dynamic axes, this forms the basis for time- and thus cost-efficient blade machining.
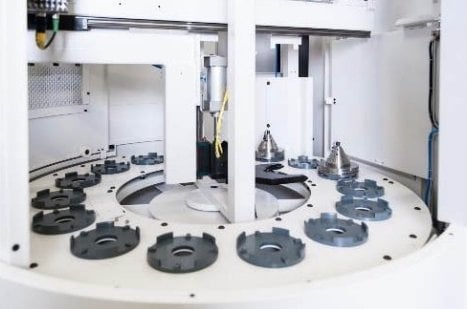
16-fold pallet changer is optionally available. The automation is extremely compact and considerably reduces the workpiece changing times.
The machining centers can be—as is customary at Liechti Engineering—individually adapted to the customer. In addition to many other options, tool changers with 30 or 60 positions as well as with rotary drives on both sides, which are designed for rotary applications up to 1,000 rpm, are also available. This solution impresses with its compact design (6.6 x 3.9 m including 16-fold pallet changer), which means that less space is required in the production hall.
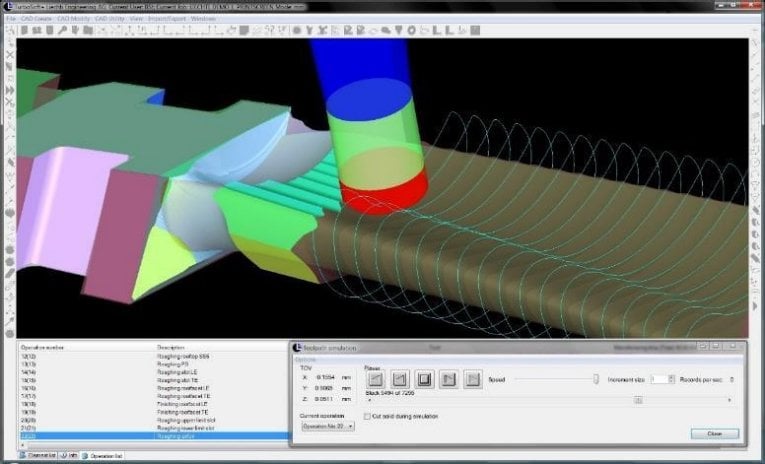
The CAM software Turbosoft plus has been specially developed for flow flats.
The machining center is optimally complemented by the CAM software Turbosoft plus developed in house at Liechti. This specialized software enables efficient programming of blades and blisks. The combination of the machine, the technological competence of Liechti application engineers and the CAM software results in a powerful overall solution from one source.
www.gfms.com