www.ptreview.co.uk
04
'20
Written on Modified on
Enough Space for a Cool Head
What should you do if you want an ergonomic lifting aid, but your ceiling height is too low for conventional crane systems? Schmalz’s solution is a modular flat jib made of aluminum that guarantees smooth movement sequences, even in low rooms. This novelty arrived at just the right time for Erkodent: The dental thermoforming device manufacturer wanted to optimize the packaging process at the end of the assembly line and needed a solution that left enough space for an air-conditioning system that had already been planned.
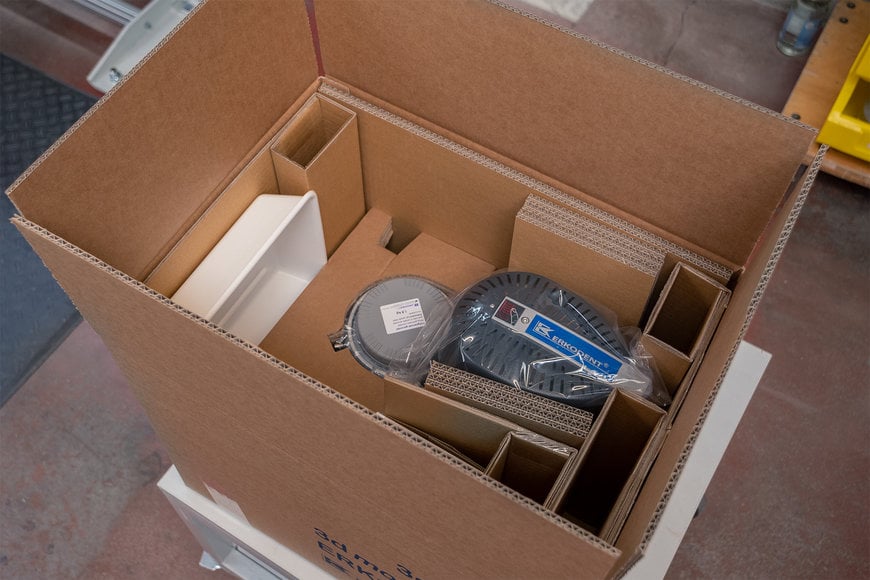
Erkodent produces high-quality products for dental technology, dentistry, and podiatry. It all started with a dental clinic in Pfalzgrafenweiler near Freudenstadt for which Erich Kopp received his health insurance license in 1954. Based on his practical experience, he soon began developing his own instruments to make treatment easier for both him and his patients. Erkodent Erich Kopp GmbH grew out of his efforts and has since become one of the world market leaders in dental thermoforming technology. In 1980, the company founder established a second mainstay in podiatry. It currently accounts for approximately ten percent of turnover.
Around 80 employees develop, manufacture, and package pressure and vacuum equipment for thermoforming in Pfalzgrafenweiler on approximately 8,000 square meters of manufacturing space. Dental technicians use this equipment to form custom impression trays, molded parts for temporary treatments, and teeth-whitening trays. Corresponding accessories and material like plastic film, silicone, and waxes are also part of the range of products, as are guards for athletes and mandibular advancement splints to prevent sleep-related respiratory disorders. What all products have in common is their high quality standard, which the family-owned company maintains using audits and multi-stage quality monitoring in goods receipt, production, and finished solutions.
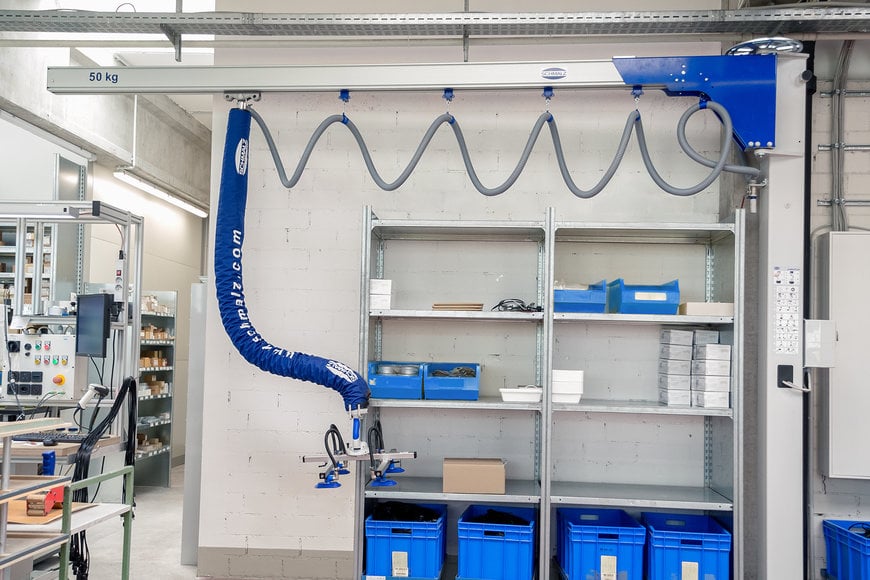
The flat jib leaves enough space on top for ventilation shafts, media lines, and the planned air-conditioning system.
First the Check, then the Strain
“Once a vacuum thermoforming device reaches the end of the assembly line, it is checked first. Then it is safely packaged for shipment,” explains Andreas Weiß, who is responsible for process optimization at Erkodent. Together with the operating instructions and padding material, a finished package weighs between 15 and 25 kilograms – and they are generally growing heavier. “The package was then positioned on a pallet by hand so the serial number is always visible,” Weiß says when describing the part of the packaging process he wanted to improve. “Every day, we package between twelve and fifteen thermoforming devices. Stacking them onto the pallet by hand without a lifting aid placed great strain on our backs and arms,” Helmut Seeger recalls. He has been working at Erkodent for five years and collaborates with six more colleagues at the various assembly and packaging stations.
No Space for Cranes and Similar Equipment?
During his search for an ergonomic solution, Weiß contacted J. Schmalz GmbH. “We are already using vacuum lifters from Glatten at several workstations and are satisfied with them,” he emphasizes. The long-standing contact, positive experiences, and spatial proximity – the companies’ main offices are only 15 kilometers apart – were decisive factors that made the people responsible for the project contact Schmalz again. Their idea was to install an overhead crane system with a vacuum lifter. “That is a common solution, but we could not implement it due to a lack of space,” Weiß explains. Even if the system had fit between the existing ventilation and media shafts, at the latest, the overhead crane would no longer have had enough space when the air-conditioning system was installed. “We discussed the problem with Schmalz at the Motek 2018 and discovered the modular flat jib made of aluminum. It was the ideal concept for us,” Andreas Weiß remembers.
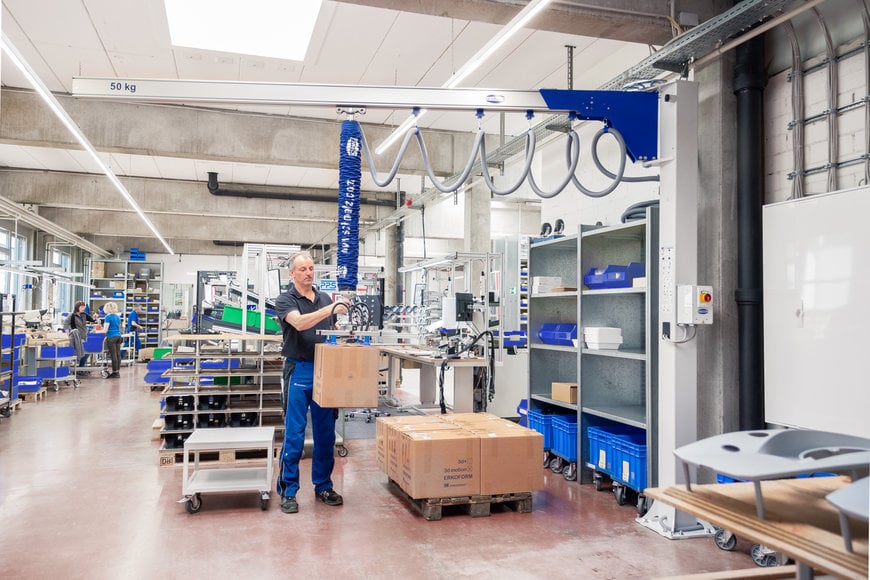
“Every day, we package between twelve and fifteen thermoforming devices, each of them weighing between 15 and 25 kilograms,” explains Helmut Seeger, an assembly employee at Erkodent.
The aluminum flat jib is based on the modular system for jib cranes. Compared to the conventional steel designs, the flat solution reduces the overall height of the new jib by up to 96 millimeters. With it, lifting devices may be suspended up to 340 millimeters higher than a standard aluminum jib with no increase in the overall height. “Thanks to the extra flat jib, the crane fits under the ventilation shafts and media lines and still leaves enough working space for the tube lifter,” Weiß notes. Not only the minimal height convinced Erkodent: The modular aluminum construction was less expensive and could also be assembled more quickly. Instead of being mounted on the ceiling, the column-mounted jib crane with its four-meter-long jib is safely mounted on the floor with a base plate. “That means we can be even more flexible because we can theoretically use the crane at another assembly location,” the person responsible for the process adds.
The extra flat crane solution has been in use since February 2019. To give its employees the best support possible, Erkodent hung the vacuum tube lifter JumboFlex 50 with a four-head suction cup fromi the flat jib. It can be used to pick up cardboard boxes weighing up to 50 kilograms and intuitively lift, lower, and release them with the main one-finger control. Stacking by serial number is also possible with no hassle thanks to the continuously rotatable handle. “Where our employees once needed to use all of their physical strength, they now essentially need only one hand,” Weiß summarizes. “The reduced workload is clearly noticeable. My colleagues and I are fitter and simply feel healthier,” Helmut Seeger confirms.
www.schmalz.com