www.ptreview.co.uk
11
'20
Written on Modified on
Simufact and Renishaw collaborate to streamline additive manufacturing simulation and build file preparation
Global engineering company, Renishaw, is collaborating with Simufact to enhance the success of laser powder bed fusion (LPBF) builds through accurate simulation and streamlined additive manufacturing (AM) build preparation.
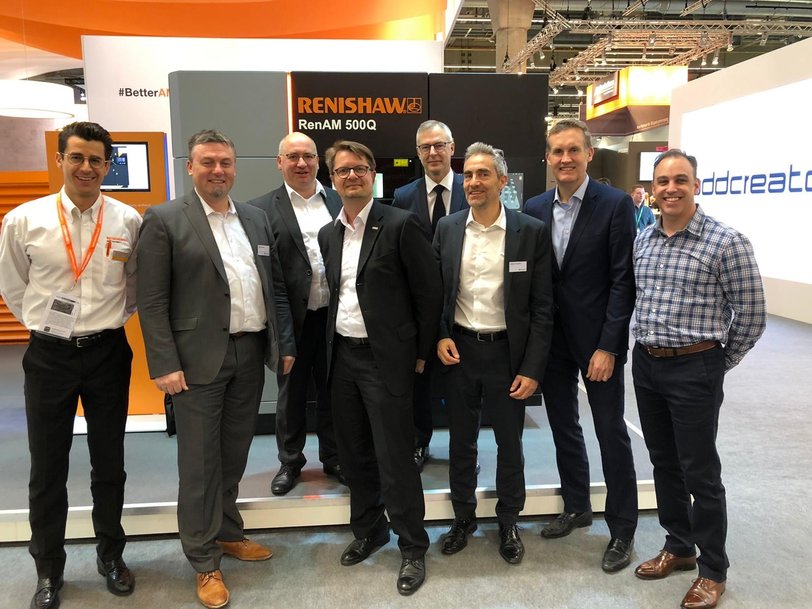
The collaboration includes the integration of Renishaw's QuantAM build preparation software into Simufact Additive 2020, announced at Formnext 2019. The two companies are also working together on improved simulation of the complex metallurgy of commonly used materials to enable successful prediction, and compensation, of stress and distortion during the printing process.
Simufact Additive 2020 includes an integrated Renishaw QuantAM API for build job preparation and export, which provides the user an error-free data transmission from Simufact Additive directly to Renishaw systems. This functionality also improves productivity because the entire work process from design to printed part is possible within the software. The QuantAM API now enables multi-laser build file preparation for Renishaw's popular RenAM 500Q quad-laser machine.
“Simufact Additive 2020 broadens the scope of our build optimisation software and underlines our commitment to openness and interoperability with third party products,” commented Dr. Hendrik Schafstall, CEO and Managing Director at Simufact. “With the integration of the QuantAM build processor, we can provide an end-to-end build optimisation process, helping the users of Renishaw systems to produce AM components with repeatable dimensional accuracy right first time.”
The collaboration extends to improving the simulation process itself. The increasing adoption of multi-laser LPBF systems for production applications presents new simulation challenges. Faster energy input from multiple lasers means that metal components often experience higher temperatures during the printing process, affecting their microstructure and resulting in different residual stress and distortion. The two companies are researching such phenomena to improve the accuracy of build simulations, enabling prediction of any distortion that may arise. This knowledge can be used to optimise the build process, and compensate the design to accommodate expected distortion.
“Our customers are looking to push the performance envelope using the latest multi-laser AM systems, but they also require consistency and precision,” explained Victor Escobar, AM Director - EMEA at Renishaw. “A seamless integration with Simufact's powerful simulation tools will help manufacturers to develop processes that take full advantage of multi-laser productivity, maximising build rates to make a stronger business case for AM.”
www.renishaw.com