www.ptreview.co.uk
09
'20
Written on Modified on
Process transparency included
Condition monitoring systems (CMS) detect changes and anomalies in the production process. They give an early warning of incipient damage, detect deviations in quality, monitor the stability of a production process and ensure consistent quality control at all stages of production and value creation. In this context, gripping systems and clamping devices are growing rapidly in importance due to their closest-to-the-part position.
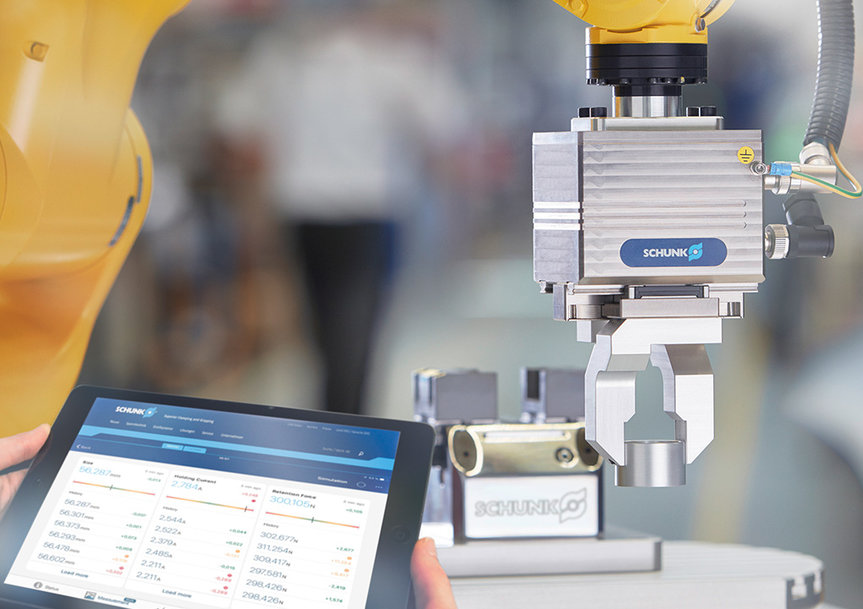
User demand for higher productivity, automated system availability and process reliability impacts the machines and automated systems used in modern production. The ability to carry out continuous condition monitoring is increasingly becoming a key criterion in component selection. The ability to analyze production and quality data at pace with production offers the potential for significant cost savings, higher operational efficiency and improved production quality.
Most importantly, the higher availability of automated systems and just-in-time maintenance have been shown to improve operational efficiency. Ideally, unplanned downtimes for automated systems can be completely eliminated. In turn, product quality can be increased by incorporating data on machine wear into the process controls and by predicting deviations from standard quality measures so that any necessary actions can be taken in a timely manner.
Not only reading data, but analyzing data
There is already an enormous amount of data being generated by the machines and automated systems, smart tools and components found in the factories of manufacturing companies. However, only a very small fraction of this data is actually being used - estimates suggest only about five percent. Values recorded by sensors have been given very little significance thus far, at most being used in the event of damage or for troubleshooting. By using this existing data comprehensively, systematically and most importantly in real time, smart manufacturing scenarios can be achieved that promise substantial benefits.
At the same time, the degree of networking and digitalization is also associated with a rapid increase in the amount of data being generated, meaning that there may be a risk that the connections to the cloud data centers may not be able to cope with the immense and rapidly growing data streams, and that downtimes and high latency periods could occur.
That is why current research projects are focusing on a fundamental shift in how data is understood. It no longer revolves around simply collecting data as was the case previously, but around analyzing the data on site and converting it into valuable information. The primary focus is on how to refine big data into smart data. For example, information on whether an automated system is operating properly and whether it is ideally linked to appropriate recommended actions needs to be prepared.
Integrated component testing
This allows component quality characteristics to be checked during handling and OK/NOK decisions to be made directly in the gripper. The data recorded in the gripper is pre-processed and analyzed in the components in real time so that the appropriate responses are triggered. This reduces the data volume to be transferred to what is truly required, i.e. a somewhat bewildering abundance of data is conveyed as meaningful parameters or key performance indicators (KPIs).
In addition to standard downtime statistics, the most important KPIs are the process capability indices (Cp) from the statistical process analysis and the utilization efficiency of the overall automated system. This measures three types of performance data and uses multiplicative methods to merge them into a comprehensive productivity indicator, the total efficiency of the automated system or the overall equipment effectiveness (OEE).
www.schunk.com