www.ptreview.co.uk
18
'19
Written on Modified on
Easily highlighting the potential of value creation
Target/actual state determined in just minutes
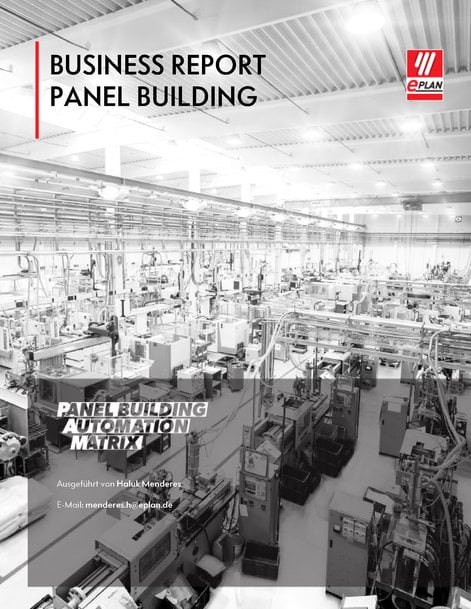
How can the value chain be optimized specifically for panel building? Where do companies stand with respect to the digitized and automated working methods that are available today? EPLAN presents the “Panel Building Automation Matrix” (PAM). It is based on a field study of 150 companies, including defined case studies. EPLAN consultants use PAM to analyse the individual status quo of customer-specific processes in panel building in just a few minutes. A benchmark comparison reveals specific savings potential that can be simultaneously implemented by EPLAN and Rittal in the area of machine technology, software and consulting.
Digitization along the entire value chain and data consistency across all processes and systems – these are the prerequisites for automating processes in control engineering and panel building. Yet what is the current degree of digitization in the industry? Where can potential still be found? Many companies just don’t know where to start.
Working methods analysed using benchmarks
EPLAN can help in this area: A new software-based method utilizes a field study of 150 companies worldwide to determine the optimization potential that is easy to achieve in close cooperation with EPLAN and Rittal as regards machines, software and consulting. A welcome ancillary effect of this implementation is a higher degree of digitization in manufacturing and the automation of repetitive tasks. “The Panel Building Automation Matrix (PAM) is a tool we’ve developed to analyse a company’s working methods in control engineering and panel building almost at the push of a button that shows unused potential in manufacturing processes,” says EPLAN Managing Director Haluk Menderes.
PAM offers an analysis and evaluation of the current workflow for manufacturing electric control cabinets as regards profitability and efficiency. The evaluation includes recommendations for optimization, their implementation and the required investments. What’s interesting for customers are listings of exact time savings in a variety of areas within the workflow – including wiring, device labeling or in NC production. A precise ROI analysis provides information on when for instance an investment in software pays for itself.
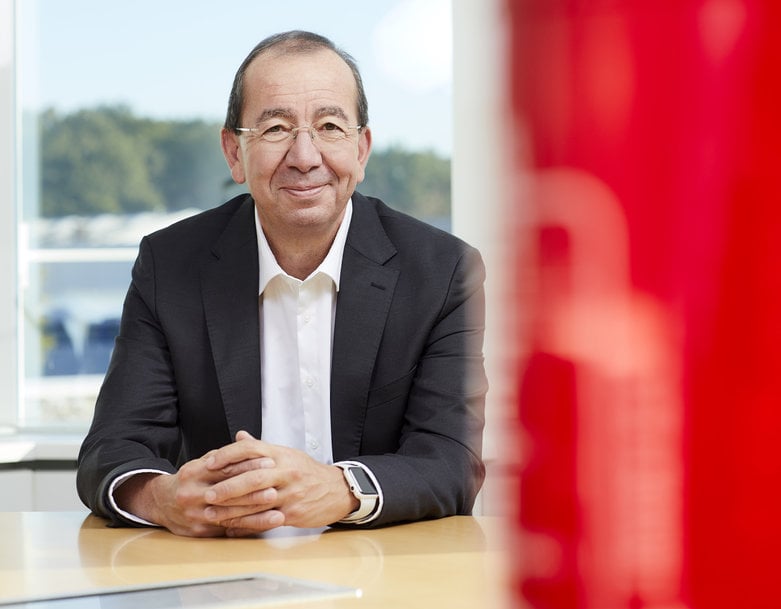
Haluk Menderes.jpg: “The Panel Building Automation Matrix (PAM) is a tool we’ve developed that analyses a company’s working methods in control engineering and panel building almost at the push of a button and shows unused potential in manufacturing processes,” says Eplan Managing Director Haluk Menderes.
Professional advice – valid results
EPLAN has been using PAM globally since early May 2019 and the feedback from the first customers in the US is enthusiastic. “With PAM, EPLAN has combined its decades of expertise in panel building into a viable, personalized ROI plan for our workshop,” says A&E Engineering President Wright Sullivan. Jacob Wilson, Director of Engineering, Sales and Development at Design Ready Controls, says: “PAM was able to exactly reproduce our current operations and manufacturing times after just a twenty-minute evaluation.” That naturally motivates EPLAN and Rittal to add additional process steps to the analysis in the future. Plans include integrating additional software tools from Rittal – as well as an ROI review for purchasing the new Rittal Wire Terminal for automating wiring, for instance, or the fully automatic Perforex machining center. The PAM analysis is carried out by the sales department and is naturally free of charge and does not depend on the purchase of EPLAN or Rittal products.
Study demonstrates: Digital instead of manual wiring
The average time an electrical technician requires to install an electrical connection from the schematic as an actual connection in the control cabinet is 4.5 minutes. Around 31 per cent of the time required is spent on purely preparatory tasks – including reading the schematic and finding the sources and targets. Another 13 per cent of the work time is invested in preparing the wires – estimating wire lengths as an example. The remaining 56 per cent of the work goes into the actual wiring: cutting to length, installing the cable lug, crimping, routing.(1) It’s more the rule than the exception that the technician must scroll through the schematic a number of times during the wiring process to gather the necessary information and supplement it where required. This leads to about a third of the work time lost to reading and specialist interpretation of the documents. To be frank, this can be done much better – namely digitally! The system of choice here is EPLAN Smart Wiring, in which the data are based on a digital prototype that has already been verified and thus only allows correct results.
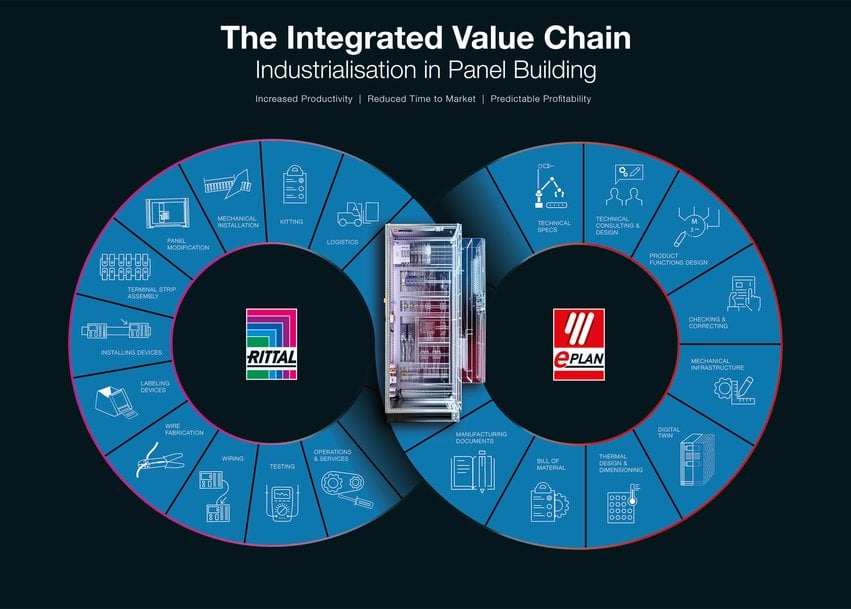
Integrated Value Chain.jpg: Nowadays, processes in control engineering and panel building must be made faster, more economical and more precise. Eplan and Rittal have the answers.
The declared goal: Integrated processes
By coupling engineering and production, EPLAN and Rittal create perfectly coordinated combinations of software solutions, systems technology, machines and services. The added value is obvious: Integrated solutions also enable integrated increases of productivity and efficiency in product manufacturing processes and beyond. To this end, engineering and design on the one side and work preparation and production on the other are integrated to form a continuous process. Digital device data, software-based tools and standardized interfaces in manufacturing are the prerequisites for this.
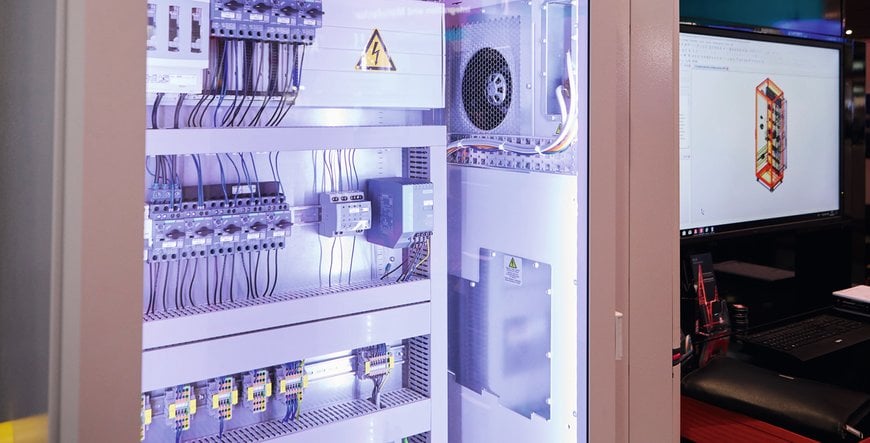
Schaltschrank.jpg: The increasing complexity of control technology and its components, customer desires for individualisation, national and international standards, last-minute changes and ever tighter delivery deadlines are putting enormous cost pressures on panel building.
Background:
The increasing complexity of control technology and its components, customer desires for individualization, national and international standards, last-minute changes and ever tighter delivery deadlines are putting enormous cost pressures on panel building. Instead of a future that relies on file folders with operating equipment lists, assembly plans and schematics as the central manufacturing documents, the value creating processes in control engineering and panel building must be made faster, more economical and more precise. This requires a change in thinking in this sector, a sector that has mainly remained somewhat bound by tradition. Yet companies have recognized that the greatest potential for setting themselves above the competition and creating unique selling points can be found in the individualized design of their value chain.