www.ptreview.co.uk
19
'19
Written on Modified on
When boundaries are tested and redefined
Technological progress continues to advance rapidly. Today, in the face of global competition, companies are finding that quality and reliability alone will not get them far. The world is changing and asking for better, faster, cheaper. To exceed customer expectations requires the desire to innovate in the development of production technologies and a willingness to change to efficient manufacturing processes. Eichenberger, the Swiss thread rolling specialist has succeeded in establishing itself in the drive technology niche with tailor-made, customized screw driving solutions. There is a constant demand for solutions to practical tasks. Somewhere there is always something that needs moving. Threading expert Eichenberger realized this a long time ago and has been able to successfully use the opportunities it offers. Their specialists listen to customers, give advice, design, build, test, optimize and manufacture. This is why their custom-tailored ball screw drives are being used everywhere, in medical, electrical, and automotive systems, as well as in automation, aeronautics and even in aerospace.
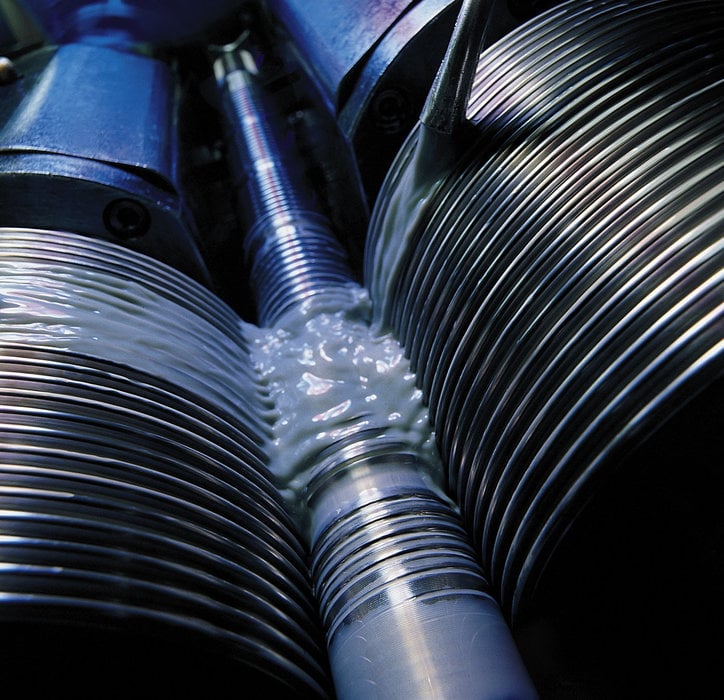
A microscopic look at the technique of cold rolling
What makes Carry ball screws so resilient and the ideal component for many applications ?
Thread rolling by means of the cold rolling process produces very precise geometries with high surface quality. Unlike with grinding, milling or turning, the longitudinal fibres of the material are not cut during the thread rolling but are deflected. The result is a dense surface, smoothly laminated, extremely resistant, essential for a long service life of the spindle. The roughness values of around 1.0 Rz at the edges of the thread and in the base radius as well as a significantly reduced susceptibility to indentation are major advantages. The friction coefficient of the steel balls is c. 0.0013. In comparison, lubricated steel has a coefficient of 0.1 to 0.05. The excellent gliding properties of the cold-laminated balls ensure minimal abrasion and offer minimal contact surface to contamination. As a result, it becomes child's play to make the balls run silently.
What makes the Speedy cold-rolled leadscrews so fast and long-lasting?
In many respects, spindles made by thread-rolling are worlds apart from spindles made by thread cutting. Price is a deciding factor. For example, with a rolled spindle it is possible to achieve helix angles that in the cut versions one could only dream of. Eichenberger's Speedy
high helix spindles have a helix angle of over 60°, whereas by comparison a metric M20 spindle only has an angle of 2.48°. The exceptionally high pitches also enable travel speeds without reaching critical rotational speeds. A key feature is the "smoothly rolled", compressed surface of the threaded spindles. For a long service life, rolled spindles are essential. The perfect matching of materials between the rolled spindle made of steel and the highly wear-resistant plastic is a decisive factor. The two components work ideally together and make it possible to guarantee essential basic conditions such as high temperatures (over 200°C), food conformity and maintenance-free operation.
The spindle pitch ratio, for example 18 mm diameter, 24 mm pitch in a drive system for a high tech facade made of stainless steel achieves extremely reliable positioning accuracy. The optimal combination of spindle, nut and lubrication results in a remarkably high efficiency factor of η 0.65. The manufacturer is thus has the option of using a lower power motor which takes less space.