www.ptreview.co.uk
03
'24
Written on Modified on
SICK presents AI-based robot guidance system
PALLOC combines a high-performance 3D snapshot camera with a factory-installed and pretrained neural network and a new Deep Learning-based localization algorithm.
www.sick.com
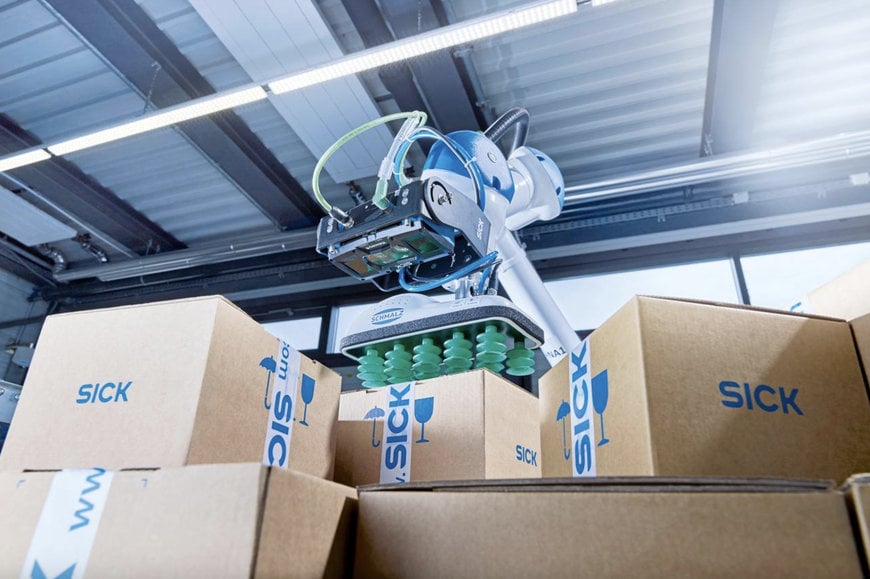
At the SPS 2024, SICK presented the robot guidance system PALLOC (PALlet content LOCalization) – an AI-assisted, adaptive localization solution for automatic depalletizing with robots. It combines a high-performance 3D snapshot camera with a factory-installed and pretrained neural network and a new Deep Learning-based localization algorithm. The system can locate a nearly limitless number of stacked boxes on pallets and provides positioning coordinates for reliable and accurate robot guidance. The integrated neural network has already been trained for a broad range of box types, and new variants can be added at any time with a user-friendly AI tool suite.
Automated palletizing solutions, manual, conventional or robot-assisted – when it comes to ensuring the seamless transport of goods from delivery to shipping or further processing, there are often several approaches to choose from. In this regard, the combination of robot guidance systems with smart camera systems, AI and Deep Learning features – which can accelerate logistics and production processes on the one hand, while reducing the number of monotonous tasks for employees on the other – plays an essential part.
Thanks to its combined 3D stereo and colour imaging, not to mention its browser-based user interface, SICK’s PALLOC is precisely this type of robot guidance system – and one of the future-safest models on the market: first of all, because the neural network’s SensorApp is directly integrated into the camera – and secondly, because the intelligent standalone system can be seamlessly integrated into the control system of nearly any industrial robot or cobot manufacturer’s control system via Ethernet TCP/IP.
PALLOC: Depalletizing with robots and AI
The robot guidance system PALLOC can localize a virtually unlimited number of stacked box and pallet variants, providing positioning coordinates for each box to deliver reliable and precise robot control. The system solution’s 3D snapshot camera can be flexibly mounted on the robot arm or above its operating area, ensuring optimal detection of even the smallest details, regardless of the distance to the box surface. It can produce up to 30 full-color images and 3D image pairs per second in high resolution. This 3D data is automatically compared with the colour data, ensuring that the contours, edges and layer depths are precisely and reproducibly measured and recorded. The preinstalled neural network has been trained for a broad range of box types with varying size, colour, design and printing; as needed, new variants can be added at any time with SICK’s user-friendly AI tool suite, e.g. the SICK web service dStudio for training neural networks.
www.sick.com