www.ptreview.co.uk
14
'23
Written on Modified on
INNOVATIVE MOTION CONTROL SOLUTIONS FOR SHEET METALWORKING MACHINES
Baumüller’s subsidiary in the US will present cutting-edge technological solutions for sheet metalworking machines at booth D41454 during FABTECH 2023.
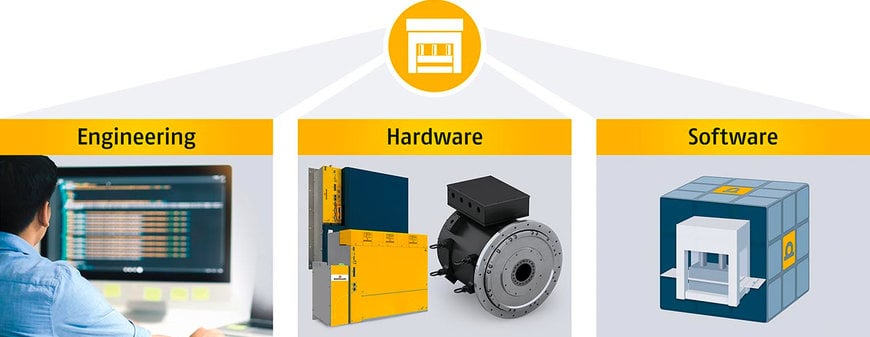
Baumüller offers a complete system for servo eccentric presses consisting of the engineering, hardware, and software
Baumüller will participate in FABTECH 2023. This prestigious event, dedicated to the sheet metal forming industry, will take place in Chicago from September 11 to 14, 2023.
Visitors to the booth will find out why - among other things - servo eccentric presses are the best alternative to traditional pressing methods, what advantages the use of modern simulation technology in the engineering of sheet metalworking machines can offer, and how Baumüller SmartValue can contribute to a permanent reduction of the production's carbon dioxide (CO2) footprint.
Complete drive system for more flexibility
The booth focuses on the overall Baumüller’s solution for the automation of servo eccentric presses. Compared to conventional presses, these presses have the edge regarding productivity, product quality, and flexibility. The machine cycle time, robustness, energy use, and environmental compatibility can be optimized with high-performance direct drives and a compatible control unit. Baumüller has many years of experience providing solutions for servo eccentric presses and, as a full-range supplier, is at your side from the planning to the engineering to commissioning and service.
ProSimulation: The benefits of Industry 4.0 for efficient drive design and minimum connected system load
With ProSimulation, Baumüller offers simulation models of its drive components. The digital twins provide many advantages, especially during the engineering phase: the development time is shortened, and therefore time to market is shortened, maximizing reliability and performance. In addition, Baumüller can undertake the complete design of a motion control solution for a sheet metalworking machine.
This offers numerous advantages, particularly for complex applications such as servo eccentric presses: It enables the selection of an efficient and resource-saving drive package. For example, the whole drive topology can be mapped in the software. This consists of the nonlinear transfer ratio of eccentric mechanics, gearing, high-torque motors, servo drive technology, and energy storage in conjunction with dynamic movement and force profiles. The simulation creates transparency in the power and energy profiles and describes the charging and discharging processes in detail. This enables efficient dimensioning of the energy store, and therefore the connected system load can be reduced. This saves resources, considerably relieves the power supply system, and reduces the machine’s footprint.
Powerful hardware for more power and energy efficiency
Sheet metalworking applications pose significant power, speed, and space challenges. Baumüller offers a broad and scalable portfolio to address these challenges. Our DST2-series high-torque motors provide the power for the most demanding pressing processes. The motors can adapt perfectly to the press’s requirements thanks to different shaft and flange options.
During Fabtech 2023, Baumüller will present the b maXX 5000 product family for high-performance applications. The servo drives impress with their compact design, ample selection of safety functions, and energy recovery option. Intelligent energy management and using capacitors to store energy can reduce the connected system load, saving energy and costs.
Attractive solution: retrofitting a conventional press
The drive system of a conventional eccentric press consists of an asynchronous motor, a flywheel, and a coupling-brake combination. A servo motion control solution can often replace the existing system to get all the benefits of Industry 4.0 and a servo drive-based system. Retrofitting a machine allows for retaining part of the mechanism, and only the drive system is renewed. This solution increases the press's flexibility, productivity, and output product quality. In addition, a retrofit maximizes sustainability by extending the machine’s life and saving resources.
Retrofit of a traditional mechanical press into a servo press
Life-cycle management worldwide
In addition to developing and manufacturing automation components, as a group of companies, Baumüller provides numerous services for plant and machinery manufacturing and machine operators. From project planning, design, and engineering through assembly and commissioning to maintenance, retrofitting, and relocation, Baumüller offers support over the entire life cycle of machines and systems. Baumüller attaches particular importance to the sustainable and resource-saving production of intelligent drive and automation solutions.
Baumüller will participate in FABTECH 2023. This prestigious event, dedicated to the sheet metal forming industry, will take place in Chicago from September 11 to 14, 2023.
Visitors to the booth will find out why - among other things - servo eccentric presses are the best alternative to traditional pressing methods, what advantages the use of modern simulation technology in the engineering of sheet metalworking machines can offer, and how Baumüller SmartValue can contribute to a permanent reduction of the production's carbon dioxide (CO2) footprint.
Complete drive system for more flexibility
The booth focuses on the overall Baumüller’s solution for the automation of servo eccentric presses. Compared to conventional presses, these presses have the edge regarding productivity, product quality, and flexibility. The machine cycle time, robustness, energy use, and environmental compatibility can be optimized with high-performance direct drives and a compatible control unit. Baumüller has many years of experience providing solutions for servo eccentric presses and, as a full-range supplier, is at your side from the planning to the engineering to commissioning and service.
ProSimulation: The benefits of Industry 4.0 for efficient drive design and minimum connected system load
With ProSimulation, Baumüller offers simulation models of its drive components. The digital twins provide many advantages, especially during the engineering phase: the development time is shortened, and therefore time to market is shortened, maximizing reliability and performance. In addition, Baumüller can undertake the complete design of a motion control solution for a sheet metalworking machine.
This offers numerous advantages, particularly for complex applications such as servo eccentric presses: It enables the selection of an efficient and resource-saving drive package. For example, the whole drive topology can be mapped in the software. This consists of the nonlinear transfer ratio of eccentric mechanics, gearing, high-torque motors, servo drive technology, and energy storage in conjunction with dynamic movement and force profiles. The simulation creates transparency in the power and energy profiles and describes the charging and discharging processes in detail. This enables efficient dimensioning of the energy store, and therefore the connected system load can be reduced. This saves resources, considerably relieves the power supply system, and reduces the machine’s footprint.
Powerful hardware for more power and energy efficiency
Sheet metalworking applications pose significant power, speed, and space challenges. Baumüller offers a broad and scalable portfolio to address these challenges. Our DST2-series high-torque motors provide the power for the most demanding pressing processes. The motors can adapt perfectly to the press’s requirements thanks to different shaft and flange options.
During Fabtech 2023, Baumüller will present the b maXX 5000 product family for high-performance applications. The servo drives impress with their compact design, ample selection of safety functions, and energy recovery option. Intelligent energy management and using capacitors to store energy can reduce the connected system load, saving energy and costs.
Attractive solution: retrofitting a conventional press
The drive system of a conventional eccentric press consists of an asynchronous motor, a flywheel, and a coupling-brake combination. A servo motion control solution can often replace the existing system to get all the benefits of Industry 4.0 and a servo drive-based system. Retrofitting a machine allows for retaining part of the mechanism, and only the drive system is renewed. This solution increases the press's flexibility, productivity, and output product quality. In addition, a retrofit maximizes sustainability by extending the machine’s life and saving resources.
Retrofit of a traditional mechanical press into a servo press
Life-cycle management worldwide
In addition to developing and manufacturing automation components, as a group of companies, Baumüller provides numerous services for plant and machinery manufacturing and machine operators. From project planning, design, and engineering through assembly and commissioning to maintenance, retrofitting, and relocation, Baumüller offers support over the entire life cycle of machines and systems. Baumüller attaches particular importance to the sustainable and resource-saving production of intelligent drive and automation solutions.
www.baumueller.com