www.ptreview.co.uk
31
'24
Written on Modified on
Hexagon Automation: The shift from optimisation to innovation
The power of data and AI are extending the reach of automation across the factory floor.
hexagon.com

Automation is undergoing a shift. The industrialisation of artificial intelligence (AI) has given a brain to automated processes. Where once we relied on rigid, pre-programmed systems unable to adapt or learn from past experiences, we can now create dynamic systems that analyse, learn and get better with time.Where it’s remit used to be firmly fixed on repetitive tasks, its scope has now grown significantly. The potential it promises to unleash touches on everything from design to customer. At the factory, it gives us the potential to reach new peaks of production, optimise operations and achieve the goal of producing right first time. Come with us as we explore how the industrialisation of AI will impact key business areas.
Business resilience
An automated system is a fixed system. It cannot adapt or respond to unexpected changes. At various points in its life, every automated system needs human intervention. We can create clever automated systems that work in predictable ways. We can build them to respond to foreseeable events, but there will always be an unknown, or an unpredictable scenario.
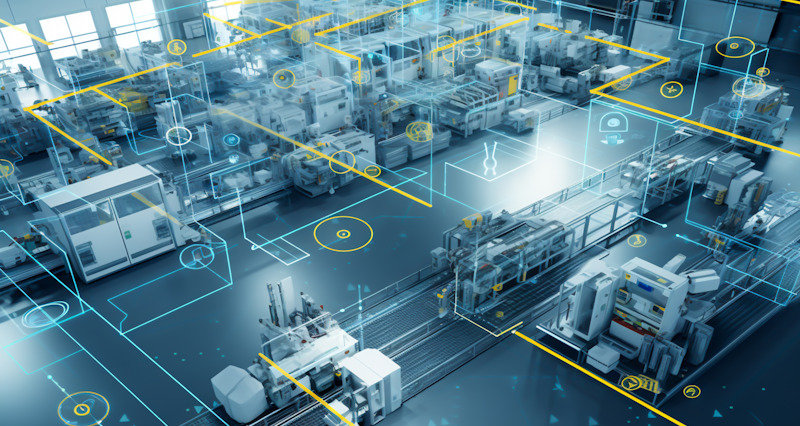
AI allows us to rigid systems into agile systems that support business resilience. By integrating AI with automation, systems have the power to learn from pattern recognition, use data-driven insights and respond to new or changing events. By integrating AI with automated systems we introduce adaptability and flexibility which reduces the need for human intervention and enables a greater level of resilience and agility at the business level.
Design and development
AI is revolutionising the way we design and iterate new products. Generative design tools enable designers to place requirements into software, along with certain parameters like materials, physical dimensions and budget constraints, then the AI generates and presents a number of viable design iterations. The result is not just one solution but many optimal designs based on the original specifications. Unlike humans, generative design has no pre-defined ideas about how a product or part should look – it will simply design something to task. This leaves the software free to invent solutions to problems. The technology is already making an incredible impact across sectors including automotive, where it has empowered designers to do everything from lightweight to improve performance, often by consolidating multiple parts into a single unit. Rather than taking away from designers, generative design is giving wings to innovation by opening up new avenues for exploration.
Factory floor workflows
Introducing the power of AI to traditional automation has the potential to transform production workflows. Instead of just handling repetitive, dirty or dangerous tasks, AI systems can take on a range of much more complex activities. The capacity to learn over time based on real feedback and to recognise patterns and extrapolate makes it excellent at optimising workflows and fine-tuning processes with automatic adjustments of manufacturing assets to ensure quality output.
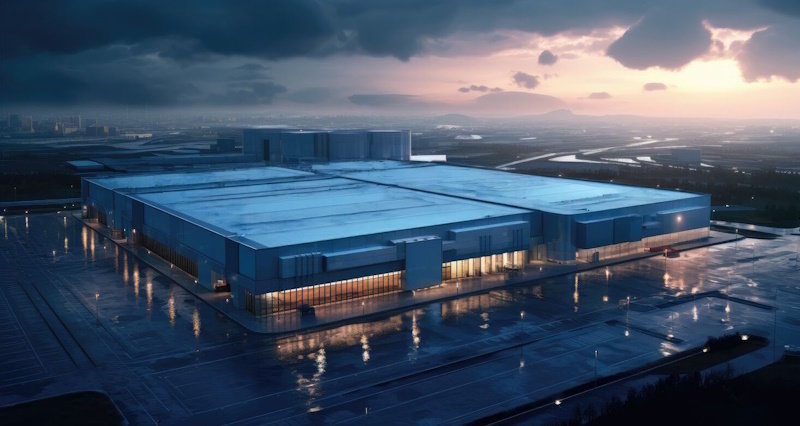
But AI’s value on the shop floor extends beyond efficiency and optimised processes. With the right foresight and vision, it can lead well into the realms of innovation. Efficiency, safety and optimisation almost become a by-product as AI suggests entirely new ways of working. Fully integrating AI into factory floor workflows enables new strategies and techniques which could transform traditional workflows.
Quality control and maintenance
AI is very good at is finding patterns and recognising anomalies. This capability has been used in facial recognition for many years. We see it at airport security and passport control, but now this technology is increasingly applied in the field of predictive maintenance and quality control in production lines. AI can be trained to visually inspect parts as they move along a production line, checking for a range of irregularities, in some cases faster and more consistently than human operators. Additionally, this ability to identify patterns and spot deviations makes artificial intelligence very good at predictive maintenance, recognising changes in the behaviour of a machine that might indicate potential problems. This becomes an indicator to schedule maintenance, all of which reduces downtime and saves costs.
Distribution and logistics
Up until now logistics departments might have used AI to create and identify the optimal way to store, pack and deliver goods. They might have used Ai to monitor and respond to peaks and troughs in demand or to plot schedules based on real-time conditions.
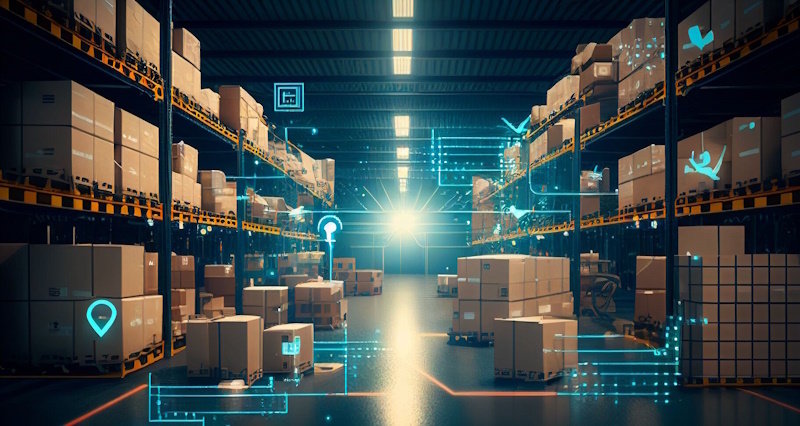
That’s all very impressive, but it is a reactive strategy. To move beyond optimisation and into the competitive advantages of innovation we need to become proactive. This is where AI, and more specifically HxGN EAM (Enterprise Asset Management), come into play. HxGN EAM is an industry-leading asset management solution that uses AI to extend asset lifecycles and improve productivity. It allows organisations to evolve from EAM to Asset Performance Management (APM) by applying technologies such as AI and Machine Learning to deliver accurate, trusted data and strategic insights for improved decision-making.
www.hexagon.com