Sensors solutions that enable advanced control of service robots
Service robots are widely used in various situations such as logistics / transport, security, cleaning, housework, hobbies / entertainment and care / assistance. Since service robots are used in a wide variety of situations, it is necessary to fulfil many requirements such as smooth communication with humans (HMI), ensuring safety and responding to changes in the real time. In service robots, the role of a sensor is very important. In this article, we will take a vacuum cleaner robots as an example.
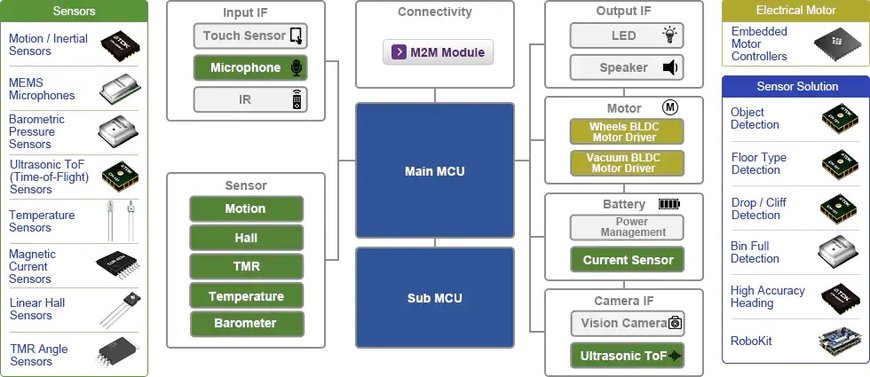
Diagram block - Vacuum cleaner
TDK products for "Vacuum cleaner robot"
The vacuum cleaner robot uses a huge variety of sensors. "Motion Sensor" to detect the position, "Microphone" for voice recognition, "Barometric Pressure Sensor" to detect when the dust bin is full, "Ultrasonic ToF Sensor" to detect obstacles, "Gas and Temperature Sensor" to detect the indoor environment, "Current Sensor" for managing the battery , "Hall and TMR Sensor" for detecting the angle and position, etc. In addition, "Embedded Motor Controller" is designed for the drive of small brush-type, stepper, or brushless motors and can use the integrated MCU as a secondary micro-controller inside the end application. TDK also offers additional Sensor Solutions to support specific application requirements.
Floor type, cliff and obstacle detection
The Floor type, Cliff and Obstacle detection applications are developed to demonstrate and use the capabilities of TDK's Ultrasonic Time-of-Flight range sensors, CH101 and CH201.
The CH101 and CH201 are miniaturized, ultra-low power Ultrasonic Time-of-Flight (ToF) range sensors. the CH101 and CH201 provide accurate range measurements to targets at distances up to 1.2m and 5m respectively. Using ultrasonic pulse-echo measurements, the sensors work in any lighting conditions, including full sunlight, and provides millimeter-accurate range measurements independent of the target’s color and optical transparency. The sensors wide Field-of-View (FoV) enables simultaneous range measurements to multiple objects in the FoV.
Floor type detection application demonstrates floor surface type sensing by using the signal measurements from CH101 modules. The application uses the average amplitude of a reflected ultrasonic signal to determine if the target surface is "hard or "soft".
Presence-Detection application demonstrates the use of motion detection to determine the presence of people and objects.The Presence-Detection application can observe and run with either a single sensor.
Cliff Detection application indicates cliff sensing by using CH101 module, it can configure and operate one or more CH101 sensors.
The above applications can be used in various robotic products like drones, vacuum cleaners, autonomus mobile robots (AMR), humanoids or collaborative robots.
Floor type, cliff and obstacle detection
RoboVac (Software solution)
The RoboVac software was developed specifically for our premium 6-axis motion sensor ICM-42688-P in vacuum cleaner robot application. It is an enablement software to leverage the performance of the ICM-42688-P while compensating for the known weaknesses found in MEMS motion sensors.
Some key features enabled by TDK's RoboVac Software include:
- Leverage ICM-42688-P high resolution (20-bit), precise sampling (RTC) and stability (VLN) and fuse the 6-axis data to provide a precise and stable heading for robot path planning.
- Calibrate sensor bias initially after the robot turned on and before ready to go.
- Estimate fusion degradation over time and temperature and indicate the host to stop for dynamic calibration.
- Dynamically calibrate sensor bias drift over time and temperature time to time.
ICM-42688-P
Sensor fusion & in-use calibration software does matter for robot heading tracking
IMU accelerometer, gyroscope and temperature measurements (from ICM-42688-P) are fed to RoboVac
・RoboVac algorithm:
Evaluates the quaternion for the host application to control the robot movement
Calibrates for sensors errors (bias drift) in order to maintain accurate heading estimation
Commands the robot to stop if new calibration is required
Processing data rate: 1000Hz, 200Hz, 100Hz
・Host provides the robot state as input to RoboVac for potential calibration
・Specs: ≤ 10 deg/hour
・Execution overview
Initial calibration runs only once
Pause every 5~10 minutes
1~2 seconds calibration duration
Motion rejection during calibration
RoboVac Algorithm description
"Dust box full" detection
The level of dust inside the dust bin is estimated by monitoring the flow of air through the dust bin with a pressure sensor ICP-10101. Compared to the air pressure inside the dust bin when the dust bin is empty, the air pressure inside the dust bin begins to drop when the air flow becomes to stagnate due to an increase in suction dust or clogging of the filter.
In order to remove local environmental impacts such as HVAC and detect it more accurately, it is recommended to detect it as a differential pressure that using a similar pressure sensor to measure the outside air pressure.
Dust box full detection
Evaluation results ICP-10101
Embedded Motor Controllers
The HVC flex servo-drive family from TDK enables cost-effective realization of high-performance compact electric motor control. The new HVC 4422F offers extended memory size to address the OEM diagnostic requirements and allows operation in high-temperature environments. An integrated MPU supports RTOS requirements. Powered by a 32-bit CPU core (Arm Cortex-M3), the HVC controllers economically address growing challenges in the robot market and beyond (industrial, consumer, instrumentation, etc.). The flexible peripherals of the product provide all means to directly control brush-type, stepper (bipolar or three phase), or brushless (BLDC) motors directly.
The HVC family further features a flash program memory with a size of 32 kbytes (HVC 4222/4223) or 64 kbytes (HVC 4420F/4422), providing high flexibility in code development, production ramp-up, and in-system firmware update.
Fully integrated single-chip motor-control solution MCU+Drivers for small motors
・ Flexibility for sensored or sensor-less stepper, brushed and brushless DC-motor control.
・ High-performance to enable sophisticated control schemes.
・ Minimal number of external components.
・ Supporting system diagnosis routines.
・ Short development time
¬Easy-to-use development tools and app notes
¬Complete working demos
¬Professional automotive certified firmware package
¬Easy configuration and re-use between different applications
HVC Features
Block diagram - System Architecture
Temperature sensors for robotics
In robotics, TDK's sensors are used for monitoring temperature, which is essential for controlling various functions.
TDK supports high-precision temperature detection with a wide products portfolio.
NTC element with lead
NTC elements are available in the high reliable glass encapsulation, which are the radial lead type with short response time and the easy-to-handle rigid axial lead type. For options, coating of NTC head and leads for high insulation and moisture resistance and lead wire processing that contributes to the simplification of the mounting process are also available.
Bondable NTC chip
The bondable NTC chip is intended to be used in semiconductor devices in which wire bonding is used in charging battery stationary and motor controller for robotics products. Those sensors are directly mounted in intelligent power modules and monitor the power semiconductors junction temperature.
Product onerview of NTC thermistors
Multilayer chip NTC
SMD chip NTC is ideal for on-board temperature detection and temperature compensation with dimensions series from 3216 to 0402. Also available for conductive adhesives.
>>Link to Selection Guide of Chip NTC Thermistors
Temperature sensor assembly / systems
To monitoring the temperature via heatsink of such as IGBT, capacitors, coils in robotics either directly or indirectly, screw-in or screw-on sensors are well-established solutions as they can be easily mounted to the dedicated components. And the air temperature sensors have good possibilities to detect the cooling air temperature and steer the cooling fan.
Please contact us to arrange NTC characteristics, lead length / terminal processing, etc. in addition to standard part numbers.
Product onerview of NTC Sensor Assembly / Systems
RoboKit
The TDK RoboKit is a new development kit that enables seamless integration of solutions from TDK’s portfolio specially designed for the robotics market. RoboKit integrates key TDK offerings such as ICM-42688-P 6-axis Inertial Measuring Unit (IMU), ICP-10111 capacitive barometric pressure sensor, ICS-43434 multimode digital microphone, CH101 and CH201 ultrasonic Time of Flight (ToF) sensors, and Micronas motor controller, angle sensor, and pressure sensors. TDK delivers solutions that meet the rigorous demands of the robotics market, such as heading accuracy of under 10 degrees per hour using InvenSense IMUs and RoboVac software, market-ready inertial navigation system (INS) from Coursa Drive, robust obstacle detection for any color objects in all lighting conditions using Chirp ultrasonic ToF sensor, in addition to robot joint control using Micronas motor controllers. Also included are a temperature sensor and a magnetometer. The TDK RoboKit software also integrates with the leading operating system, ROS. ROS-ready drivers for IMU and ultrasonic range sensor are available now.
www.tdk.com