Low-cost robotization for a holistic approach to advanced manufacturing
The soaring demand on productivity is a significant factor for increasing investments in robotization. Many companies now acquire robots to solve problems, assist humans and support production. Moreover, the lack of labour power is currently the biggest motivation for operating robotization in workplaces in order to achieve customer requirements, and reduce the time from order to implementation. But while the adoption of robotization is increasing, most robots remain out of reach for the small and medium-sized (SME) business due to the high cost. Robotization can make our lives simpler and better, but only if they are affordable. By K.A. Gerardino.
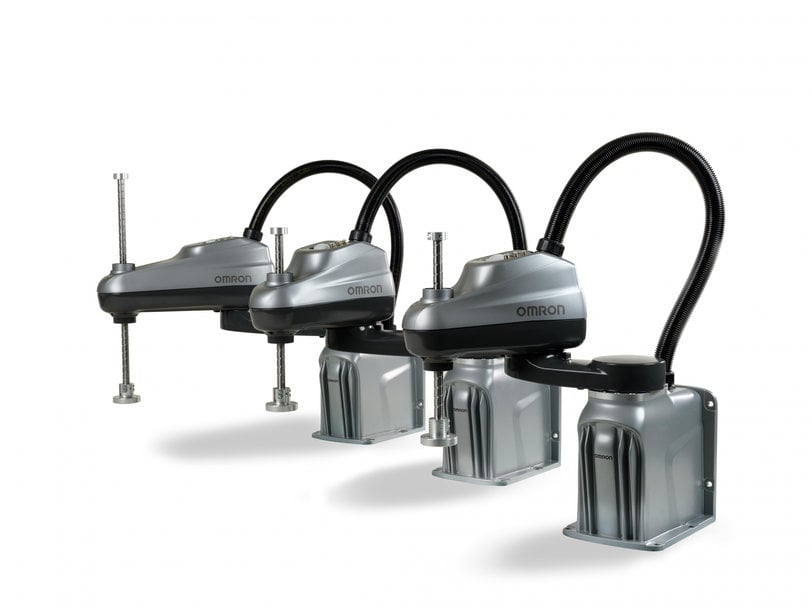
Factors affecting robot cost
Robots are not cheap, and the cost of robotizing one’s manufacturing process can put a huge hole in their finances if they do not approach it without a proper plan. Companies do not go for robots just for the sake of it; they are driven by a need that has to be met, and this comes in the form of the production scope.
When the demand for products goes up, an enterprise must rise to the occasion and make sure they meet it or risk losing their customers to another player in the game. Once they have determined the size of that demand, they can go about procuring the right number of industrial robots for the work. Having this knowledge in advance helps them budget appropriately, which is way better than going in blindly.
The bigger the robot, the more the cost of purchasing and installing. Smaller robots cost less because fewer materials have been used to make them. Bigger robots may operate with the same technology, but the sheer number of raw materials that have gone into them is enough to bump that price up significantly. Then you have the installation cost to contend with on top of having to find enough space for them.
The software is the brain of the robot, the most important part of the entire operation, without which all you have are elaborate pieces of metal. Robotic software is not the same; they go from simple industrial robot programming that handles simple tasks on the manufacturing floor to more sophisticated creations that can multitask without missing a beat. The cost of the software goes up, the more sophisticated the machine. You also must consider the long-running costs of updates down the line to improve their efficiency.
It would be misleading to ignore the influence that a brand has on the price of an industrial robot. The making of robots has been around for decades now, and the companies that were the first to get into the game hold the brand advantage as they are known more and are trusted because of the experience they have. This means that the older the brand, the more expensive their robots and vice versa. Although that does not guarantee that they are better than the recently created brand, it is simply the dynamics of branding that affect consumption.
How independent or dependent are the robots you are aiming for? Can they work on their own, or will they need accessories to function? These are the questions you ought to ask yourself when shopping around for robots. Some industrial robots can hold out on their own, handling their tasks without any supervision. However, there are others that cannot perform at optimum levels without the addition of other related accessories and boosters. These usually come at an extra price, and that should be factored in your plans as you deliberate on which robots to go for.
But in order to best serve the purpose of robotization, it must be affordable so that companies who need them can use them. Yes, robotic arms can be found on many assembly lines, from manufacturing automobiles to preparing meals. Due to increased computing power and advancements in artificial intelligence (AI), industrial robots can be programmed and given complex reasoning ability. More recently, robots have employed sensors to interact with the real world to handle a wide range of tasks.
Although robots have succeeded in finding their place in manufacturing, progress has been slow in making affordable robots. Traditional development processes used by robotics companies result in high-cost production, which is not effective for SMEs.
Cost-efficient robots
Yes, the benefits of low-cost robotization are undeniable. But what about the benefits to the company doing the development? Why is low-cost just as important to them? Using a revolutionary low-cost approach means companies can experiment with new robotics services. It is ok to “think outside the box” when the cost is low; there is more room for the imagination and rapid innovation.
Low-cost robotization development supports a more efficient value chain. When the price to develop and manufacture a product is efficient, the company will be able to provide a superior product. The result is a competitive advantage that is difficult to duplicate. Moreover, if the value offered to the customer exceeds the total of creating that value, a company will be able to reap higher profits developing reasonably priced robotization. If your company’s goal is to improve the lives of your customers and to quickly gain mass adoption, then a cost-efficient solution is important.
The worth of an industrial robot quickly amount to tens of thousands of euros and internal knowledge is often also a requirement. The installation takes a lot of time, the robot takes up a lot of space and in order not to endanger the other people on the shop floor, they must be covered by safety screens. Reasons enough to leave robotisation as it is and to make processes run as smoothly as possible without robots.
So, the choice not to robotize seems justified, but the world around us is changing rapidly. A new generation of robots is emerging and they are perfect for SMEs. This article shows two industrial robot options suitable for SMEs. They are SCARA and Collaborative Robots (Cobots). Both are common types of industrial robots used in manufacturing. These compact robots can automate similar applications, but each have their own set of unique characteristics that make them standout from one another.
SCARA Robot
SCARA stands for Selective Compliance Articulated Robot Arm. These robots got their start in the late 1970s when they were only used to automate assembly applications. Over the years, SCARA robots have expanded their scope of applications to include material handling tasks, such as packaging, light palletizing, and picking. They are also now being used to automate inspection, 3D printing, and dispensing applications.
SCARA robots are smaller, lightweight, compact, and fully automated to handle the same roles that used to be a preserve for the pick and place robotic arm. But all these improvements came at a very costly price. The initial SCARA robots that were made were so costly that having one was impossible for most manufacturers; only the very biggest names in the industry could afford it.
As time progressed, however, more improvements were made, and now there are low-cost SCARA robots in the market that can be procured for less than US$10,000. They are faster, versatile, and can be used for more than just pick and place; they are capable of being repurposed for assembly, material handling, packaging, among many other roles.
The new SCARA robots can be less expensive compared to other robot types. It commands a lower cost due to having fewer components like motors and gearboxes. They are also generally smaller robots which often helps on cost. The lower up-front cost of SCARA robots makes them a great choice for entry-level robot users to begin their robotization journey.
When it comes to speed, efficiency, and flexibility, SCARA robots are the better choice. They are faster, and easy to operate. Below are some of the low-cost SCARA robots in the market today:
Mitsubishi Electric’s RH-CH SCARA robots are in response to machine builder’s demands for lower cost automation solutions. These SCARA robots come in 400mm, 600mm and 700mm reaches and payloads up to 6kg. These light weight, low profile arms are perfect for parts transfer, small parts assembly, automated inspection, and flexible sorting applications. “Our customers are under constant pressure to reduce machinery costs while increasing throughput” says, Kirk Skaggs Director of Sales at Allied Automation. “Mitsubishi Electric provides low-cost solutions that still enable end users the ability to plug the equipment into their Industry 4.0 systems,” says Kirk.
Igus’ new drylin SCARA robot in the low-cost automation range is a perfect solution for pick-and-place and simple assembly operations, such as those used in medical labs and desk-based electronics manufacturing lines. The robot is lightweight at just 20.6kg (RL-SCR-0100 model), features four degrees of freedom, uses stepper motor technology with an encoder to achieve the required accuracy and speed, and can complete a cycle in just three seconds. “The drylin SCARA robot’s main advantages are having a compact structure with a relatively large working area, for its vertical size, while being able to operate in a fast and flexible way,” says Adam Sanjurgo, LCA product manager at Igus.
Omron’s i4L SCARA is a compact robot that offers strong performance at the lowest total cost of ownership. The i4L delivers quality along with scalability, preventative maintenance, and integration flexibility. Thanks to its compact design and small footprint, it is simple to install and can be table mounted or wall mounted without the need for additional hardware or brackets. Its compact design and flexible programming make the i4L ideal for a wide variety of robot applications, including digital assembly. The i4L offers simple integration with unique Ethernet connectivity in the base, and maximum uptime by means of interactive maintenance alarms and an RGB dome light. A status light helps to diagnose problems faster and more efficiently, maximising value in every stage of the product lifecycle. It is ideal for high-speed repeatable applications, and comes with three options of working envelope with reaches of 350mm, 450mm and 550mm.
Yamaha’s YK-XE low-cost, high-performance SCARA family, which handles payloads in the 4kg to 10kg range, contains models with specified repeatability as close as ±0.01mm in X, Y, and Z axes, and ±0.01° in rotation. The YK710XE is an exception. With the greatest arm length in the family, reaching 710mm, it has ±0.02mm repeatability in X and Y axes. The accuracy and precision of these robots allows use in tasks such as positioning tiny mechanical components like small springs or washers, or picking and placing surface-mount electronic components. Their payload capacity also allows them to be used for transfer or assembly of heavy workpieces such as automotive parts. The latest generation of Yamaha’s YK-XE SCARA robots are designed with a new lightened head assembly and enhanced motion control that ensure faster acceleration and reduced vibration. The control strategies Yamaha developed for its SCARA machines automatically optimizes the linear and angular acceleration, considering the arm orientation and the inertia of the payload, to limit the maximum torque, prevent excessive vibration, and enhance controllability. This helps not only minimise the cycle time but also relieves mechanical stresses to enhance reliability.
Yamaha's YK-SE
Collaborative Robots (Cobots)
Cobots offer several advantages over traditional robots and have a unique feature that fits perfectly with the personal development of employees. They do not have to stand behind large safety screens and the risk of accidents is small.
Most of the problems that robotization causes for SMEs do not apply to a cobot. Starting with programming the cobot. With simple software, it is accessible to everyone to program this robot and there is no need to bring in any knowledge to have it perform an action. Also, programming the cobot is not a time-consuming job, this can be done within an hour.
Cobots are robots designed to work safely alongside human workers in factory or warehouse settings. Automation allows them to be programmed for specific tasks like assembly, picking and packing, material handling or quality control. This enables their human co-workers to focus on tasks for which human capabilities are better, such as those requiring reasoning and acquired skills.
Using sensors and complex algorithms, they can be programmed, allowing manufacturers to create custom automation solutions. Unlike other industrial automation, engineering enables cobots to stop when obstacles, including humans, get in their way. Additionally, on rare occasions when they do make impact, the force they exert is minimal, insufficient to cause injuries or damage. Below are top five cobot manufacturers in 2022:
Founded in 2005, Universal Robots makes four cobot models. All its cobots offer six degrees of freedom, allow greater flexibility, and are easily integrated into industrial environments. Widely used in manufacturing, automation applications include quality control and inspection, picking and placing, general assembly, injection molding, palletizing, and packaging. Universal Robots makes the following cobots with varying payload and reach capabilities: UR3e: carries a payload of 3 kg (6.6 pounds), with a reach of 500 mm (19.7 inches). UR5e: carries a payload of 5 kg (11 pounds), with a reach of 850 mm (33.5 inches). UR10e: carries a payload of 12.5 kg (27.55 pounds), with a reach of 1300 mm (51.2 inches). UR16e: carries a payload of 16 kg (35.3 pounds), with a reach of 900 mm (35.4 inches). Cobots made by Universal Robots are generally used for more heavy industrial purposes.
Universal Robots UR3E
Since 2014, Locus Robotics has fabricated custom automation solutions, which enable companies to operate their fulfilment and logistics systems more efficiently. Cobots made by Locus: Allow warehouse workers to pick three times faster. Connect effortlessly with existing infrastructure. Enable warehouses and fulfilment centres to use less labour. Require no reconfiguring, as this is done by Locus. Does not interrupt operations. The company’s LocusEmpower solution allows manufacturers to set cobots for their own operational requirements while continuing with their current pick and pack procedures. This pilot program permits comparisons between new and existing processes to increase productivity.
AUBO Robotics started in 2015 from a collaboration between three professors from China and the United States who were all interested in automation. Engineering a range of intelligent and lightweight robots with load capacities from 3-16 kg (6.6-35.3 pounds), the company developed their i-series cobots to work within numerous industries. With ample configuration options, their cobots’ capabilities make them extremely versatile and capable of performing well across a variety of applications. AUBO’s i-series cobots are used in the production of: automobiles, chemical products, communications equipment, computers, consumer electronics, hardware, household appliances, and medical implements.
Along with their manufacturing capabilities, AUBO’s cobots are also used in scientific research, education, catering, ecommerce, healthcare, and logistics. Their robot arm combines both high-tech and user-friendly solutions, utilizing open-source architecture that supports its use for academic, industrial and research purposes.
As one of the older companies dealing with engineering automation equipment for industry, FANUC started production with a single product in 1956. It began making cobots in 2015 with its CR-35iA, capable of lifting heavy payloads while working alongside humans. The company currently makes eight different cobots, offering diverse options depending on the application. FANUC’s eight cobots have the following payload and reach capabilities: CR-4iA: carries a payload of 4 kg (8.8 pounds), with a reach of 550 mm (21.7 inches). CR-7iA: carries a payload of 7 kg (15.4 pounds), with a reach of 717 mm (28.2 inches). CR-7iA/L: carries a payload of 7 kg (15.4 pounds), with a reach of 911 mm (35.9 inches). CRX-10iA: carries a payload of 10 kg (22 pounds), with a reach of 1249 mm (49.2 inches). CRX-10iA/L: carries a payload of 10 kg (22 pounds), with a reach of 1418 mm (55.8 inches). CR-14iA/L: carries a payload of 14 kg (30.9 pounds), with a reach of 911 mm (35.9 inches). CR-15iA: carries a payload of 15 kg (33.1 pounds), with a reach of 1441 mm (56.7 inches). CR-35iA: carries a payload of 35 kg (77 pounds), with a reach of 1813 mm (71.4 inches). Along with its diversity in cobot models, FANUC’s custom automation capabilities even allow it to automate whole assembly lines.
A leader in industrial automation, Stäubli Robotics is recognized for the safety, effectiveness, and consistency of its automation. Engineering and technical support are above par, while the company’s TX2 range of cobots offers a variety of safety features that allow it to safely work with human coworkers to increase overall productivity. The TX2 range’s safety features include: Safe limited speed: Cobot reduces speed when the operator enters the environment, returning to full speed once the operator leaves. Safe stop: When an operator approaches, the cobot slows, stopping to interact with the operator then starting when the interaction ends. Safe zones: This feature ensures limited arm performance within predefined areas. Safe tool: This supervises cobot’s tools or grippers, along with speed and dimension. Safe touch with TX2touch version: When encountering an operator, the cobot reacts in 10 milliseconds, making any contact harmless. Stäubli’s cobots feature compact arms and large working envelopes that allow manufacturers to optimally maximize workspace. Able to be mounted on ceilings, floors and walls, their various configurations allow easier integration into production lines. As such, they suit a variety of applications in numerous industries.
Conclusion
Luckily, numerous robot manufacturers are finding ways to reduce the cost of their robots through enhanced production techniques. Reasonable prices will also encourage more research and experimentation, paving the way for improved technologies and capabilities in the future. Low-cost robotization will usher in a more inclusive world where everyone can use robotics to make their lives simpler, easier, and better. As robot density grows and adoption increases, we can expect prices to go down further.