www.ptreview.co.uk
03
'24
Written on Modified on
USING AI FOR QUALITY CONTROL DURING PRODUCTION IS A COST-SAVER
Eigen Innovations uses Intel technology to help factories detect defects earlier and control product quality.
www.intel.com
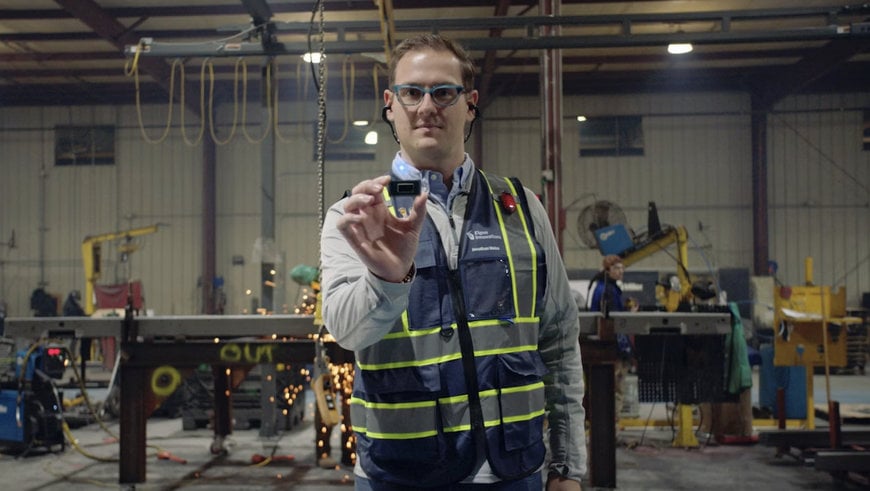
Eigen Innovations, an AI software company based in New Brunswick, Canada, ensures consumers receive high-quality products by helping manufacturers produce defect-free goods in the factory. With the help of Intel technology, Eigen helps manufacturers save time and money, all while increasing customer satisfaction.
Jon Weiss, Eigen Innovations’ chief revenue officer, explains that his company’s automated inspection solutions help manufacturers find hidden defects on their production lines. Recognizing and fixing problems early makes the process more efficient and cost-effective, allowing manufacturers to ensure they complete the best product every time they make it. Rather than conducting random sample quality testing, each part on the production line is reviewed for defects using Eigen’s OneView AI platform.
Quality is King
“The manufacturing industry typically has razor-thin margins,” Weiss says, “and yet many companies don’t know their cost of quality.” When they do add it up, he says, quality “can cost a manufacturer up to a whopping 40% of revenue.”
But Weiss notes that detecting defects is incredibly difficult. Many companies perform sample testing, where they regularly pull products off the production line and check for problems. But since only a small fraction of products are tested, it’s difficult to have confidence in those goods that were not inspected.
That’s where Eigen comes into play. Unlike traditional quality testing, Eigen’s solutions inspect every part, on every line, in every factory. Manufacturers get access to data and insights to help make real-time decisions and improvements that ultimately reduce the cost of quality – and consequently, boost revenue.
Instead of discovering a defect after hundreds or thousands of parts have already gone through the line, a defect can be identified in real time. The manufacturer will know exactly where the problem is, which parts are affected and what error occurred. Eigen’s OneView software can even trigger a signalthat automatically pauses the machine or sends a command to a robot to pull a product for additional testing. And, better yet, AI models are constantly reviewing images of the production line and continuously learning so defects can be avoided proactively in the future.
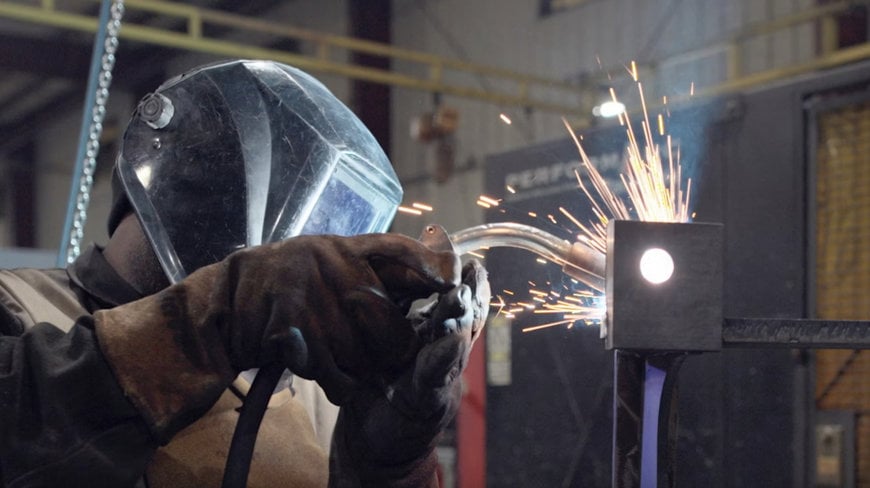
The Need for Speed
Weiss says Eigen’s in-line quality machine vision software, OneView, runs on a “robust hybrid architecture, where data inferencing and closed-loop automation take place within the factory.”
Eigen’s system takes data from across the factory – including PLCs (industrial PCs), cameras, machines and sensors – and consolidates all of it into one traceable digital record. The digital record serves two purposes: It’s used to train patented AI models that help deliver inline inspections and to identify root causes of issues and ultimately improve processes. As you can imagine, the process is very data-intensive.
Ultimately, the cloud capabilities are what customers find the most useful. “Customers have instant access to enterprise-wide improved inspections,” Weiss says. “And once the customer is happy with an inspection model’s level of accuracy, they can do a one-touch deployment across all machines with Eigen’s inspection solution.”
So what would normally be a manual, time-intensive process – including downtime on the factory floor for installation – can now be done with the click of a button.
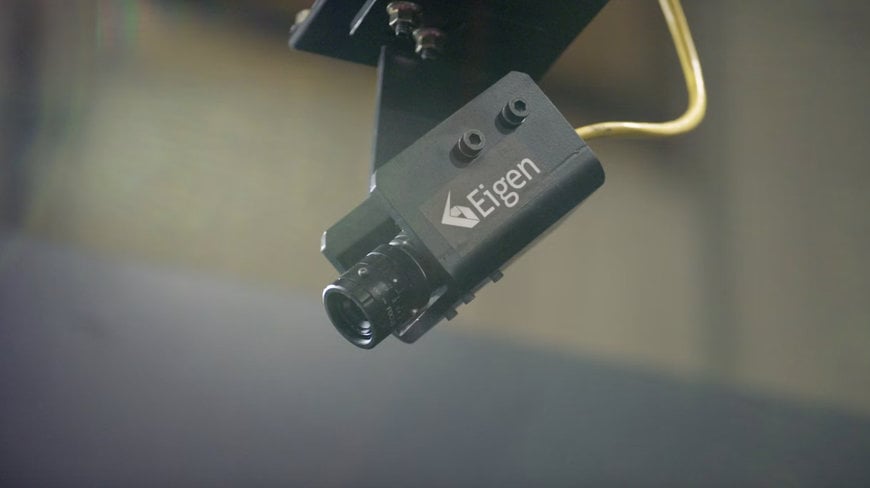
Happy Customers for the Win
Southern Fabricators, a North Carolina-based contract manufacturer specializing in metal fabrication, is an Eigen customer. Known for creating complex product assemblies like components for farming equipment and forklift frames, Southern Fabricators produces hundreds, sometimes thousands, of pieces every day, with each piece made up of dozens of parts that need precise welds.
Here’s how OneView works for Southern Fabricators: When sensors see a problem on a weld and AI confirms the concern, OneView alerts technicians to the potential defect. It will show what happened, with a dashboard of variations in fuse times, temperatures and other relevant metrics to identify the root cause of the issue. The AI models also look at the thermal imagery and determine whether it's a good or bad weld.
Every step of the inspection process is catalogued, providing full traceability down to individual serial numbers. Weiss explains that this full traceability helps mitigate recalls. However, if a recall is needed, the factory can identify which set of products had an issue and only recall the affected products.
Rocky Carpenter, plant manager at Southern Fabricators, says the company has a six- to eight-week lead time on orders, so it’s critical to be agile and swift. The business needs as much predictability as possible, especially with razor-thin margins and long lead times. With the help of Eigen’s solution, Southern Fabricators has saved money (Eigen’s technology paid for itself within six months) and reduced rejects on the shop floor.
Weiss says Eigen’s customers are looking for performance and access to real-time data. And Eigen was tasked with finding a solution that could withstand industrial environments full of harsh tools like high-heat welders.
When exploring options, graphics processing units were ruled out due to debris and heat concerns. In comes the Intel central processing unit (CPU), with its low latency and speedy performance. In the testing phase, Eigen deployed various Intel® Core™ CPUs and the OpenVINO™ toolkit and immediately saw a significant jump in performance.
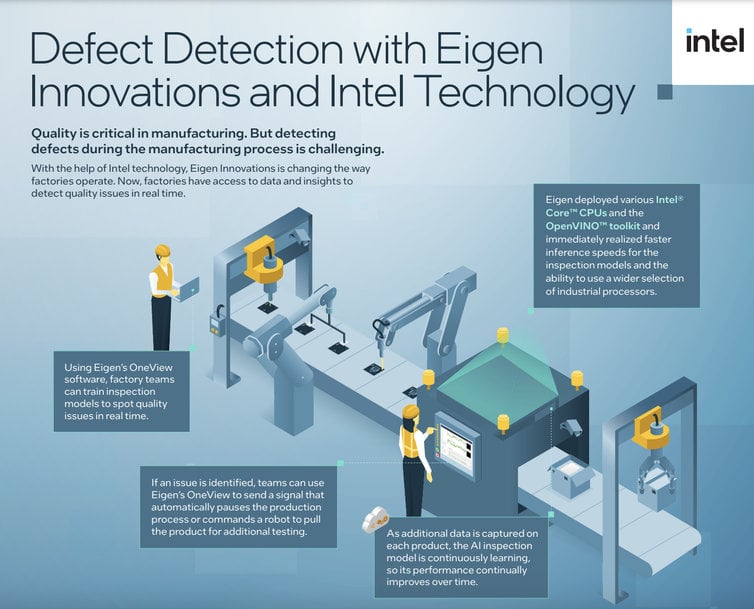
Flexibility is Key
Weiss says what drew Eigen to Intel was a similar approach to flexibility and choice for customers. Eigen wants to give customers “the widest range of deployment options” and that’s made possible by using Intel and its OpenVINO edge technology. He explains that Eigen’s deployment flexibility has ultimately become one of its key differentiators and a strong value-add for its customers. Eigen’s hardware-agnostic approach lets customers choose the hardware that works best for them and seamlessly feeds data into one dashboard.
Another advantage of OpenVINO? Horsepower. Weiss says the speed of OpenVINO is unmatched. He gives an example of a customer that produces specialty paper. In just eight seconds, machinery can build up residue, causing $120,000 worth of damage. Using OpenVINO, “the customer is able to assess, analyze and act within one second, ensuring there is no equipment failure on the line.”
A Competitive Edge
What separates Eigen from other AI software companies is its focus on manufacturing. “We live and breathe manufacturing production environments,” says Weiss. “That’s all we do. We only do inline quality inspection in factories.”
Eigen also employs thermal applications, using cameras to help manufacturers find defects that the human eye can’t see — like its consideration of the quality of a weld. The company’s OneView-managed solutions offer the most comprehensive thermal inspections on the market.
Eigen’s solution is aimed at “simplifying the path of AI adoption without the need for data scientists or writing code,” says Weiss. He explains that Eigen’s easy-to-use technology empowers technicians to resolve potential issues quickly and train AI models at the touch of a finger.
Despite headlines claiming artificial intelligence is replacing people in the workforce, the reality is that many factories are struggling to fill jobs. “If you have any process that is overly dirty, dangerous or dull, it should not be done by humans. It should be automated,” says Weiss. “Let’s get those people doing higher value, higher impact tasks.”
www.intel.com