www.ptreview.co.uk
21
'24
Written on Modified on
KUKA ROBOTS SUPPORT AN INSECT FARM IN DENMARK
Six robots from KUKA are at work on the largest and first commercial insect farm in Denmark.
www.kuka.com
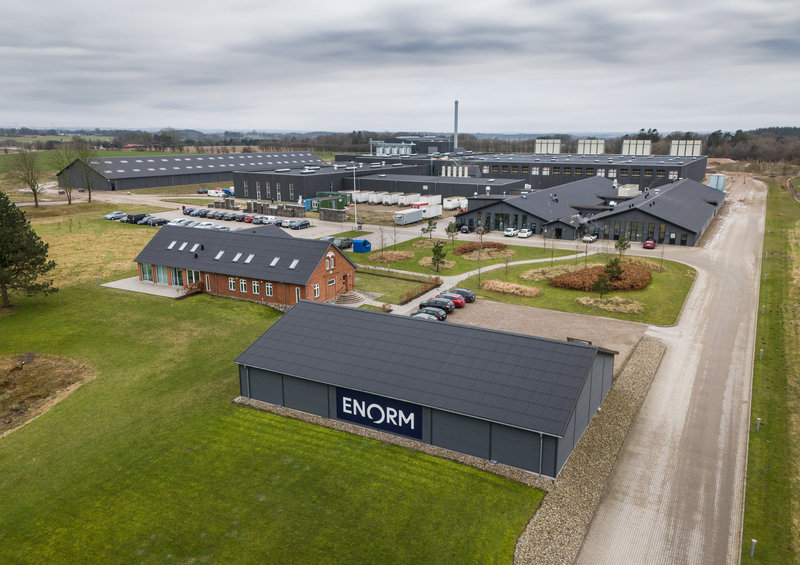
In a factory building in the heart of Denmark, 50 kilometres southwest of Aarhus, a literally moving spectacle can be observed day after day and almost 24 hours a day: Millions of fly larvae munch their way through their food in countless boxes, while the containers are constantly moved, stacked, emptied and filled by quietly whirring KUKA robots.
"The larvae of the fly can feed on almost all organic matter. That's why we can feed them with waste products from the Danish food industry that would otherwise be disposed of elsewhere - and turn them into high-quality feed protein for livestock farming," says Jane Lind Sam, COO of ENORM. Insect production is a prime example of a sustainable circular economy with minimal impact on the environment and climate.
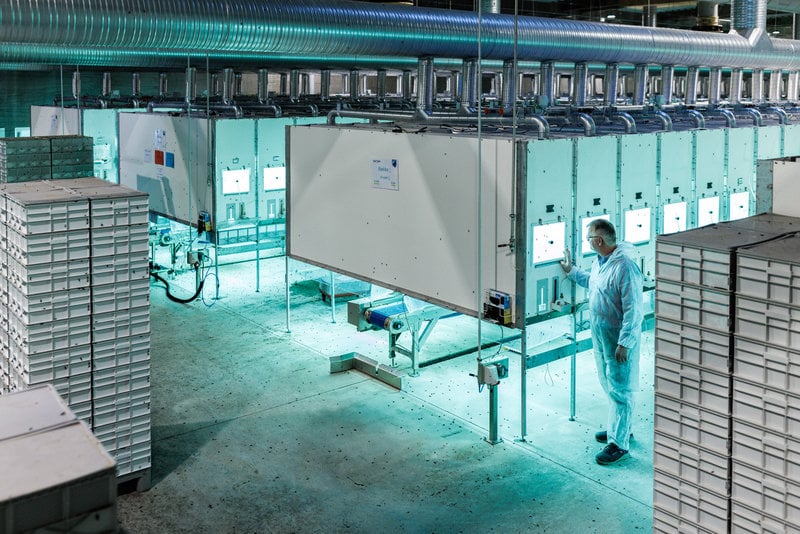
The robots fill a new box every seven seconds
The containers used in larvae breeding are extremely heavy and need to be filled, emptied and stacked quickly. Finding the best solutions for this was the task of Rolf Tange and his team. Tange is CTO of the Sealing System Group, which has been using KUKA technology for its customers for decades.
"We knew that the flexible Hygienic Oil robots from KUKA would be perfect for ENORM's insect farm," says Tange. "In the first stage, the larvae grow in 30 to 40-centimetre boxes," he explains. After seven days, they are then transferred to larger boxes measuring more than one square metre. And at this point at the latest, the robots are an indispensable aid to any human: "There are 50 kilos of liquid food in there, then 70,000 larvae are tipped on top," explains Tange. "Not even the fittest worker could manage that weight."
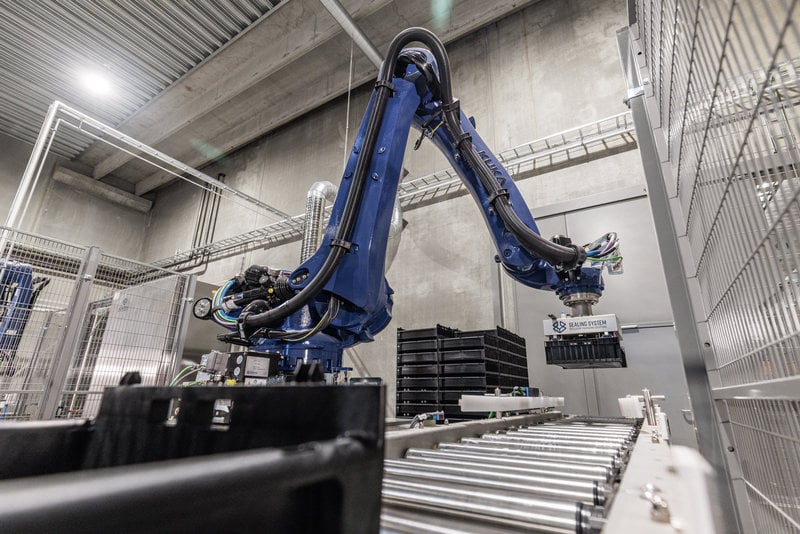
The six KUKA robots fill a new box every seven seconds, i.e. 500 per hour - 20 hours a day. The system is cleaned in the remaining four hours.
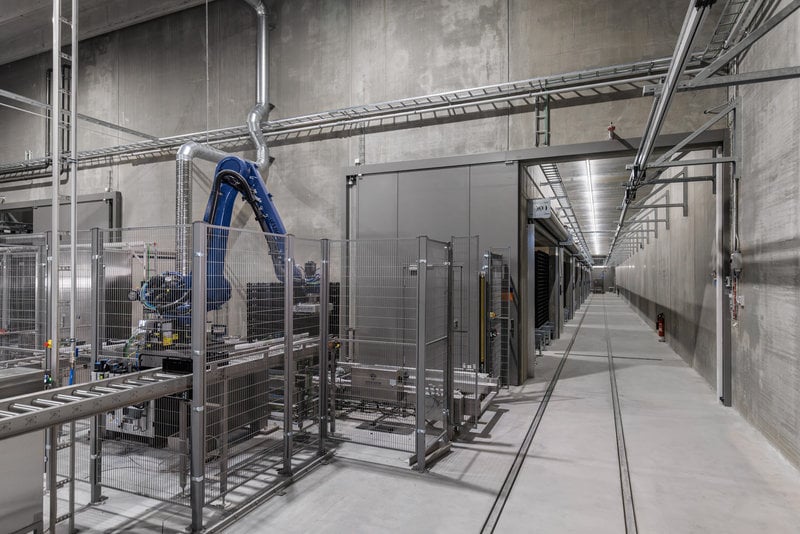
Robot system was simulated with 3D model before commissioning
The Sealing System Group team tested important processes virtually in advance using the software from Visual Components. The Finnish company, which has been part of the KUKA Group since 2017, specialises in software solutions for 3D simulation in factory planning. The software from Visual Components was used to simulate the speed and rhythm at which the robots and conveyor systems have to move.
Perhaps factories like this will soon be everywhere. After all, many experts are convinced that ingredients based on black soldier fly larvae can be produced responsibly and have a significantly lower CO2 footprint compared to other animal protein sources.
www.kuka.com