www.ptreview.co.uk
26
'23
Written on Modified on
Delta line Motion System Solutions for Intralogistics
Modern warehouses feature a variety of machines and systems, including conveyors and autonomous robots, all of which involve motion, largely produced by electric motors, making them a crucial component of modern storage and distribution systems.
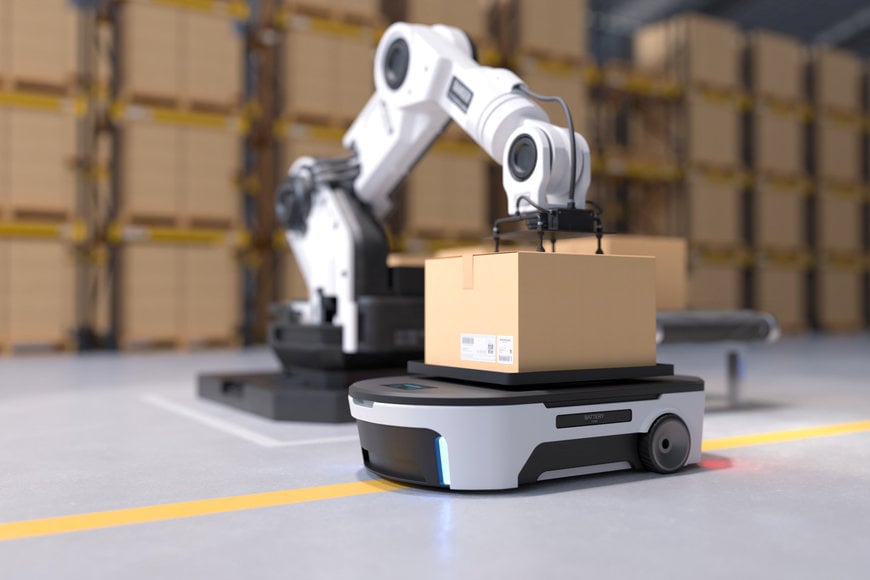
Given the diversity of the equipment, it’s unsurprising that a vast range of motor types – or, to be more precise, motion systems solutions – are needed, each of which must be optimally matched to its application. Achieving this is no trivial task, but it’s one where Delta Line can help, by drawing on its unrivalled expertise and experience in developing, designing and manufacturing motion systems solutions for intralogistics applications.
But what are those applications, what challenges do their designers face, and how can Delta Line help to address them?
With the growing popularity of online shopping in the consumer sector and just-in-time ordering in industry, distribution warehouses are springing up almost everywhere, and, increasingly, they embody a very high degree of automation. Traditional conveyor, diverter and lift systems are still frequently encountered, but now these are often partnered by automatic guided vehicles (AGVs), automatic storage and retrieval shuttles (ASRSs) and autonomous mobile robots (AMRs). Each of these presents challenges in specifying and sourcing the motion systems solutions it needs to function.
Conveyors, for example, need robust drive systems with long operating lives suitable for continuous operation. Wheel drive systems for AGVs and AMRs must be capable of withstanding high radial loads and offer excellent dynamic performance in the smallest possible package. Robot applications require high torque density in a small package at a competitive price.
By no means do all of the requirements relate to mechanical performance. The electronic control systems for the motors must meet requirements for energy savings, easy integration with plant control systems, and safe operation, such as safe torque off (STO) under fault conditions. And, of course, the motion system must be suitable for operation from the available supply, which, in the case of AGVs, AMRs and other mobile applications, maybe 48 VDC derived from a battery.
Another important and almost universal challenge is ensuring that the motion system solutions are available in the required quantities when needed. Given the rapid expansion in warehouse provision, this is an increasingly important concern, with many suppliers of motion systems struggling to keep up with demand.
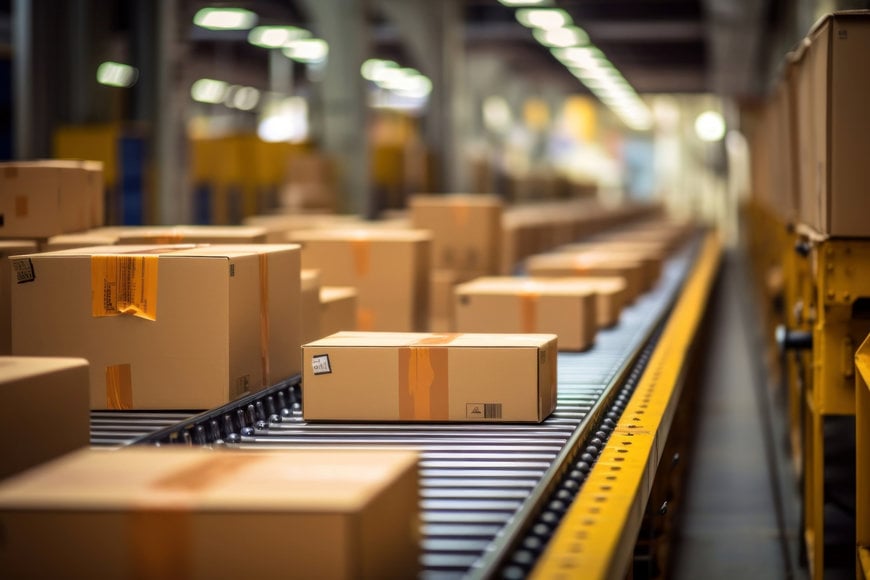
What makes Delta Line different?
First of all, we believe in working in close cooperation with our customers – large and small – to ensure that they get the best solution for their application, whether that’s a standard off-the-shelf product, a standard product with customization, or a completely custom product explicitly designed for the application. Delta Line’s experience and expertise complement the customer’s own, and the combination frequently produces solutions that achieve new standards in performance and value for money.
Delta Line has an extensive product range, including brushless motors, gearboxes, hub wheels, servomotors, linear actuators stepper motors, electronic controllers and much more, so is uniquely well-placed to provide the right solution for virtually every application. The company’s motors are renowned for combining efficiency and reliability with high torque capability in a compact package. Since they are manufactured in-house, they can be readily fine-tuned to suit specific applications.
While it is happy to supply motors, gearboxes and other components for motion systems solutions separately, Delta Line is also adept at developing and supplying complete packages including, as needed by the application, motors, gearboxes, electronic controllers, encoders and brakes. These integrated solutions, which are supplied fully tested and ready for immediate use, simplify ordering and stocking and dramatically reduce build and test time for the customer, leading to lower costs.
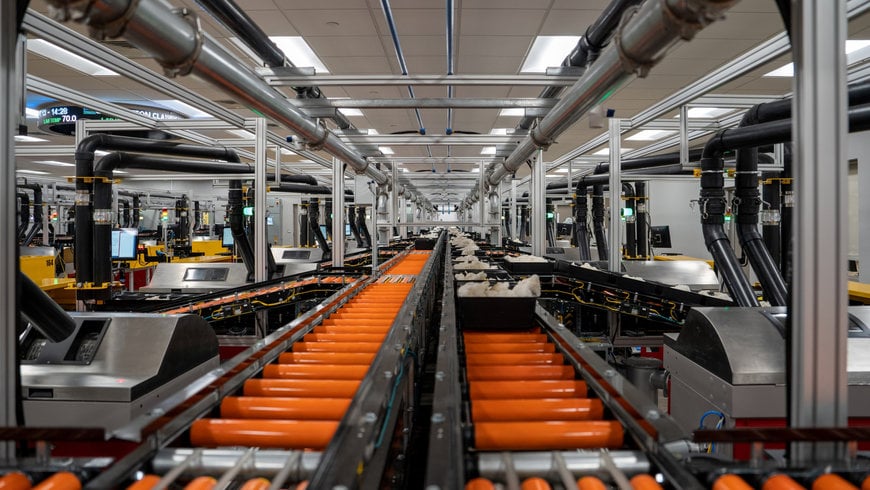
But what about continuity of supply and product availability? And what about pricing?
As one of Europe’s largest manufacturers of motion system solutions, Delta Line can respond rapidly and effectively to peaks in customer demand and is also amenable to holding buffer stocks to help smooth out problems due to component shortages further up the supply chain.
Delta Line's engineering capabilities and deep understanding of customer applications translate directly into cost-effective, precisely tailored solutions for customers. Using a holistic approach allows for identifying and delivering the exact solution that fits customers’ unique requirements - no more, no less. This targeted approach often results in Delta Line's products providing substantial savings compared to other options, regardless of whether they are standard or custom, or required in small or large quantities.
The breadth and versatility of Delta Line's motion systems solutions have yielded incredible results across diverse applications. Below are three real-world examples where Delta Line has substantially impacted the intralogistics industry, from enhancing package handling capabilities for an Italian customer to developing customized solutions for a German client and a new project involving shuttle and lift drives.
Parcel sorting machine: this customer wanted a second source for an existing motion system solution. Delta Line responded by supplying a standard product with minor customization for the mechanical elements, complemented by a new electronic control system developed from scratch. The Delta Line solution offered significantly enhanced performance compared with its predecessor, allowing the sorter to work with packages up to 50 kg, whereas the previous limit had been between 35 and 40 kg. The customer appreciated the high level of technical expertise that the Delta Line engineers could bring to the project and also Delta Line’s very competitive pricing.
Conveyor System: this project was for a new application for which Delta Line developed a fully customized solution based on two sizes of stepper motor, complete with brakes and an electronic control system. As an initial step, Delta Line supplied this international market leader with separate components so that the design approach could be checked and validated. After the customer had completed this evaluation, Delta Line combined the components to produce a fully integrated solution. Once again, the customer commented favorably on Delta Line’s expertise and the keen pricing for both the finished assembly and the development work involved in producing it.
Shuttle and lift drives: for this project Delta Line has provided a customized solution based on brushless DC motors. This application relies on a lift mechanism and a retrieval shuttle. For the lift a BLDC slotted motor fitted with a brake was used in combination with the new standalone Leo controller to drive the whole system. For the shuttle 6 BLDC slotted motors were used, four to move the wheels, one to activate the picking arms and the last one to activate the retrieving conveyor belt. Using the Delta Line Phoenix multi-axis electronic controller means that only two drivers are needed for the 6 motors of the shuttle, resulting in less complexity and smaller space. This innovative design has fully satisfied the customer’s requirements at a very attractive price point.
In the face of an increasingly automated and rapidly expanding intralogistics landscape, the need for efficient, reliable, cost-effective motion system solutions has never been greater. Delta Line's versatile motion system solutions are revolutionizing intralogistics, providing superior performance, exceptional value for money, and outstanding service for many applications. Our commitment to addressing the unique needs of our customers, coupled with our wealth of experience and expertise, sets us apart in the industry.
www.delta-line.com