www.ptreview.co.uk
23
'23
Written on Modified on
Keba:Automated XXL welding
Austrian company igm Robotersysteme AG develops, manufactures and sells robot solutions that are specially designed for the welding of extremely large and/or heavy components where both the welding robot and the workpiece move.

The company is headquartered in Wiener Neudorf in Austria and employs more than 300 people at two locations. igm’s customers include Liebherr, Caterpillar, Doppelmayr, JCB, Bombardier, Stadler, Alstom, to name just a few.
Markets and trends
A third of the revenue comes from the earth-moving equipment sector and another third from railroad car manufacturing; the remainder is earned in the manufacturing of truck bodies and trailers, boiler production and agricultural machinery. “Business is booming,” says Otto Auer, Control Engineering Manager at igm, “but conditions are more difficult than before. We can hardly find any programmers or automation specialists with welding knowledge and experience—this generation has almost died out.”
The trends that igm sees among their end customers include an ever broader product variety; a high degree of customization; ever shorter throughput times; and the fact that there are barely any standards left. There have never been so many specific customer requirements. “Batch size one” has arrived even in this industry. Says Mr. Auer: “Our customers are very focused on topics such as full automation, sensor systems for welding seam identification and tracking, and simulation. Luckily, there exists no process in this area at this point in time that would replace the welding technology, such as 3D printing or bonding.” In addition to the ubiquitous delivery problems for raw materials, green energy is gaining importance (carbon footprint).
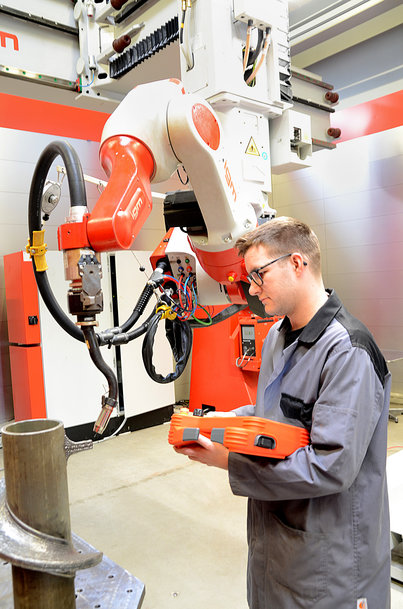
A quarter century of collaboration
igm and KEBA have been collaborating for about 25 years. Their collaboration started with designing a housing for a hand-held operation device and some associated sub-developments.
The collaboration intensified when igm was looking for a supplier capable of providing control systems as well as drive servos for robot controllers including the required safety technology. The market demanded safe axes, safe TCPs (tool center points), and safe speeds—which were also defined in standards. Says Mr. Auer: “Safety technology was the bottleneck. igm was faced with the decision to either develop the safety concept in house, or outsource it to an external provider. But the market did not offer any off-the-shelf design that met igm’s requirements.” igm screened several companies to find a provider who would develop their safety concept, and decided in favor of KEBA. “What was crucial was our existing partnership in which we felt more comfortable in particular regarding the sensitive topic of safety. KEBA is an important partner for us, not least because the company has such a broad base: robotics, controllers, drives, powerful robotics safety, and everything on an open platform.”
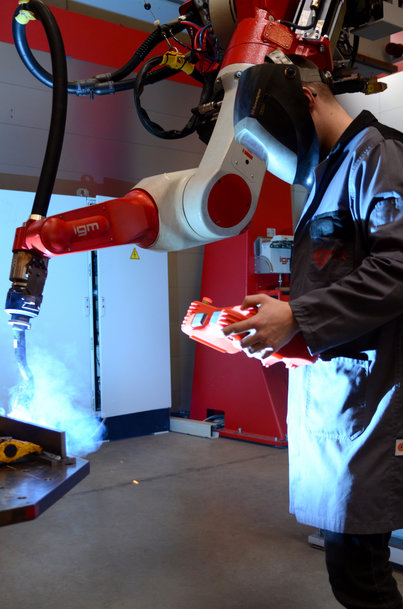
KEBA’s solution and the challenges
There are three features in KEBA’s solution that are particularly important to igm: Firstly, KEBA uses EtherCAT as their bus system (other manufacturers were favoring other bus systems at the time).
Secondly, KEBA provides a sophisticated solution for transmitting the encoder data from the robot servo motors to the drive controllers in the control cabinet. A decentralized encoder box collects the signals at the robots and then transmits them via EtherCAT field bus. This saves a lot of wiring and makes the solution more robust as well as simpler during the entire life cycle. KEBA’s concept is the only product solution of its type on the market.
Third is the fact that a built-in PLC has become a part of the robot controller. Before that, IGM provided their own PLC system (called “soft PLC”). However, the company wanted to focus on its core competency of welding engineering and outsourced the programming of the PLC. Says Walter Schimpelsberger, Key Account Manager at KEBA: “igm benefits greatly from the KEBA platform—it saves them from having to invest in the development of basics such as operating system, diagnostics, safety concept, etc. igm uses the entire range of platform features, permitting them to focus on their core competencies: welding and their own robot path control optimized for welding requirements.”

Partnering with KEBA
Asked to describe the collaboration with KEBA in three words, the answer is unequivocal: supportive, solution-focused, flexible.
Not only does the communication between KEBA and igm work at all levels—from top management to individual software and hardware developers—igm also appreciates KEBA’s great willingness to make changes that igm is looking for. Says Mr. Auer: “We are a key customer, not just one among many. An example that I like to point out is the programming of Safety and PLC as a running process. We were able to say what we need, what is important to us, and we weren't immediately confronted with a standard that can only do this or only do that. With regard to path planning, too, we feel that we are really being taken seriously, and we can see that a lot of developments have been triggered at KEBA.”
And igm still has big plans for KEBA. “Not only will we take the safety approach to the next level, we also plan to integrate parts of KeMotion, in particular a large portion of the path planning feature, and use it to offer safe speed monitoring for all axes,” says Auer.
www.socomec.com