www.ptreview.co.uk
03
'22
Written on Modified on
Aussieker makes use of Four models from DMG MORI for producing high quality workpieces
The company Aussieker Metallverarbeitung GmbH & Co. KG from Preußisch Oldendorf was founded in 1969 as a classic subcontract manufacturer. Right up to the present day, customers in the general machine and plant engineering sector and the medical industry place their trust in the competence of the 30-strong team.
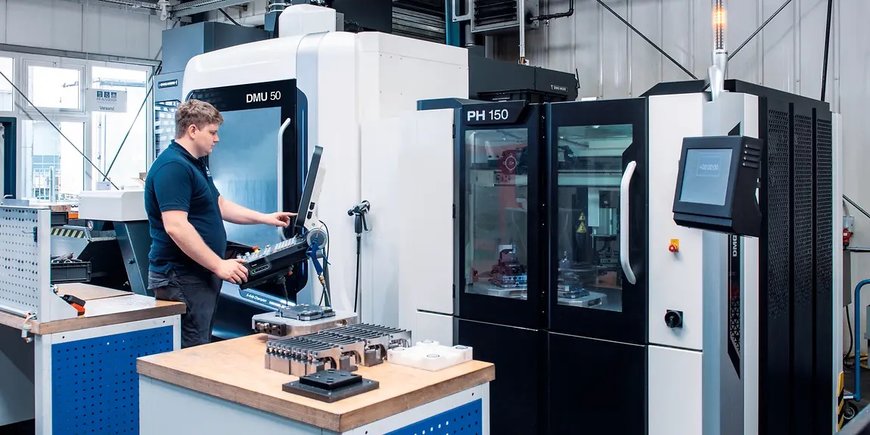
For producing its high quality workpieces, Aussieker uses modern machine tool among which since 2019 are four models from DMG MORI – including two automated machines: a DMU 50 with PH 150 and a DMU 95 monoBLOCK with PH Cell 300.
Combating the skills shortage with automation
“The challenge we face has always been to produce complex and high-precision workpieces as economically as possible”, explains Frank Aussieker. He has led the company of the same name as the second generation Managing Director since 2003. Production requires both modern CNC technology and well-trained engineers. Although Aussieker trains its own future employees in-house, it nevertheless recognises how it is becoming ever more difficult to find good staff. “This makes it difficult to fulfil a healthy order book over the long term – in particular when we sometimes have to work three shifts.”
In view of the growing lack of skilled staff, the company decided to invest in an automated manufacturing solution in 2019. A authorized representative Jan Kleine-Beek recalls the purchase of the DMU 50 with PH 150: “Based on the positive experience we have had with a DMU 100 P duoBLOCK since 2004 and a DMF 260 | 7 since 2018, it was clear to us that DMG MORI was the right partner for this investment.” The move towards unmanned production has helped enormously. “All our employees have to do now is set up new orders, load the automation and then unload the finished parts.” This leaves them enough time to operate other machines. If necessary, the PH 150 is loaded at night or at the weekend. “This only takes a few minutes and ensures that we can more or less produce around the clock and so meet tight delivery times”, says Frank Aussieker.
Prototypes and small series are part of our daily business. Thanks to the PH 150 and PH Cell 300 pallet handling systems, we can respond flexibly.
Frank Aussieker, Managing Director Aussieker Metallverarbeitung GmbH & Co. KG
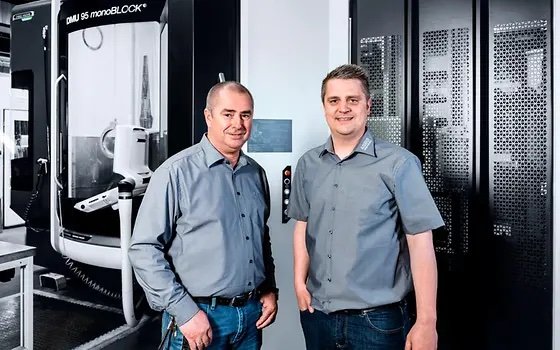
Frank Aussieker (left), Managing Director Aussieker Metallverarbeitung GmbH & Co. KG
High capacity utilization and flexible production thanks to pallet handling
The good experience with the first automation ultimately led to the purchase of the DMU 95 monoBLOCK with PH Cell 300 in 2022. “Compared to the PH 150, the PH Cell 300 offers us additional capacity”, explains Jan Kleine-Beek regarding the purchase of the automation solution, which DMG MORI launched onto the market in 2020. The pallet storage system is modular in design and can be configured specifically for each customer. The version at Aussieker is equipped with a shelf module for 19 pallet storage places – 15 for pallets of up to 300 × 300 mm, and four for pallets of up to 400 × 400 mm. “The storage system is designed in such a way that we can load components that protrude a little over the end of a pallet”, Frank Aussieker goes on to tell us. This means that the large work area of the DMU 95 monoBLOCK c With the PH 150 and the PH Cell 300, Aussieker has confirmed that automatic production is certainly not limited to large series. Quite the opposite: ”Prototypes and small series are part of our daily business”, is how Jan Kleine-Beek describes typical orders. “Thanks to pallet handling we can respond flexibility certainly not.”
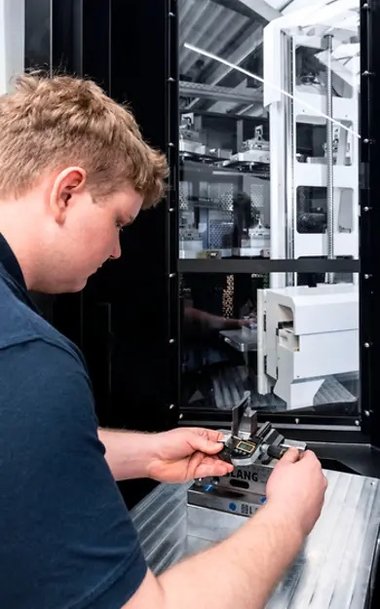
The PH Cell 300 is loaded via an ergonomic setup station.
Reliable production thanks to digital products from DMG MORI
Aussieker also works with digital products from DMG MORI to ensure automatic production runs smoothly. “The DMG MORI Messenger informs us of any unscheduled stoppages during the night and weekend shifts, so someone can drive to the plant and restart the automation”, mentions Jan Kleine- Beek as just one example. We rarely have any serious problems thanks to the integrated tool breakage monitoring. Digitization has also benefited our service, adds Frank Aussieker: “my DMG MORI enables technical problems to be sent to the the DMG MORI service team at the press of a button, so help can be provided via the NETservice or hotline, reducing stoppages to a minimum in many cases. In view of the good order situation, the company depends on reliable production.
Fast amortization
The path to automated production soon paid for itself, sums up Frank Aussieker: “It is quite clear that it has allowed us to combat the skills shortage effectively.” A the same time, machine utilization has increased significantly. “Against this background, automation solutions will play a key role in future investments”.
www.dmgmori.com