www.ptreview.co.uk
14
'22
Written on Modified on
NSK bearings save costs when maintaining ship loading conveyor
NSK has designed a solution using spherical roller bearings that were not only made from its proprietary HTF tough steel, but also featured a detachable nitrile seal. The result was an extension in service life leading to significant savings in downtime costs.
Due to the operating environment, the mining and quarrying industry requires highly reliable equipment that can withstand harsh conditions. So when the bearings on a bend pulley serving a ship loading conveyor had only six months of operating life remaining, the iron ore port called upon the expertise of NSK to devise a better solution.NSK’s team of experts investigated the bearing failure, discovering that heavy iron ore particle ingress and water contamination in the failed bearing’s lubricant had compromised the service life of the bend pulley. Any conveyor components exhibiting curtailed operating life will incur costs for maintenance hours and lost production.
To address the issue, NSK’s engineering specialists set about designing a new solution based on the company’s proven line of spherical roller bearings. In the first instance, NSK decided to manufacture the bearings from its unique HTF tough steel. Tough Steel is an effective countermeasure to the wear commonly found on the outer ring raceway, where the fixed load zone material is prone to wear when experiencing fine particle ingress.
NSK’s long-life HTF series bearings utilise advanced material engineering and heat treatment technology, thus facilitating superior resistance to wear, seizure and elevated temperatures. The outcome is dramatically longer service life and reduced costs for maintenance and unplanned downtime. Indeed, HTF series bearings can offer as much as 10 times the service life in contaminated lubrication conditions, such as those experienced at the iron ore port facility.
Another key design feature of the NSK proposal was removable nitrile seal (HNBR) garter sprung seals, which compensate for seal wear to further extend operating life. The lip contact maintains pressure even under misalignment.
As well as the extension to service life – the NSK sealed spherical roller bearings achieved 12 months of trouble-free operation – the detachable seal provided the iron ore port facility with the ability to check radial internal clearances using feeler gauges during the fitting process.
In short, this notable design feature enables accurate management of the proper clearance as part of bearing assembly procedures. The concept centres on a seal mounted to a ring/holder that is fully detachable (via bolts), providing sufficient access for feeler gauges to perform clearance measurements. Furthermore, this unique design offers complete interchangeability with existing solutions.
At the iron ore port facility, a reduction in lost production downtime was the major contributor to cost savings totalling €77,376 per annum.
1) Ship loading conveyors are critical pieces of port infrastructure, where any downtime can prove extremely costly. Photo: Anita van den Broek/Shutterstock
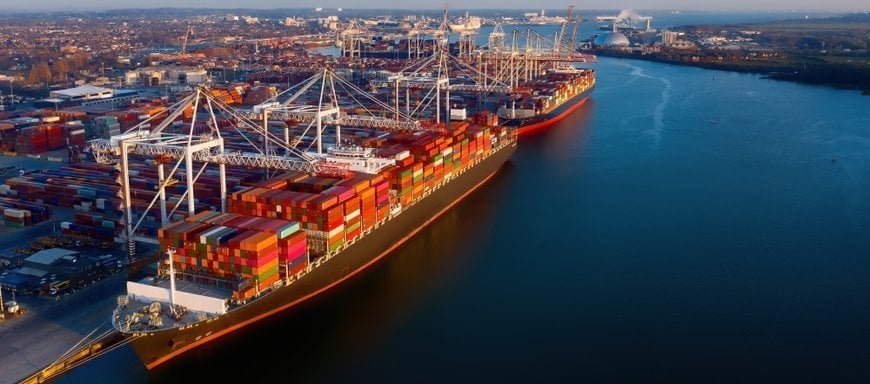
2) NSK spherical roller bearing showing a seal mounted to a ring/holder that is fully detachable via bolts. Photo: NSK
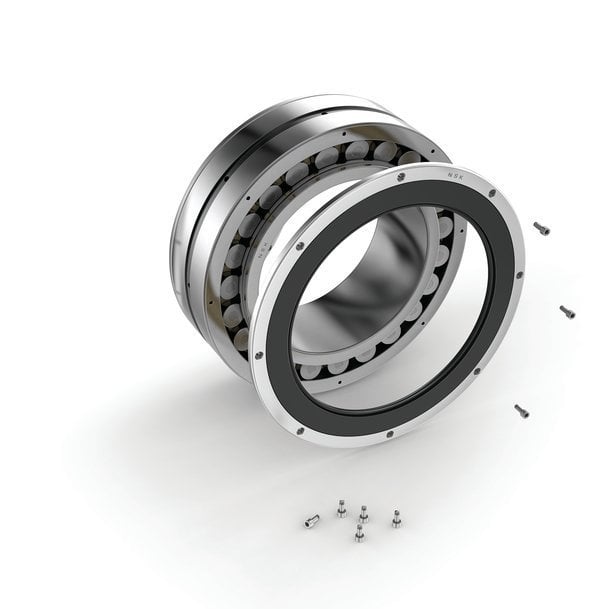
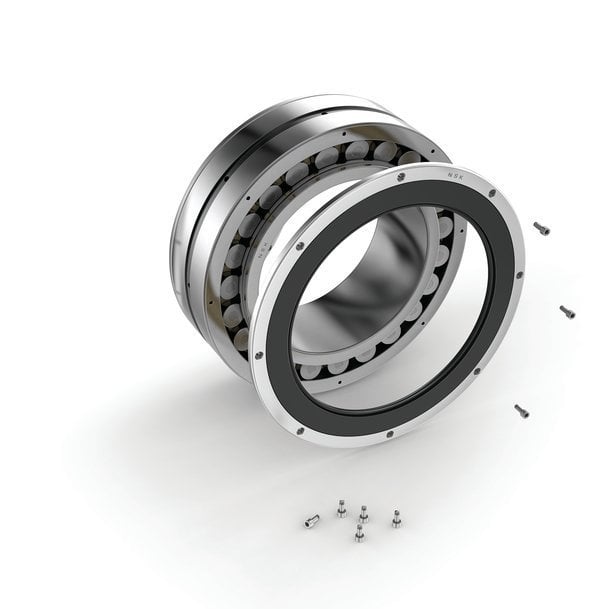